An advanced manufacturing operation uses Lumafield’s CT platform to validate the invisible—from complex liquid cooling systems to the machines that build them.
Thermal management is critical for high-performance computing and modern electronics. AI accelerators, semiconductor equipment, and laser systems are all shrinking in size while increasing in power. With more watts concentrated in tighter spaces, engineers are hitting the thermal wall faster and more frequently.
Alloy Enterprises is helping them break through it.
The Massachusetts-based company is changing how high-performance metal cooling components are designed and manufactured. Their latest innovation, a liquid cold plate engineered for the NVIDIA H100 PCIe card, shows what’s possible when thermal engineering, design automation, and new manufacturing processes are combined into one tight loop.
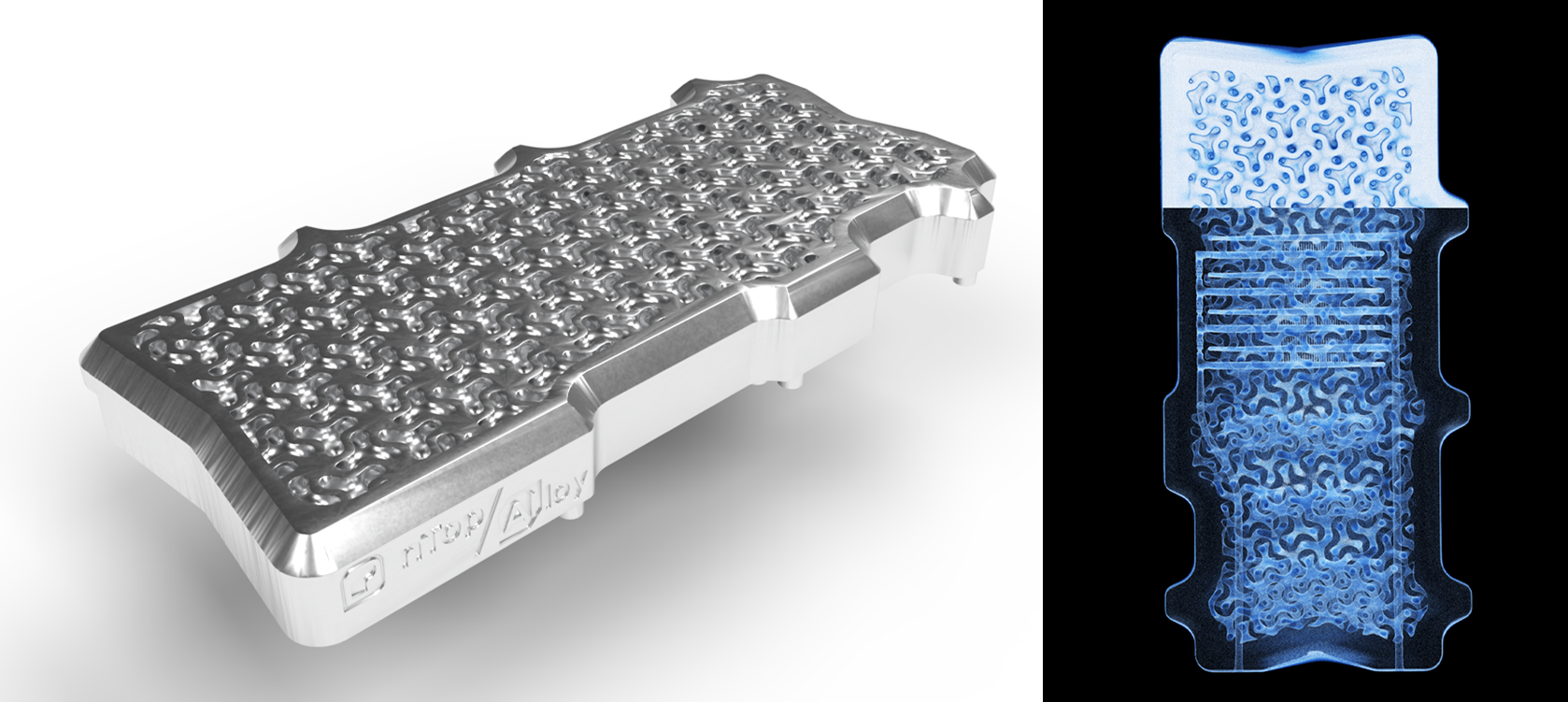
“We make complex metal components with internal micro geometries,” says Ali Forsyth, PhD, Alloy CEO. “Our customers are pushing the limits, and we’re helping them pull the heat out.”
Rethinking the Process from the Ground Up
Before founding Alloy, Ali Forsyth’s team had accumulated decades of expertise in additive manufacturing. They worked with metal 3D printing, coming to understand both its strengths as well as its limitations. Powder-bed fusion processes offered flexibility but failed to scale economically or deliver consistent quality for the types of fluid handling parts that require both structural integrity and internal precision.
Instead of iterating on flawed processes, they decided to build a new one. That became Stack Forging, Alloy’s patented manufacturing process. It uses laser-cut sheets of metal rather than powders, bonding them under controlled heat and pressure into solid components that contain an inner world of complex internal geometries. The resulting parts are monolithic, free of porosity, and structurally robust.
We leverage the Neptune scanner all the time. Seeing inside allows us to iterate and optimize so much faster.
—Ali Forsyth, CEO, Alloy Enterprises
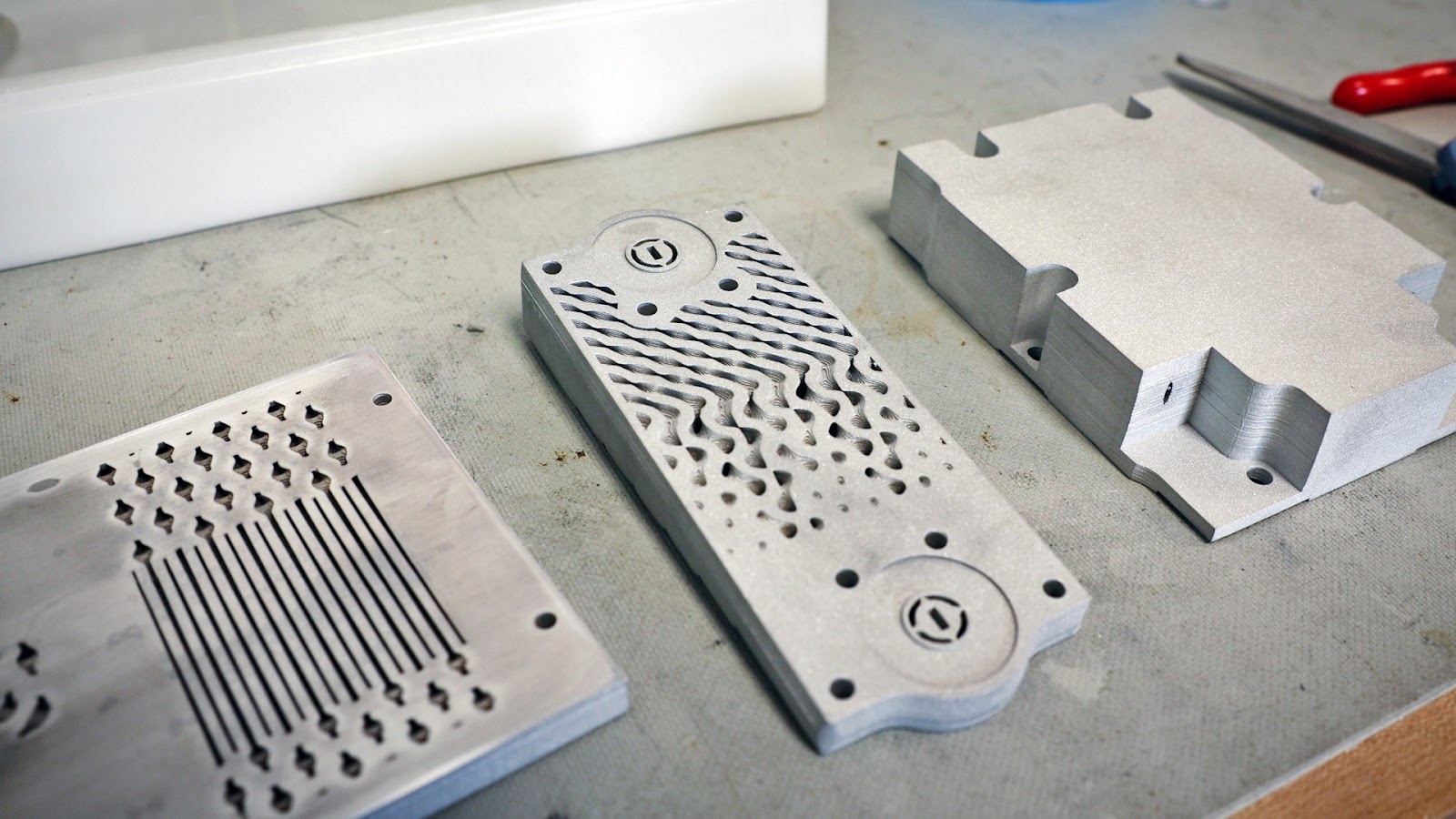
Alloy’s process opens the door to manufacturing features that would be cost-prohibitive or technically out of reach using machining or traditional additive methods. And because it scales easily, it supports the needs of customers designing for production instead of just prototypes.
Anatomy of a Next-Generation Cold Plate
Nowhere is that capability more evident than in Alloy’s cold plate for the NVIDIA H100 PCIe card. This component is tasked with dissipating massive thermal loads from one of the most powerful AI accelerators available. It isn’t just a heat sink. It’s a microfluidic system, fine-tuned to deliver performance at the edge of what’s physically possible.
The design was developed using nTop’s field-based modeling tools. That parametric environment allowed Alloy’s engineers to optimize the geometry based on simulated heat flux, fluid flow, and structural constraints. Rather than relying on traditional CAD, they generated a performance-driven structure.
The result is impressive:
- 180-micron microcapillaries direct coolant flow with high precision to regions of peak thermal output.
- Massively parallel inlet and outlet channels minimize flow length and keep pressure drop extremely low, ensuring even performance across the cold plate.
- A gyroidal TPMS (triply periodic minimal surface) provides internal support and maximizes surface area while maintaining a total part weight under 550 grams.
In these systems, heat removal means the difference between optimal performance and total failure. This cold plate not only addresses the challenge, it pushes well beyond the limits of conventional thermal hardware.
Inspection That Moves at Design Speed
The ability to manufacture parts like these is only part of the equation. Equally important is the ability to inspect them. Traditional metrology tools fall short when the features you care about are sealed inside a solid metal structure. That’s why Alloy turned to industrial X-ray CT, adopting Lumafield’s Neptune scanner and Voyager software platform.
Not having to use destructive methods to visualize parts accelerated our Production Engineers' development of solutions from months to weeks, reducing cost by cutting the number of trials needed.
—Dave Tedder, Director of Part Production
With CT scanning, Alloy’s engineers can inspect internal features down to the micron level, validate dimensional accuracy, and confirm that the geometry matches the intended design. The non-destructive process allows the part to remain intact, saving on scrap. And instead of inspection creating a bottleneck, industrial CT supercharges development timelines. Scans are fast, accurate, and easy to share.
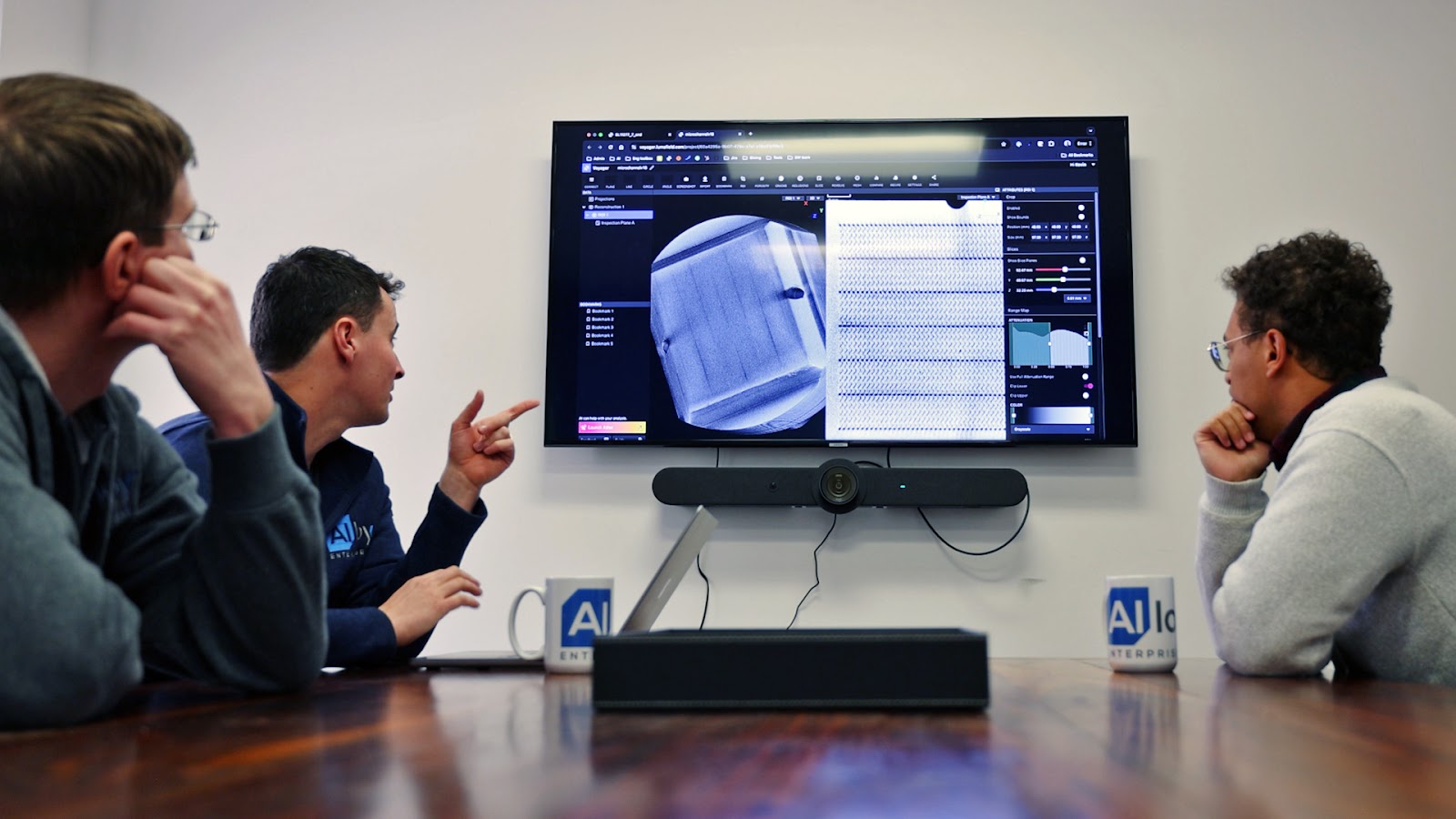
Voyager, Lumafield’s browser-based analysis tool, puts powerful quality workflows at Alloy’s fingertips. Engineers can review scan data, run measurements, annotate areas of interest, and share findings with both internal stakeholders and customers. That transparency changes the dynamic of customer collaboration.
Showing customers the inside of their own components gives us an opportunity to demonstrate the capabilities of our technology.
—Ali Forsyth, CEO, Alloy Enterprises
This visibility not only helps Alloy validate their own work. It helps customers trust their process and understand what’s happening inside the parts they’re deploying.
First-Pass Success, Every Time
The impact on development speed has been significant. Alloy uses CT scanning throughout the product development cycle, from initial prototypes to final validation. The resulting continuity ensures they catch problems early and deliver production-ready parts faster.
We’re able to ensure quality right out of the gate. First try.
—Ali Forsyth, CEO, Alloy Enterprises
In high-stakes industries like photonics and advanced computing, that level of reliability matters. Delays are expensive. Unexpected failures can break a product launch or compromise a mission. By integrating inspection directly into their design workflow, Alloy helps their customers move faster with fewer surprises.
The collaboration isn’t limited to engineering teams. Because Voyager runs in any web browser, project managers, procurement leads, and external partners can all access the data from anywhere in the world. That makes communication smoother and decision making faster.
Quality Starts with Equipment
Inside Alloy, Lumafield’s CT platform has become just as important for maintaining Alloy’s own production systems as it is for validating customer parts. Bill Johnson, a Senior Systems Engineer on the machines team, shared how the scanner revealed a failure mode that had stumped the group for weeks.
“We had a set of heaters that were failing, and we couldn’t really get to the bottom of why,” Johnson said. These heaters were part of the equipment Alloy uses in its proprietary diffusion bonding process. The failures were causing downtime and product loss, but the root cause remained elusive—until someone suggested putting the components into the Neptune scanner.
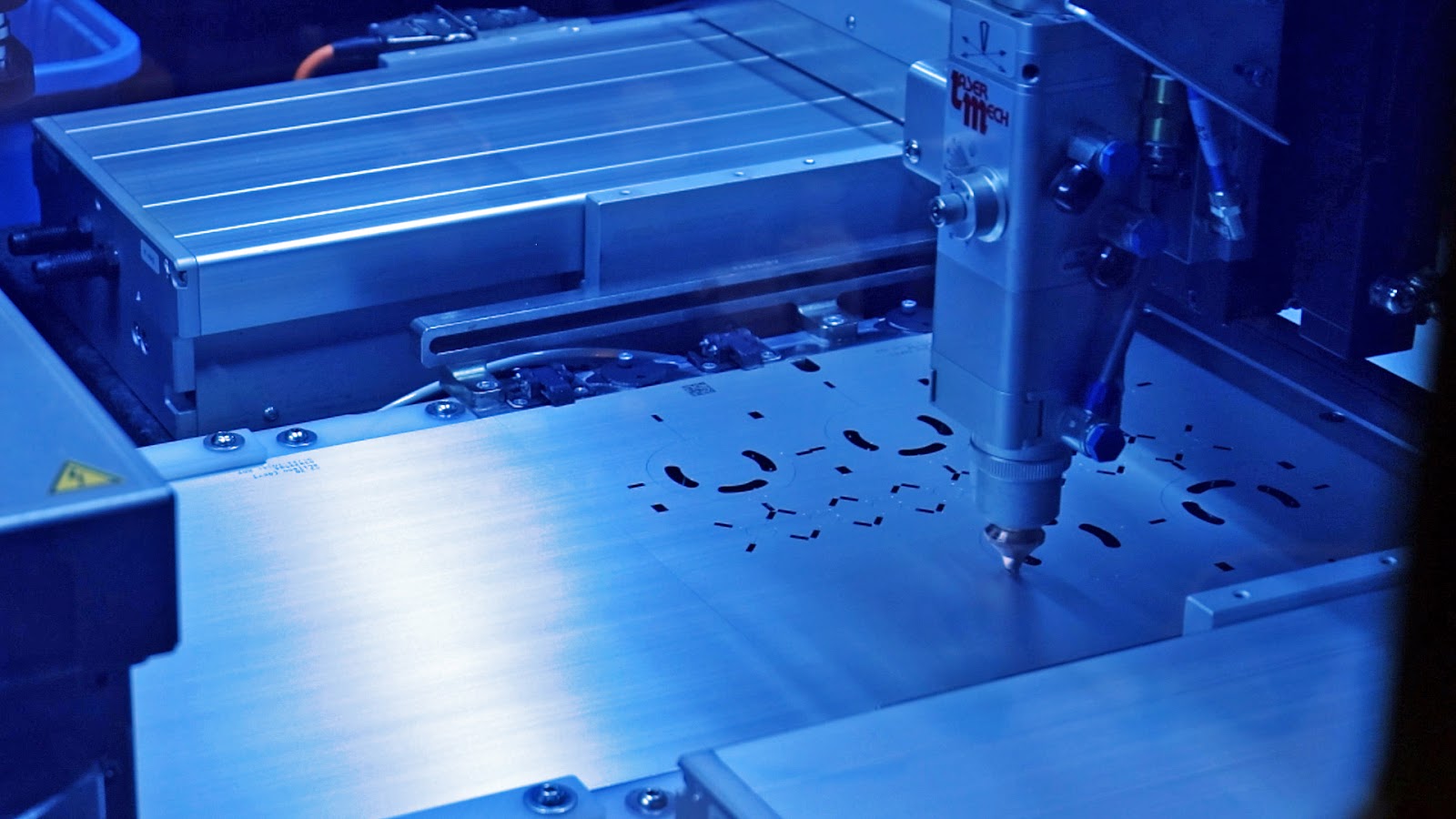
What they found was clear and actionable. Some of the heating elements hadn’t been properly soldered during manufacturing. This led to fatigue, breakage, and intermittent electrical contact. It wasn’t something that could be diagnosed with a multimeter or even destructive testing.
CT scanning provided the evidence Alloy needed not just to fix the issue, but to go back to the vendor with concrete data and push for corrective action. “It gave us the ability to actually look now at all of our equipment, all of these heaters that are going into our equipment, and see that we have a yield problem,” Johnson explained.
I’ll be honest, I don’t think we would have seen this if we didn’t have a tool like the Lumafield scanner.
—Bill Johnson, Senior Systems Engineer, Alloy Enterprises
This isn’t a one-off case. As Alloy scales, the same CT capabilities used to validate cold plates are now helping them harden their own production line. More than a product development tool, the scanner is becoming part of the factory’s diagnostic system.
A New Standard for Fabrication
Alloy is building more than a novel process; they’re pioneering a new workflow. Engineers move from field-driven design, to scalable fabrication, to digital inspection—all in one continuous cycle. There’s no handoff between silos. The same team can model a part, build it, inspect it, and deliver it with confidence.
This model is proving to be both faster and more resilient. It allows Alloy to respond quickly to new requirements, test ideas in days instead of weeks, and help their customers adapt to rapidly shifting product demands.
Lumafield plays a central role in that ecosystem. Without the ability to see inside every part, the promise of internal complexity would be harder to fulfill. CT scanning closes the loop.
With every scan, every iteration, and every successful delivery, Alloy is showing what happens when inspection transforms from an afterthought to a core capability that supports innovation at every level.
Engineering for the Future
In the past, internal complexity was something to avoid. It created cost, risk, and uncertainty. With Stack Forging and industrial CT, it’s becoming a strength.
Today, Alloy is shipping high-performance cold plates that contain hundreds of precision fluid channels and internal surfaces invisible to traditional inspection. And they’re doing it at scale.
There's not a single part of our business that Neptune and Voyager haven’t touched: from sales, to marketing content, to R&D, to accelerating the design of parts and delivery to our customers, to debugging problems on our machines. We've been able to take advantage of CT scanning in ways we hadn’t even imagined.
—Kevin Simon, Director of Software, Alloy Enterprises
This is what engineering becomes when design, manufacturing, and inspection operate as one. Alloy and Lumafield are engineering for that future.