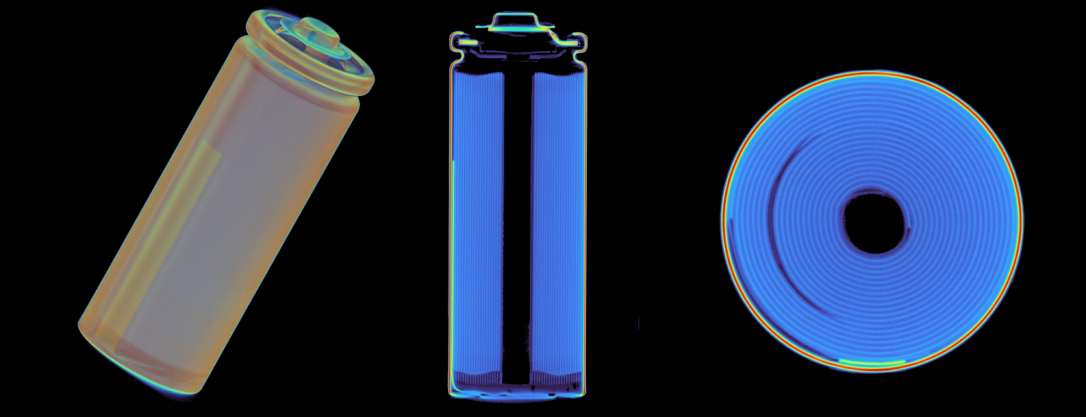
A global CPG leader streamlined battery quality control by replacing costly outsourced inspection.
Summary
- A global CPG leader streamlined battery quality control with Lumafield's Neptune CT scanner, replacing costly outsourced inspection.
- Neptune exceeded a 350% ROI while enabling critical supplier audits.
- Lumafield's Voyager analysis software provides detailed battery insights unattainable with 2D X-rays, ensuring comprehensive product reliability.
- Lumafield's technical support optimized scan settings, guaranteeing consistently high-quality results for the engineering team.
Background
Our customer is a multinational CPG corporation best known for its flagship personal care products found in bathroom cabinets and kitchen cupboards around the globe.
Their 60+ brands produce many of the most trusted oral health, home care, and beauty products on the market and bring in nearly $20B in annual revenues.
A Better Way to Test Batteries
A number of the company’s products, including electric toothbrushes, are powered by rechargeable lithium batteries. The company currently sources around a dozen different battery types from three different vendors for these products and must frequently run quality assurance testing on them. This testing has historically consisted of a combination of outsourced CT scanning, in-house X-ray scanning, and destructive teardown testing.
Each assessment cost the team more than $30K in CT scanning alone and often left the company’s engineers with unreliable, poorly filtered scan data. The high cost associated with outsourced CT scanning also caused the engineers to halt their yearly audit of battery suppliers—an annual expense of around $120K—and shift their testing to focus on highly imprecise X-ray scanning.
We had been looking at the batteries in our X-ray machine, but the X-rays can’t give us the kind of details we need to properly evaluate a lithium battery. X-ray helped us identify some really egregious quality issues, but we quickly realized there was no substitute for CT scanning.
— Director of Product Compliance
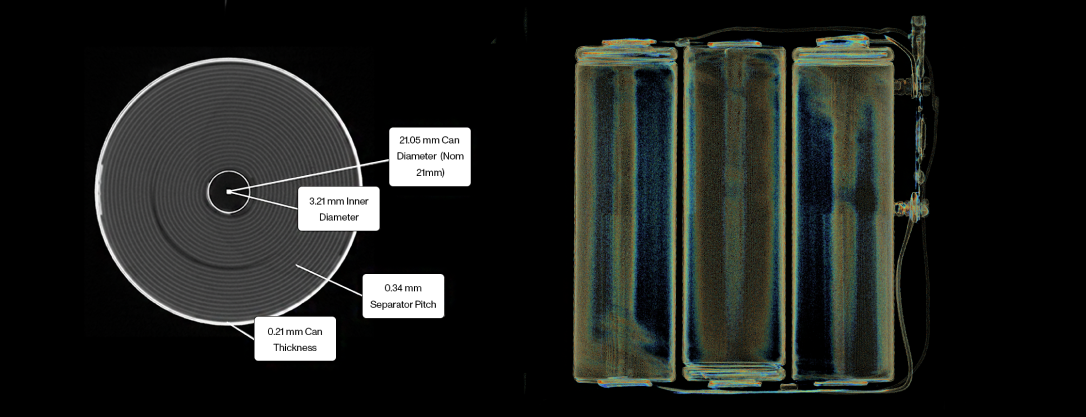
In pursuit of a cost-effective tool more capable of closely evaluating a variety of components within cylindrical battery cells, they identified Lumafield's Neptune industrial CT scanning technology as the best possible fit. Neptune helped the company save over $150K in outsourced scanning expenses in under a year—a 350% return on their investment —while enabling them to reinstate essential annual supplier audits.
For years we tried to limit our CT scanning because of the financial burden associated with outsourcing it, but Lumafield’s Neptune scanner has completely changed that. With all the scanning we’re now able to do, Neptune paid for itself in a matter of months and hugely improved the way we test our batteries.
— President, Product Development
Fine-tuning Scan Parameters
Battery testing usually focuses on the layered, spiral section of the battery known as the “jelly roll”, which engineers must thoroughly evaluate to ensure there are no signs of inconsistency or contamination issues. Other critical components like the anode, cathode, separator, and electrodes must also be examined to ensure consistent production and design quality as part of this process.
Optimizing the scanning of batteries to properly analyze complex internal components can often be challenging, especially when you’ve just brought industrial CT in-house. When some of the company’s early battery scans came back darkened and grainy, Lumafield’s dedicated Solutions Engineering team worked closely with engineers from the customer to fine tune the scan settings.
Lumafield’s team analyzed a variety of their battery scans and recognized that elevated filter sizing and gain settings were causing a noticeable dip in quality. A quick product education session with engineering team leaders helped the customer optimize their scan settings and ensure they produced high-quality scans moving forward.