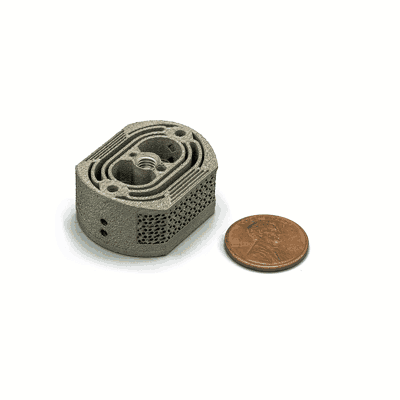
"I was able to have a meeting with our customer, log into Lumafield's software, and show evidence that prompted a design modification."
Summary
- rms Company helps develop and scale the production of medical devices with additive manufacturing (AM), providing their customers the freedom to design complex features such as lattices.
- Engineers taking advantage of generative design tools can scale a single product design strategy into tens or hundreds of SKUs. Checking the print viability of all iterations is time-consuming.
- Generative methods can lead to features that do not print well, such as incomplete lattices or trapped powder. Cross-sectioning to inspect these features destroys the sample, is time-consuming, and provides limited data.
- rms Company is investing in Lumafield’s computed tomography (CT) scanning to digitize the physical output of AM as a cost-effective inspection method. The scans allow non-destructive slices to inspect lattices, porous structures, and other generative design components.
I was able to have a meeting with our customer, log into Lumafield's software, and show evidence that prompted a design modification.
Ryan Kircher, Senior Additive Mfg. Engineer
Background
rms Company, part of the Cretex Medical family, is a trusted supplier to the top medical device companies in the world. While its expertise goes back to its founding in 1967, the company has invested in the future by adopting additive manufacturing for mass production. “rms Company prides itself on building processes that are able to scale up to runs of 10,000 parts,” said Brett Sobczak, additive manufacturing engineering manager at rms Company. Direct metal printing, often in titanium alloy Ti64, allows rms Company to produce geometries that were traditionally impossible to manufacture. These advances enable their customers to leverage advanced design methods and move past the old limitations in manufacturing.
Lumafield + Rms Company
However, the advantages of additive manufacturing also bring about challenges in inspection. The methods for implant inspection are varied – machined geometries historically require programming a coordinate measuring machine (CMM). Generative geometry inspection requires destructive sectioning of parts, polishing operations, microscopes, and photography. Inspecting a finished implant will require utilizing both of these time-consuming methods.
The additive manufacturing team at rms Company has been looking at technologies such as CT to move beyond these limitations. “People have been informally using CT in this industry for years now,” noted Ryan Kircher, rms Company's senior additive manufacturing engineer. Instead of an engineer or technician destroying a sample to conduct metallography on a cross-section, a CT system captures the whole part without requiring labor overhead. CT scanning is both more cost-effective and ensures that engineers see what matters.
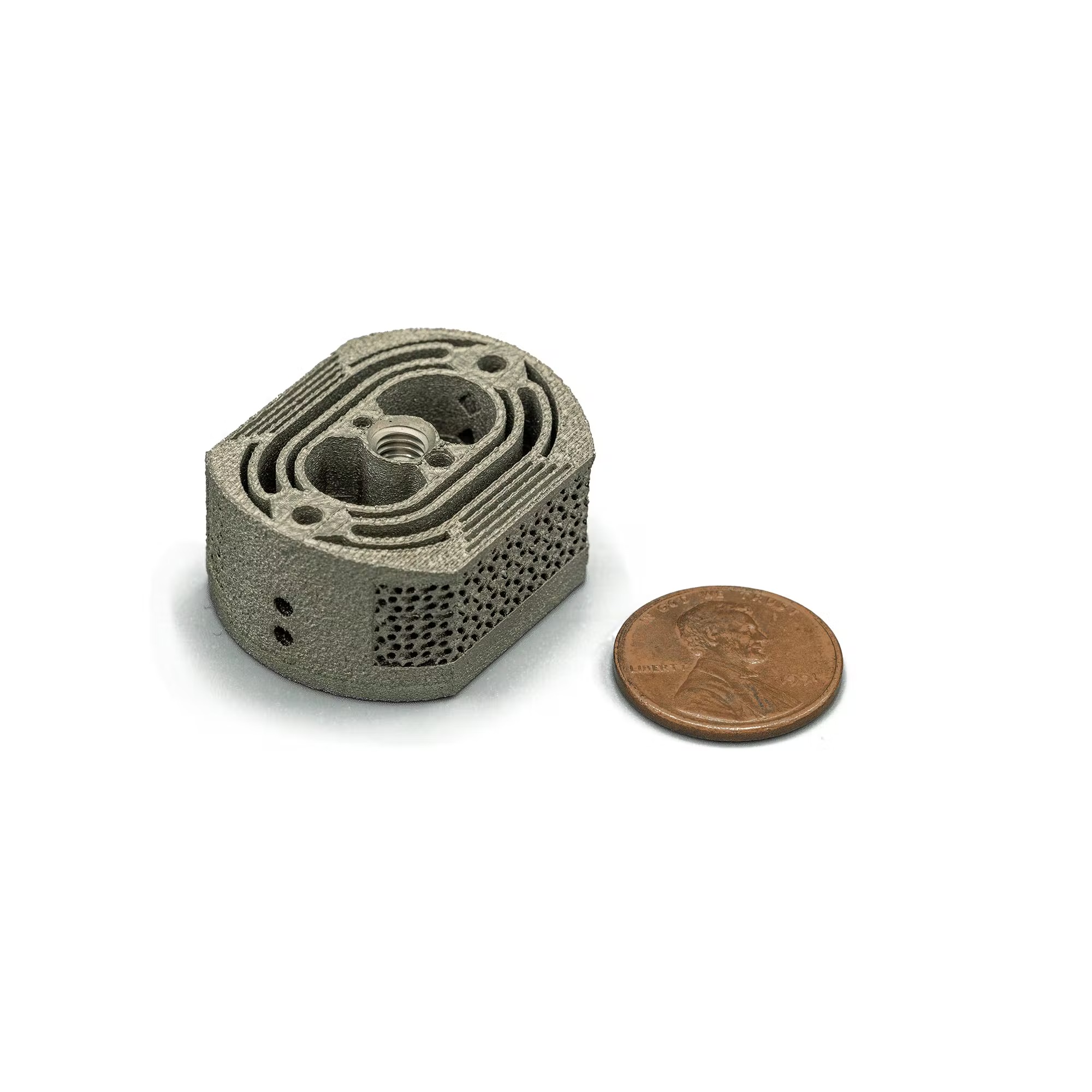
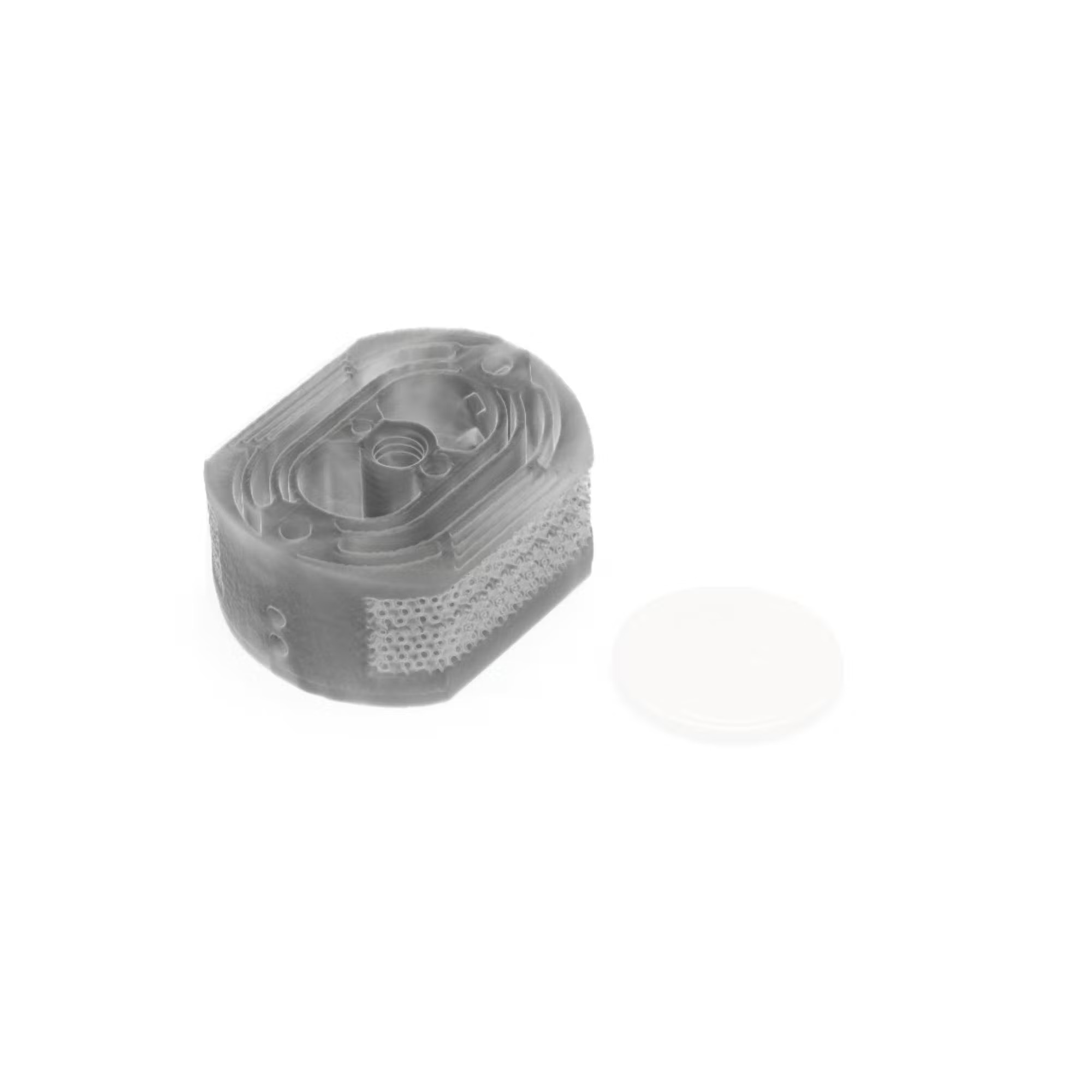
Inside The Lattice
CMM machines provide accurate measurements of surfaces but require skilled operators to program. Sobczak estimated that programming a CMM inspection routine can take a technician as long as a day, depending on the part. The time requirements create challenges when scaling a product line. Kircher says, “a single spinal implant product can have over 100 different SKUs” when designers use an algorithm to make incremental sizing changes.
Further, this effort does not provide complete coverage of the part. “A lot of people will only focus CMM inspection or gauging on machined geometry. The lattice remains a black box,” noted Kircher. By CT scanning, rms Company increases qualitative inspection coverage with fractions of the effort required in the past. “We are changing the thought process and culture around additive manufacturing in medical implants,” added Kircher.
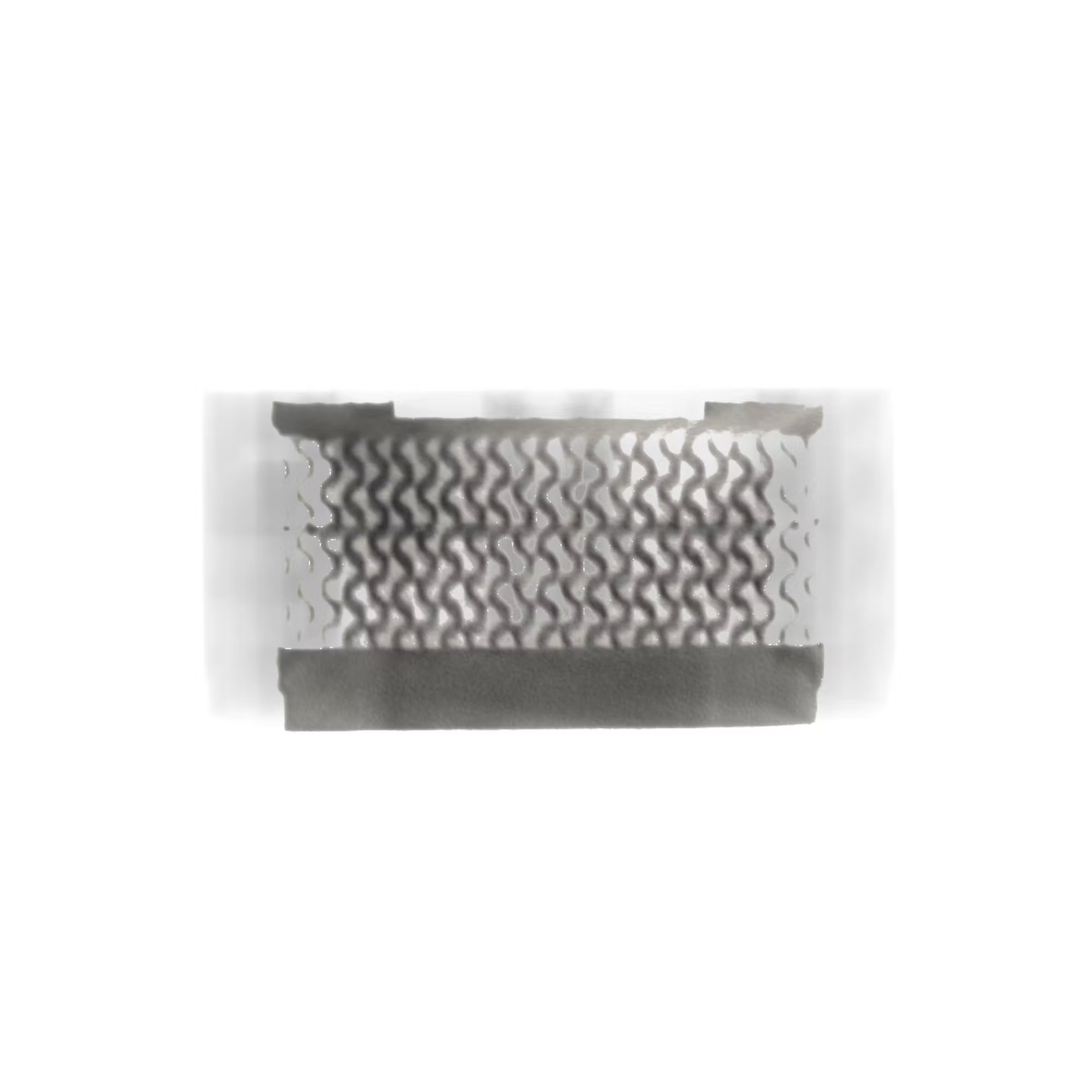
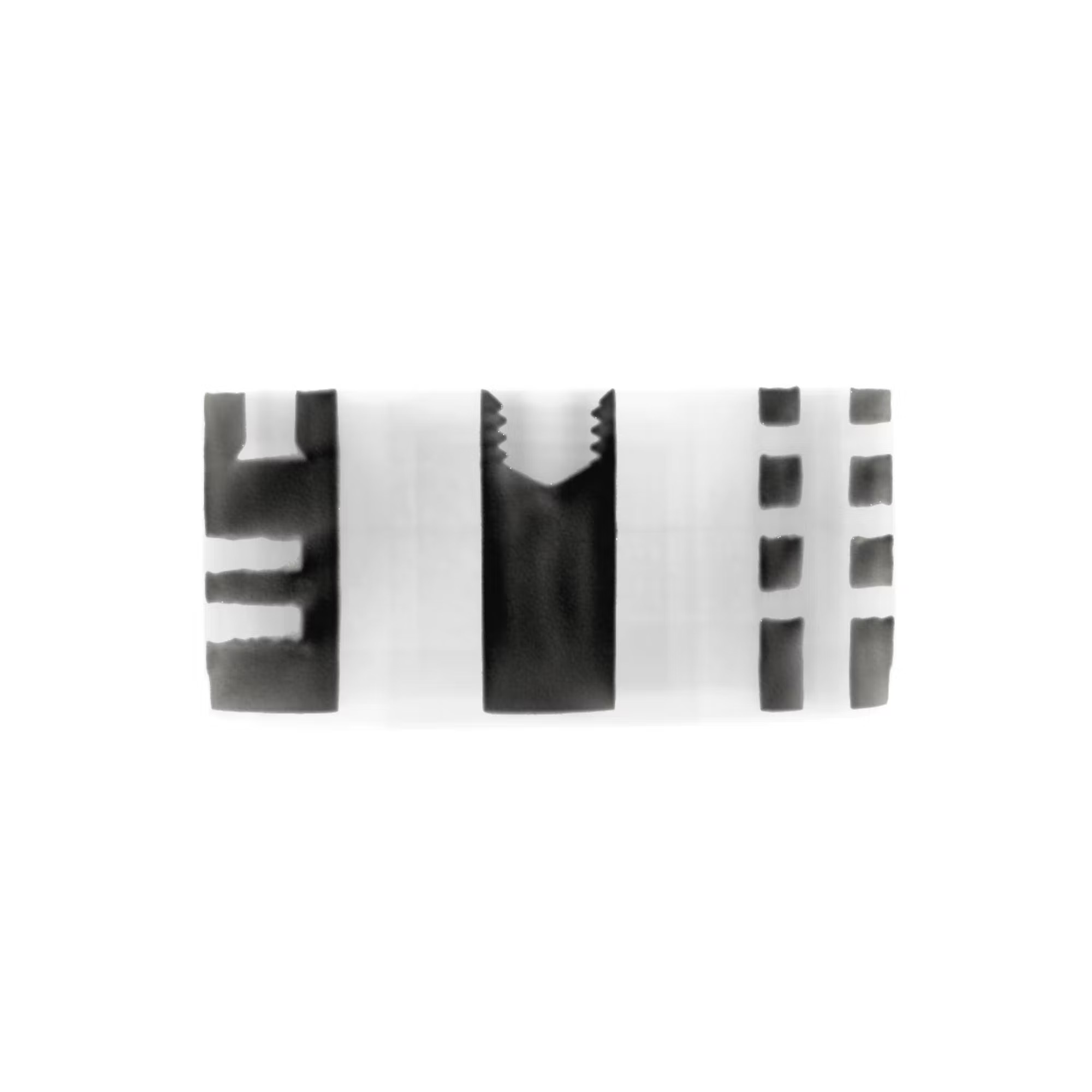
In one recent case, rms Company used CT to scan a part that a customer had designed using a generative algorithm. The scan revealed an incomplete lattice. "I was able to have a meeting with our customer, log into Lumafield's software, and show evidence that prompted a design modification," Kircher said. The case showed how "being able to get information for the entire region of lattice structure is invaluable," says Ryan.
In the past, such an interaction would have unfolded very differently. rms Company would have had to cut the part in half and send the customer a picture. But even then, Ryan says, the question would have remained: "Is there another defect somewhere else besides where you cut it?" After using the solutions from Lumafield, Sobczak was quick to add, “I don’t think there is another option.”