"I've cut open a million pairs of shoes. You can see your product in a different light when you have something intact, and you can look at it digitally."
Summary
- Developing shoes is a labor-intensive process; Saucony's designers must ship physical samples around the world and physically destroy multiple prototypes with destructive testing. Geography and material limitations restrict access to samples, even as Saucony’s rigorous testing process demands data and accessibility.
- Industrial CT scanning gives engineers a way to look inside an intact shoe and share scans with coworkers and suppliers, saving time and cost and reducing environmental impact. Additionally, CT scans build a "digital-closet" that engages sales reps and customers.
- Lumafield’s CT scanning technology has driven collaboration across Saucony. Before the company adopted Lumafield industrial CT, only a few engineers could see how shoes were constructed. Now product line managers, marketers, and others can engage with the scans, increasing familiarity with their products, streamlining communication, and ultimately improving how they work together.
Background
For over a century, Saucony has made athletic shoes that deliver excellent fit, comfort, and running performance. It's easy to think that running shoes are simple products, but creating a pair of high-performance running shoes today calls for advanced materials and engineering expertise that wouldn’t seem out of place in a NASA lab. As shoes become more advanced, shoemakers need better data to design and manufacture products that push the limits of performance.
“While the world of shoe makers and shoe sellers seems decidedly analogue, the use of sophisticated scanning and visualization is a powerful tool in the digitalization of our entire industry at every step along the value chain,” says Barry McGeough, Global VP of Innovation at Wolverine Worldwide, Saucony’s parent company.
Saucony approaches the design and manufacture of each shoe as a technical challenge. The company has a deep commitment to product engineering. Saucony's innovation lab hosts a full biomechanics laboratory, where designers fabricate a wide variety of R&D shoes and run countless rounds of testing for each design. Underlying all their efforts is the goal of producing the highest-quality shoes. “It's really important to us to make sure that we are the best at what we do,” says Luca Ciccone, Director of Product Engineering at Saucony. “We take a lot of care in making sure we know what’s inside of our shoes so that the athletes wearing them can perform their best.“
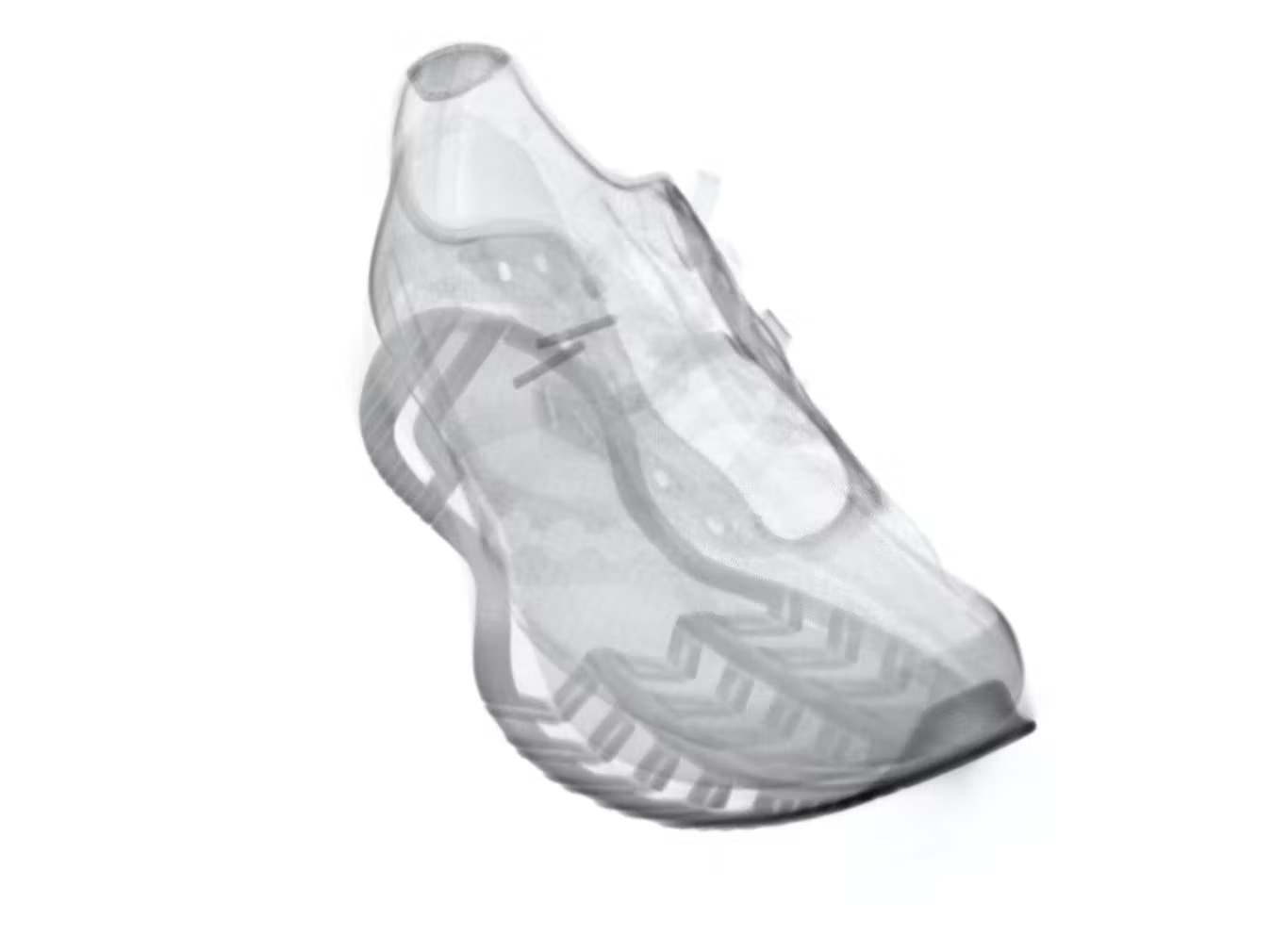
Saucony + Lumafield
One of the biggest barriers Saucony's designers and engineers encounter is the difficulty of looking inside their shoes at critical internal features—until recently, a highly manual process that defies collaboration.
For every new shoe, Saucony orders samples from one of its partner factories, tests them on live runners to see how they perform as the foot hits the road, and then slices them open before and after testing for detailed lab examination. This process is repeated multiple times until engineers are satisfied they’ve nailed the design.
Industrial CT scanning helps Saucony streamline this process, lowering costs, saving time, and reducing waste. Rather than needing to destroy prototypes, engineers can use CT scans to quickly peer inside any shoe to study defects, molding, and density. "I've cut open a million pairs of shoes. You can see your product in a different light when you have something intact, and you can look at it digitally,” says Ciccone of Lumafield’s CT scanner. “[It] adds so much value to our process.”
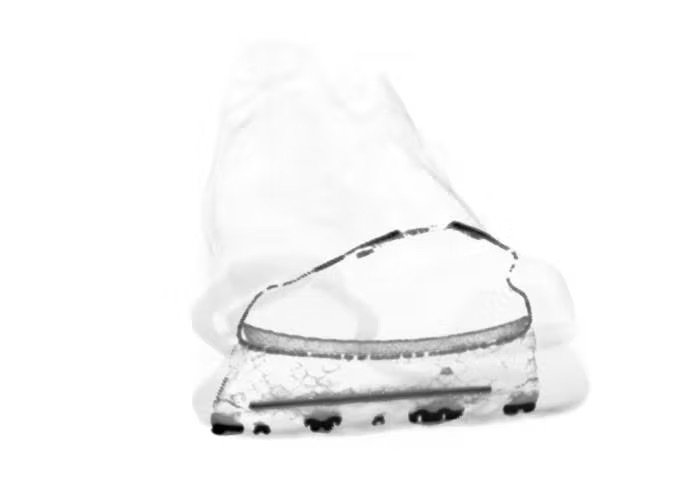
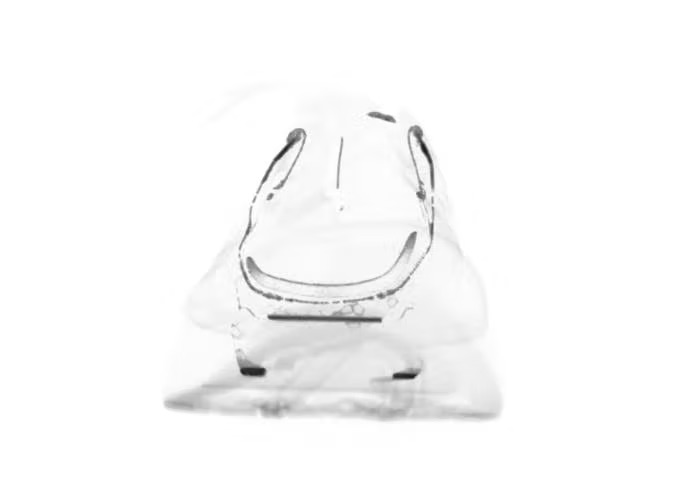
By translating physical shoes into 3D scans, Lumafield is helping Saucony build its digital manufacturing future. As Ciccone explains, “The fact that we can scan a shoe with the sole unit attached …. you can really get an idea of how all these components are actually looking [together]. We weren’t able to do that before.” Keeping these scans in a growing “digital closet” allows Saucony to compare previous iterations of a model against each other, streamlining both design and manufacturing processes.
And engineers aren't the only ones to benefit from CT scanning; the ability to scan shoes has strengthened collaboration across Saucony. Scanning gives stakeholders across teams the ability to engage more deeply with their products, allowing for closer collaboration and tighter communication. “It's a team effort here whenever we develop new products,” says Ciccone, emphasizing how valuable it is for brand managers and marketers to be able to access the same information as the engineers.
Asked to enumerate other ways they’d like to use CT scans in the future, McGeough and Ciccone were full of ideas. “It’s the ultimate content,” says McGeough of CT scans, explaining that it’s always beneficial “if athletes and enthusiasts alike can better understand the anatomy of their footwear, not just how it will perform for them, but why.” Ciccone adds, “It's a tool where it's tough not to want to use it. There are always places where we can.”