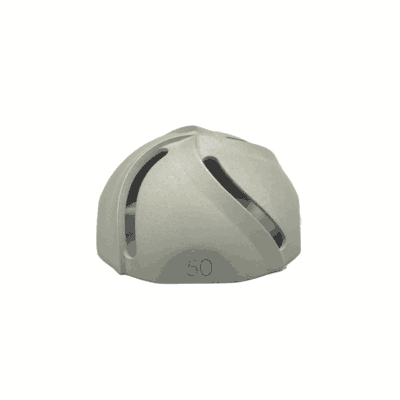
"A Lumafield scanner gives us very quick—and valuable—information."
Summary
- Desktop Metal rigorously tests new materials for use in their 3D printers. Yet the traditional method of studying part internals—mounting & polishing—is destructive and time-consuming; demands on the lab’s resources can back up results for over a week
- Lumafield’s CT scanner provides non-destructive volumetric data, and cuts active sample preparation time dramatically, from days of hands-on labor to a matter of minutes to configure a scan
- Lumafield’s software is user-friendly enough that Desktop Metal can rely on interns to run scans; its hardware compact enough that it can easily be moved as Desktop Metal’s team grows
- Lumafield’s cloud-based technology means Desktop Metal can access a back catalog of hundreds of scans from any computer, anywhere
- The data generated with Lumafield enable actionable insights. Desktop Metal has structured go / no-go logic around scans to accelerate decision making
A Lumafield scanner gives us very valuable, and quick turnaround information.
Jianing Gao, Senior Materials Engineering Lab Manager
Background
Desktop Metal is a company that recognizes the importance of speed. Founded in 2015 with the goal of making metal and composite 3D printing fast and accessible, Desktop Metal’s advanced printing technology has revolutionized how metal parts are manufactured.
To ensure the durability and quality of its printed parts, Desktop Metal engineers and materials scientists rigorously test the performance of new materials and processes in their lab. 3D printing metal parts is an exercise in precise layer-building, explains Jianing Gao, Senior Materials Engineering Lab Manager at Desktop Metal. Engineers take special care to test and analyze inter-layer porosity for any material in development. “Success is when you can’t see any visible porosity,” she says.
The traditional method of testing microstructures, however, is destructive and time-consuming. Samples are mounted with a polymer coating and must be painstakingly polished prior to cutting and analysis. The resulting sample reveals only a 2D plane of a 3D object. “If we cut through the pores, good, if we don’t, it could be a false negative,” explains Gao. To process a sample this way, she says, engineers must place a sample in a queue with at least a weeklong wait.
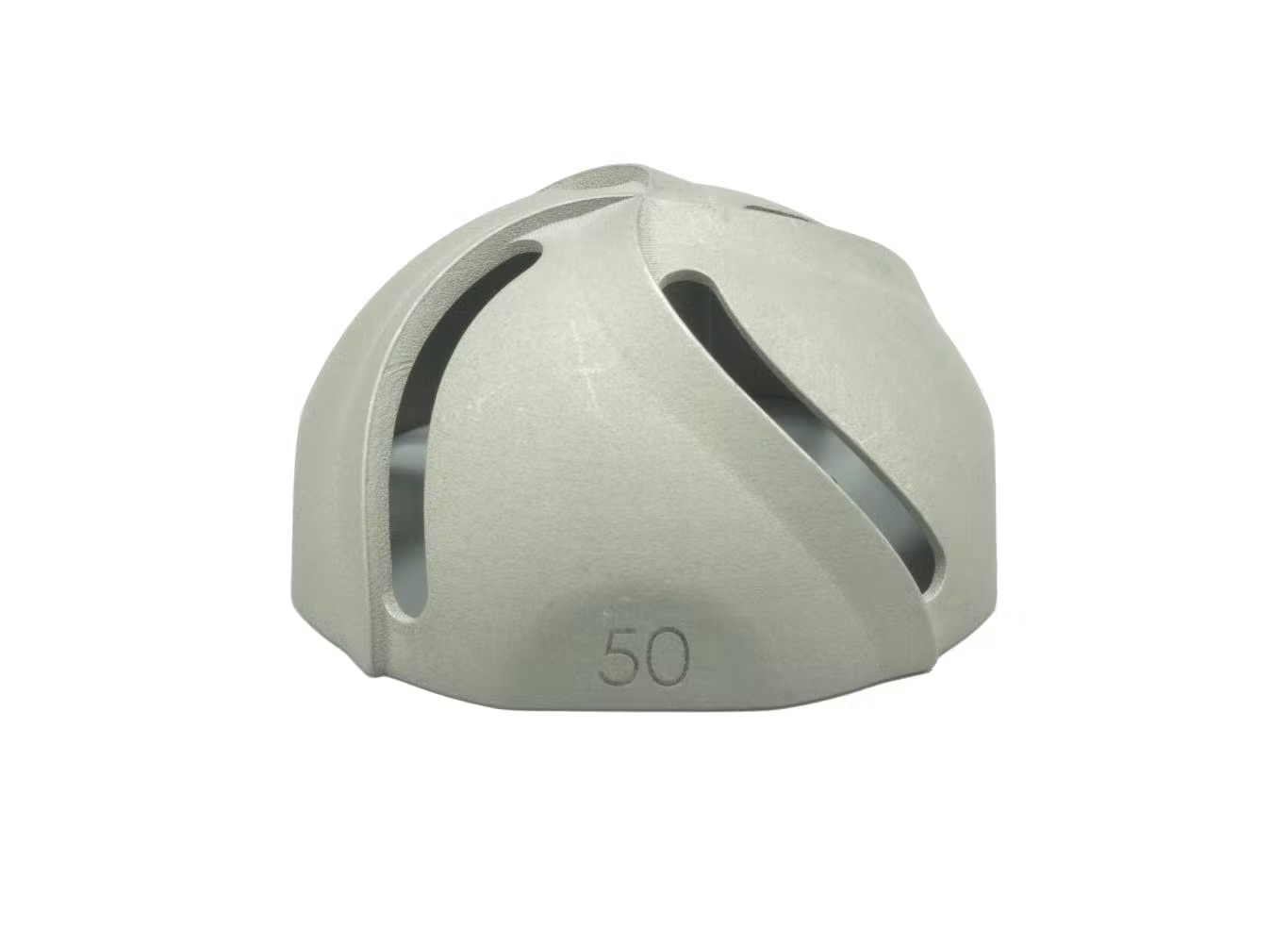
Desktop Metal + Lumafield
CT scanning with Lumafield has been crucial, Gao says, in giving Desktop Metal “a non-destructive way to see the porosity inside something, a part that otherwise we would have to cut open.” Most importantly, she says, “it’s a lot faster. Usually, a CT scan takes 2-3 hours and you can go about your decision-making right away. Even if you want finer resolution, the scan is done overnight.” Only a few minutes of active work are required to configure a scan, freeing up Desktop Metal’s team for other efforts.
In addition to speed and accuracy, Lumafield’s platform offers ease of use and flexibility, crucial for a fast-growing company. “I enjoy working with Lumafield’s team,” Gao says, “It’s very agile and very responsive.” She adds, “The software is easy and intuitive to use.” Desktop Metal’s interns are able to come up to speed after one or two sessions with the machine, making it possible to run the scanner without needing to hire a dedicated operator. And with its compact footprint, Lumafield’s scanner has been easy to move around the office as the Desktop Metal team has expanded and their office layout changes.
“It’s nice to have the cloud-based platform because all the images are there. It’s certainly the right mindset to go cloud-based for Lumafield,” says Gao. Instead of grappling with file management or external hard drives, Desktop Metal’s engineers are able to share and access its terabytes of data across hundreds of scans from any computer, wherever they are.
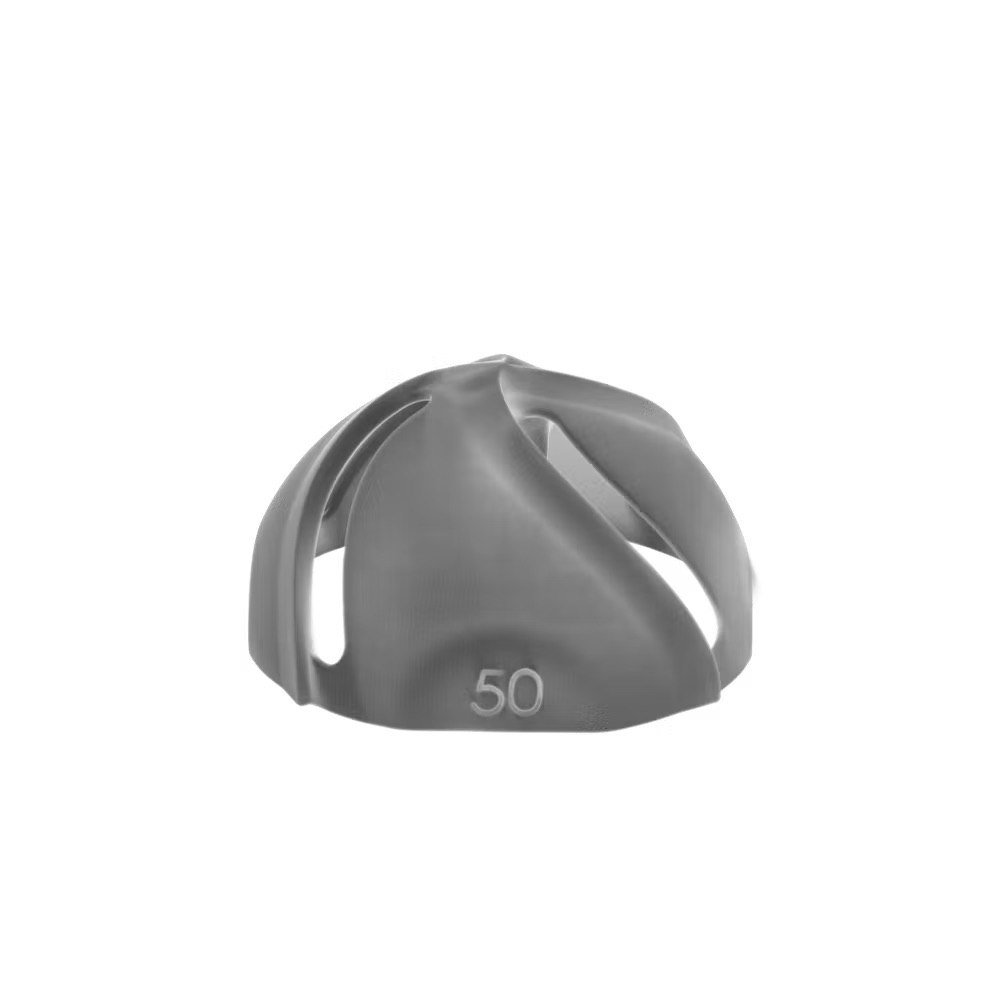
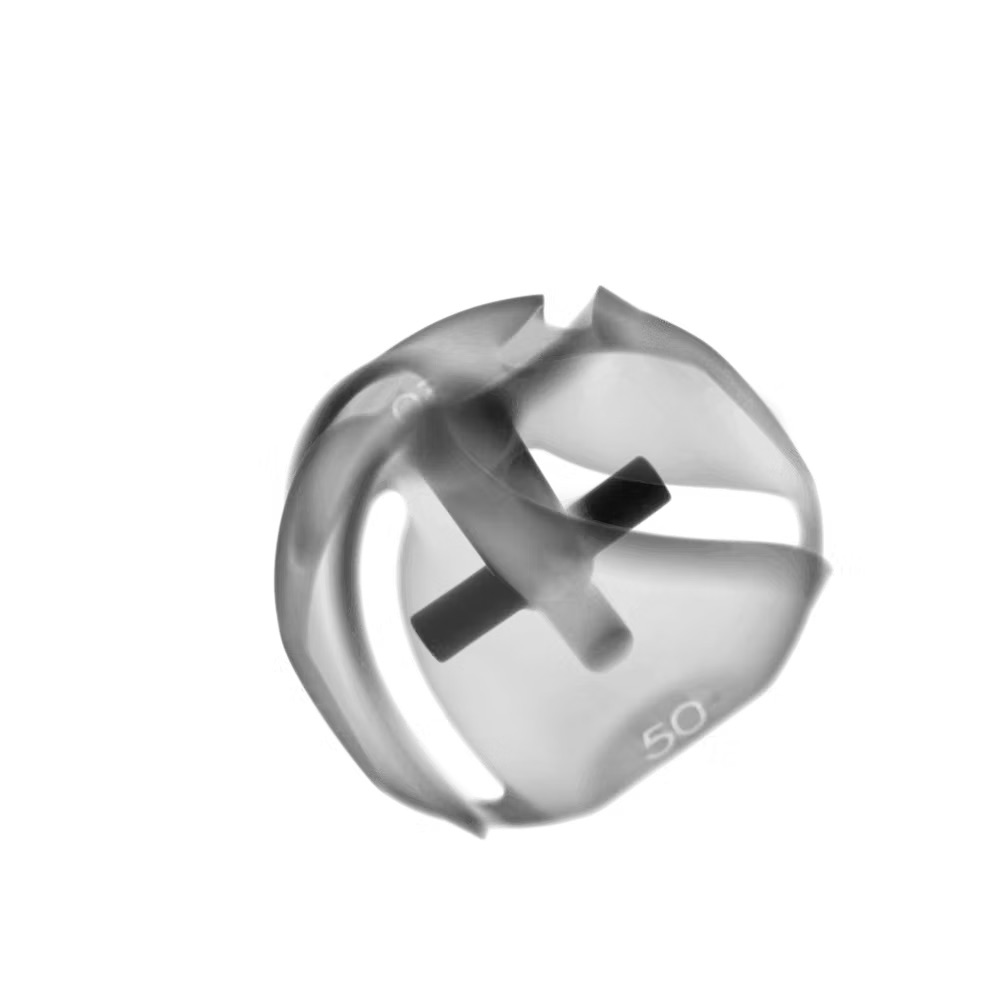
New Data. New Insights.
Engineers on Gao’s team now rely on Lumafield’s data to perform go / no-go tests for the materials they’re analyzing. The swift turnaround of new data allows for the swifter generation of new insights. The data from the CT scans are “critical,” says Gao. “We use Lumafield, we’re able to see what’s going on inside.”
“A Lumafield scanner gives us very quick—and valuable—information. With the versatility of this instrument we certainly would like to see if we can use it in other applications,” says Gao.