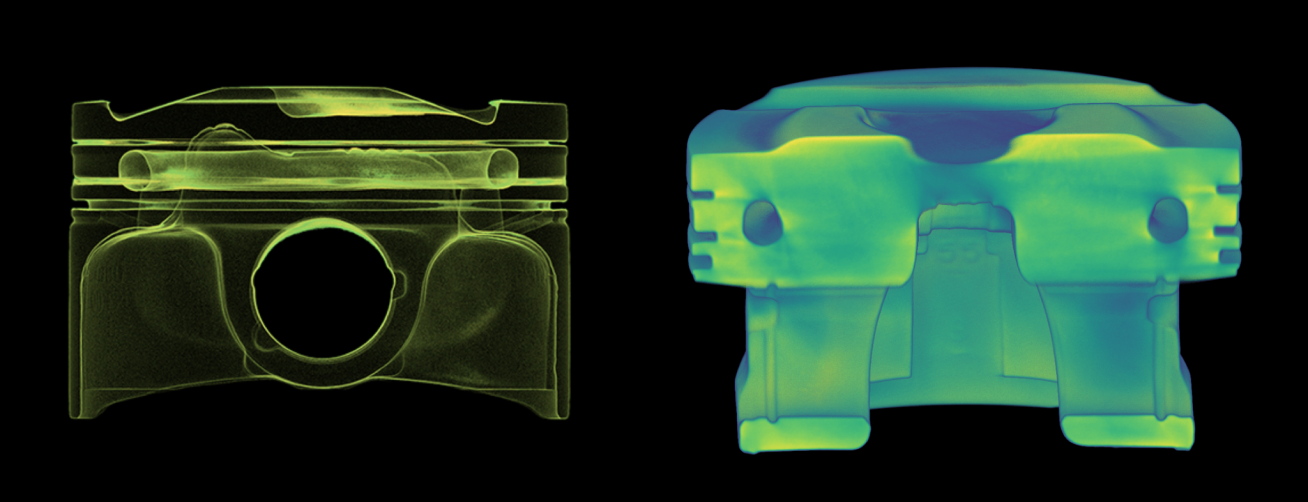
A global automotive safety leader saved over $100K annually on X-ray machine maintenance.
Summary
- A global automotive safety leader eliminated more than $1K in outsourced scan costs per part and saved over $100K annually on X-ray machine repairs with Lumafield’s Neptune CT Scanner.
- High-resolution scans of intricate wiring within steering wheels helped pinpoint a critical short circuit issue, preventing a potentially dangerous and costly product delay.
- Lumafield empowered engineers to collaborate seamlessly with its Voyager software, accelerating problem-solving and protecting consumer safety.
Background
Our customer is one of the world’s largest automotive safety suppliers. They are trusted by top automotive manufacturers across the globe to supply best-in-class safety devices including airbag systems, seatbelts, steering wheels, and a variety of other innovative safety products. Billions of drivers worldwide rely on their airbags and seatbelts to protect them from the full impact of an automotive accident.
With this responsibility in mind, the company maintains an uncompromising commitment to rigorous quality control standards in the production of each component it delivers. Engineers must routinely test the integrity and functionality of a variety of structural components made of plastics, rubbers, foams, fine wire mesh, copper, and other metals. The mechanism which deploys the airbag from the steering wheel is often an area of additional scrutiny, as this includes a highly complex system of electronic and textile components.
Non-destructive testing is essential for safety components such as these. The company was previously reliant on a combination of an in-house X-ray system and outsourced CT scanning to analyze components during both the production and failure analysis processes. With the cost of frequent outsourced scanning difficult to justify and the in-house X-ray machine breaking down every few months, the company identified Lumafield's Neptune industrial CT scanner as a more effective solution.
Safer, Faster, More Reliable
There’s no better tool for integrity analysis and assembly verification. It’s pretty awesome; we now have the clearest possible understanding of the intricate components that make up each product. That sort of insight ultimately helps us save more lives.
— Director, Electrical Engineering
Examining intricate safety device components with Neptune has solved two major problems for the company’s product team. Outsourced CT scanning only allowed them to examine 2D slices rather than 3D models and cost over $1K per part to scan each of their tens of thousands of components. The alternative was an outdated, in-house X-ray machine that often broke down for weeks at a time. Outages and repairs left the company footing the bill for over $100K each year in maintenance alone. These mounting expenses were a frustration, but the lack of detail and reliability in scan data was a major cause for concern.
With Neptune at their disposal, the company transformed this life-saving product testing process at their lab. For 40% less than the expense of repairing their old X-ray machine—and with no more thousand-dollar expense per outsourced scan—Neptune enabled the team to scan and analyze over 30K unique parts at various stages of the development process.
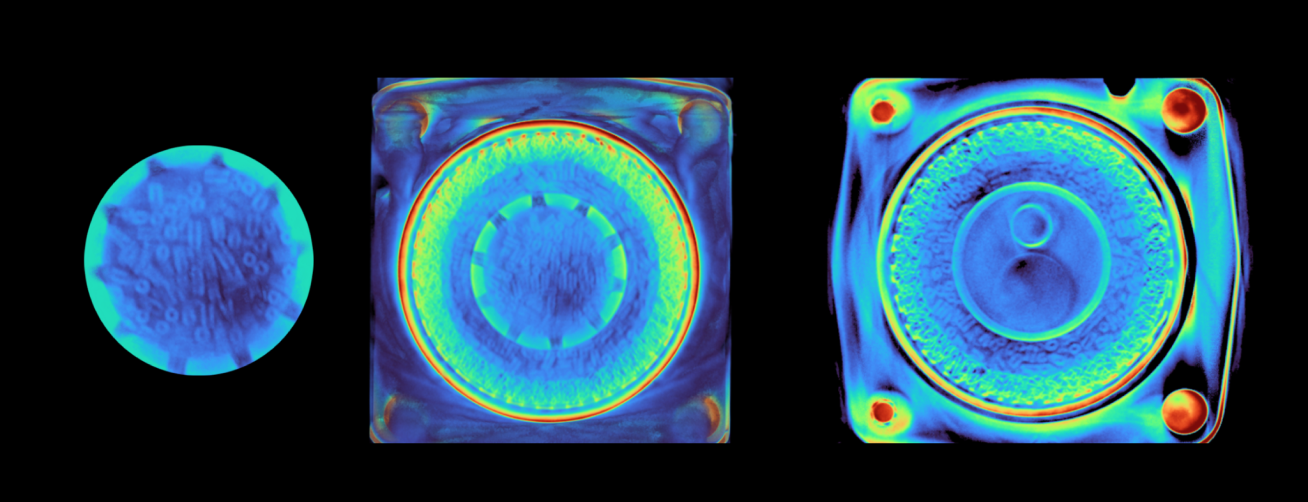
Taking a Closer Look
Steering wheels are among the most complex parts the company currently manufactures, due largely to a combination of plastics, fine wire mesh, textile airbags, and built-in electronics systems. Previous testing methods made quality checks on this fine wire mesh especially difficult, and rendered destructive testing the most reliable way to ensure none of the minuscule wires were malfunctioning or out of position.
Concerns over circuitry issues during the development process halted production of a new steering wheel product last year. With Neptune capable of scanning at a 40 to 50 micron resolution, the company’s electrical engineering team put their new in-house technology to work to evaluate the positioning of the wiring.
Engineers across multiple states working collaboratively in Lumafield’s Voyager software found that contact between two of the fine copper wires had caused a short in the system. Product designs were quickly altered and retested, and the company ultimately delivered a safer and more reliable product as a result.
There’s no room for error in this business. We can’t have defective products, and Lumafield is an incredible partner in ensuring that we catch anything that could potentially malfunction long before these parts leave the factory.
— Director, Electrical Engineering