CT Touchdown
As the Big Game approaches, it’s easy to focus on the teams and forget about the real powerhouse: the football itself. Industrial CT gives us a window into what lies beneath its leather exterior. Let’s take a look at the ball’s easily overlooked engineering and labor-intensive manufacturing process.
To get started, give the football a spin in our Voyager window below.
Panels
The pebbled leather panels of football are made of cowhide, which wears well over time and provides a grip that can withstand all weather conditions. A football’s manufacturing process is still largely manual. A worker cuts out the four panels with a die, sews cotton and vinyl linings onto the back of each one, and then stitches them all together before a roller flattens the seams. CT allows us to assess the consistency in the panel's thickness, the precision of the stitches, and how well the panels conform to the bladder, all of which contribute to the ball's aerodynamic properties and in-hand feel.
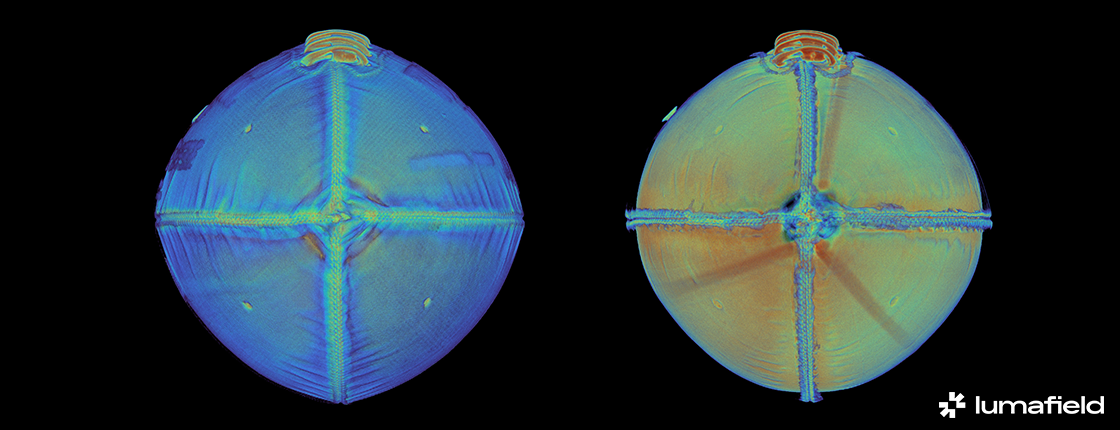
Bladder
Enclosed within the four panels is a polyurethane bladder, a critical component that retains air and ensures the ball holds its shape and proper inflation. With Voyager’s dimensioning tools, we can measure the thickness of the layers and apply a color map that corresponds to the density of each material. The thickness of the polyurethane bladder (red, most dense) measures 0.872 mm, the cotton/vinyl layer (blue, least dense) is 1.389 mm, and the leather (yellow, density between the bladder and lining) is 1.456 mm.
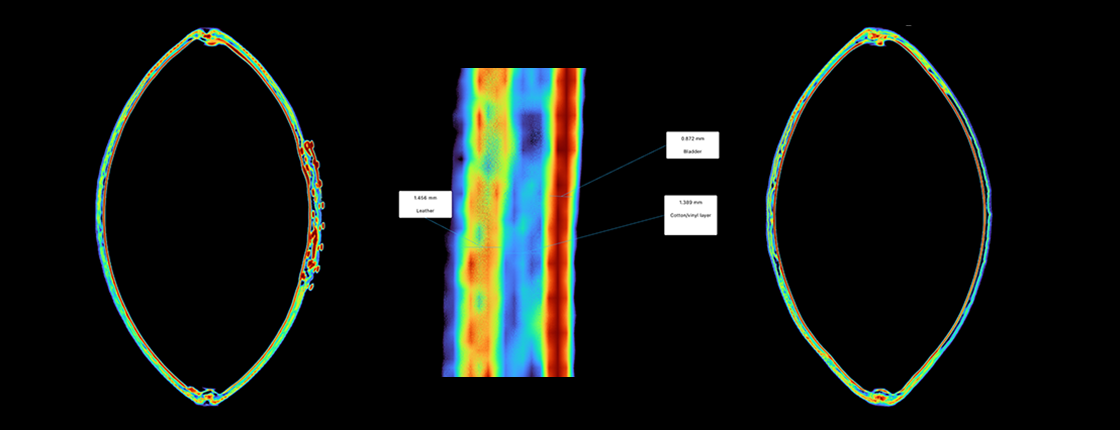
Laces and Valve
The laces on a football aren’t just there for show; they provide an essential grip for quarterbacks to throw spiral passes with accuracy. A worker inflates the ball to make it rigid, then steadies it with planks before using an awl to thread the single four-foot-long vinyl lace through the holes twice over.
While small and often unnoticed, the valve can make or break the football. A proper seal is needed for air retention, especially during a game as critical as the Super Bowl. A retaining flange embeds in a dense housing adhered to the bladder’s inner wall. The NFL requires that a football be inflated to between 12.5 and 13.5 psi. This is crucial, because a softer ball is easier to catch. Remember Deflategate?
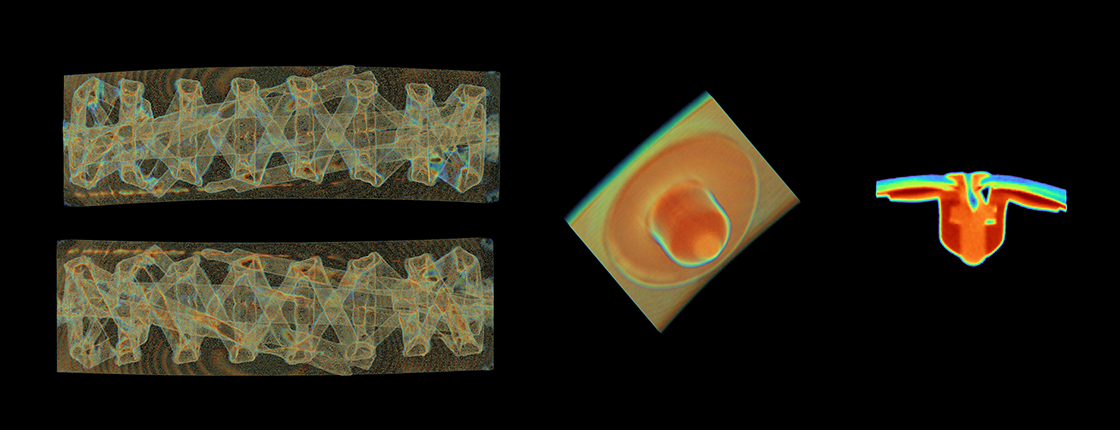
Conclusion
CT helps us appreciate the unseen qualities that ensure footballs meet the highest standards of quality and performance. At this year’s Big Game, don’t lose sight of the precision design and craftsmanship at the heart of the sport.
Discover how Trek Bicycle and other athletic equipment manufacturers are using Lumafield's industrial CT platform to accelerate their product development.