Manufacturing Process: Blow Molding
Blow molding is a widely used manufacturing process for producing hollow plastic products, including bottles, containers, and industrial components. The process is valued for its ability to create lightweight, durable, and cost-effective parts with minimal material waste.
By inflating heated plastic inside a mold, manufacturers can achieve complex shapes and precise wall thicknesses quickly and at large production volumes. Different blow molding techniques offer varying levels of precision, strength, and flexibility, making each suited to different applications.
The three primary types of blow molding—Extrusion Blow Molding (EBM), Injection Blow Molding (IBM), and Injection Stretch Blow Molding (ISBM)—each offer unique advantages in terms of efficiency, precision, and material properties. While all three methods produce hollow plastic parts, they differ in how the plastic is formed, shaped, and finished, making each process better suited for specific applications ranging from industrial containers to medical vials and beverage bottles.
What is Extrusion Blow Molding (EBM)?
Extrusion Blow Molding (EBM) is the most versatile blow molding method, commonly used for detergent bottles, automotive ducts, industrial drums, and fuel tanks. It’s ideal for larger or more irregularly shaped hollow parts that don’t require extreme precision.
EBM products often have visible seam lines along the sides, where the mold halves met during processing. Many also have a pinch-off mark at the bottom, where excess plastic was trimmed after molding. If the bottle has an open, threaded neck but lacks a separate pre-molded finish, it was likely made using EBM.
The EBM Process
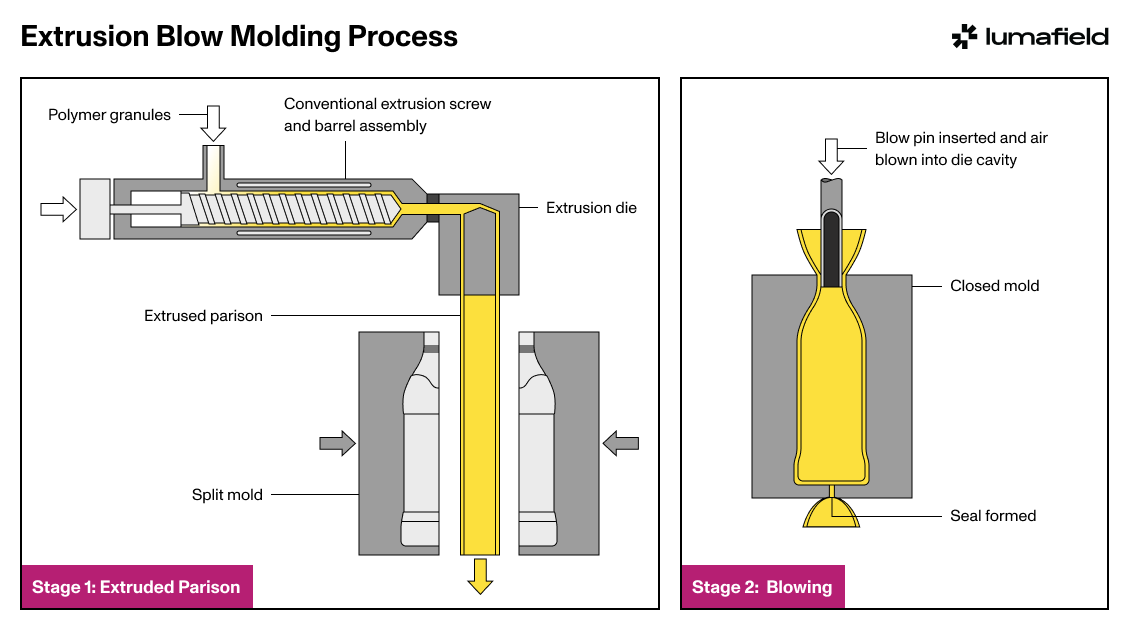
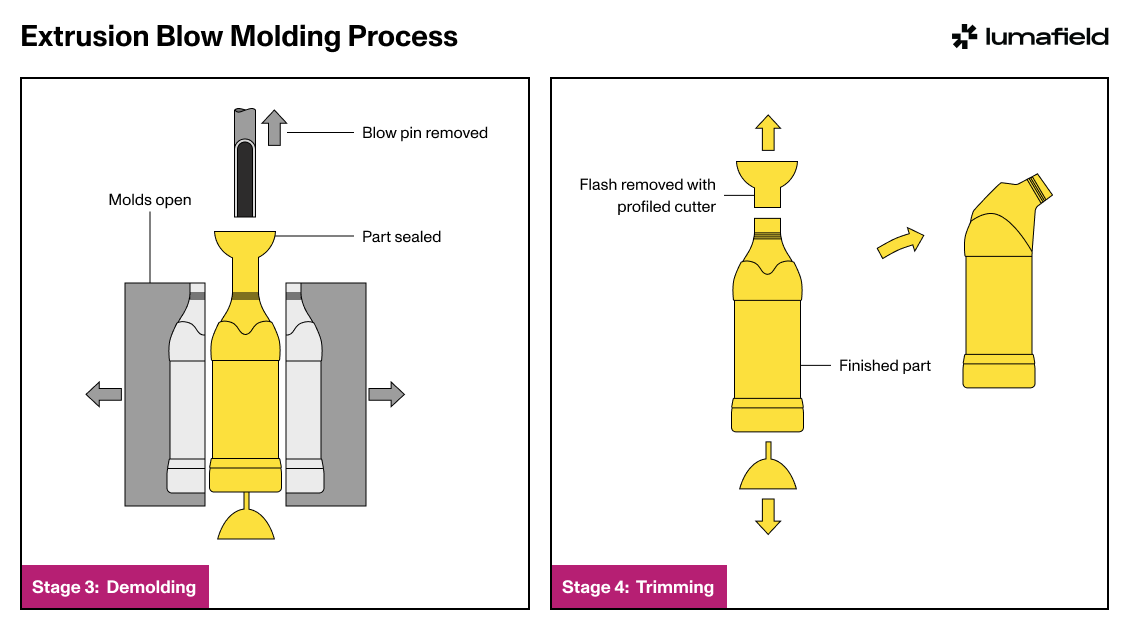
- Extruding the Parison: Plastic granules are melted and extruded through a die, forming a continuous, hollow plastic tube known as a parison. The material remains molten and flexible.
- Blowing and Forming: A mold clamps around the parison, and a blow pin is inserted at the top. Compressed air expands the parison, pressing it against the mold walls. Simultaneously, the bottom is sealed by pinching the material together.
- Demolding: Once the plastic cools and solidifies, the mold opens, and the newly formed part is released. The blow pin is removed, leaving a fully enclosed hollow structure.
- Trimming: Excess plastic, known as flash, is removed from the top and bottom using a profiled cutter, ensuring a clean final shape. The finished part is now ready for use or additional processing.
EBM is highly efficient for high-volume production of durable, multi-layer containers with variable wall thickness.
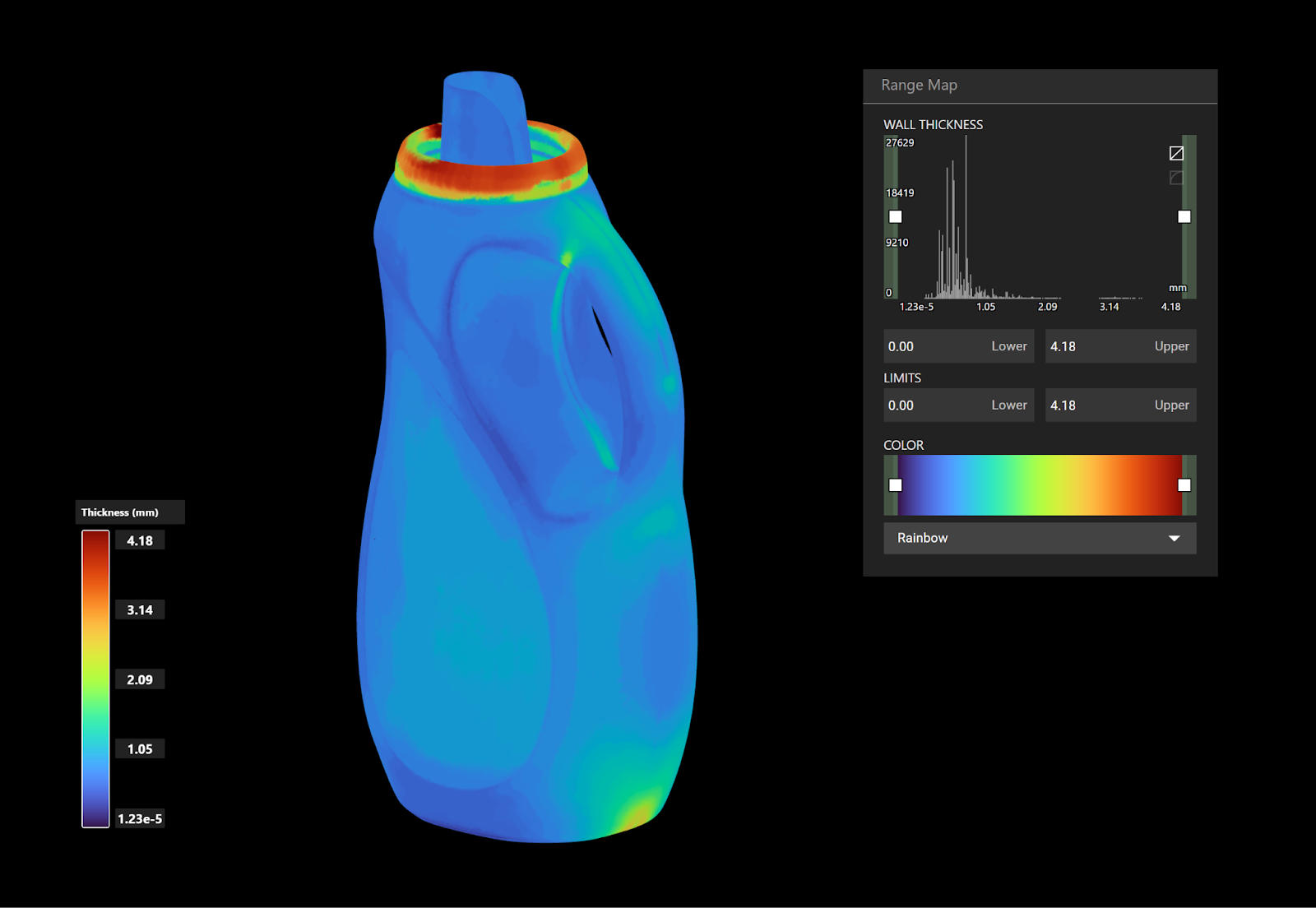
What is Injection Stretch Blow Molding (ISBM)?
Injection Stretch Blow Molding (ISBM) is a high-performance process designed primarily for lightweight, impact-resistant PET bottles, such as water bottles, soda bottles, and juice containers. The key difference in ISBM is that the preform is stretched before blowing, enhancing material strength and clarity.
ISBM bottles are thin-walled, lightweight, and can be either clear or opaque with a well-defined neck and threads. Side seams are generally less visible, and bottles typically show stretch marks or flow lines in the material, indicating the preform was elongated before blowing.
The ISBM Process
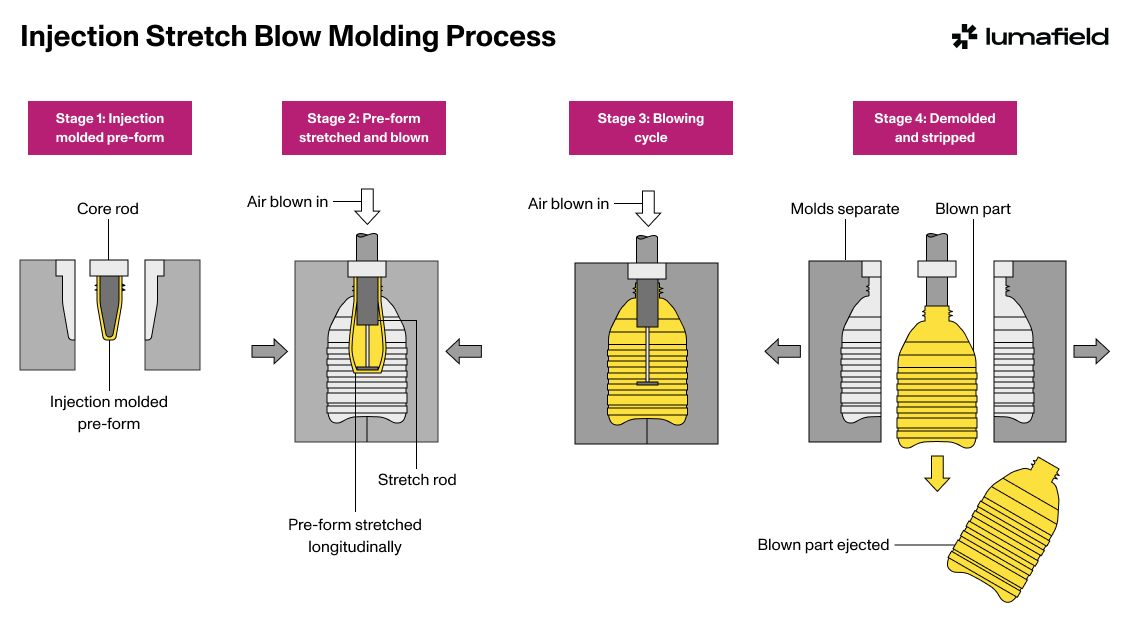
- Injection Molding the Preform: A PET preform is injection-molded with a finished neck and threads.
- Stretching and Pre-Blowing: The preform is heated and placed into a stretch-blow mold. A stretch rod extends the preform lengthwise, improving material orientation and increasing tensile strength.
- Final Blowing: Compressed air inflates the preform outward against the mold, finalizing the shape while maintaining the stretched structure.
- Demolding and Ejection: The mold separates, and the bottle is ejected, ready for filling.
ISBM produces high-strength, lightweight bottles with superior impact resistance and barrier properties, making it the go-to process for carbonated and non-carbonated beverage bottles.
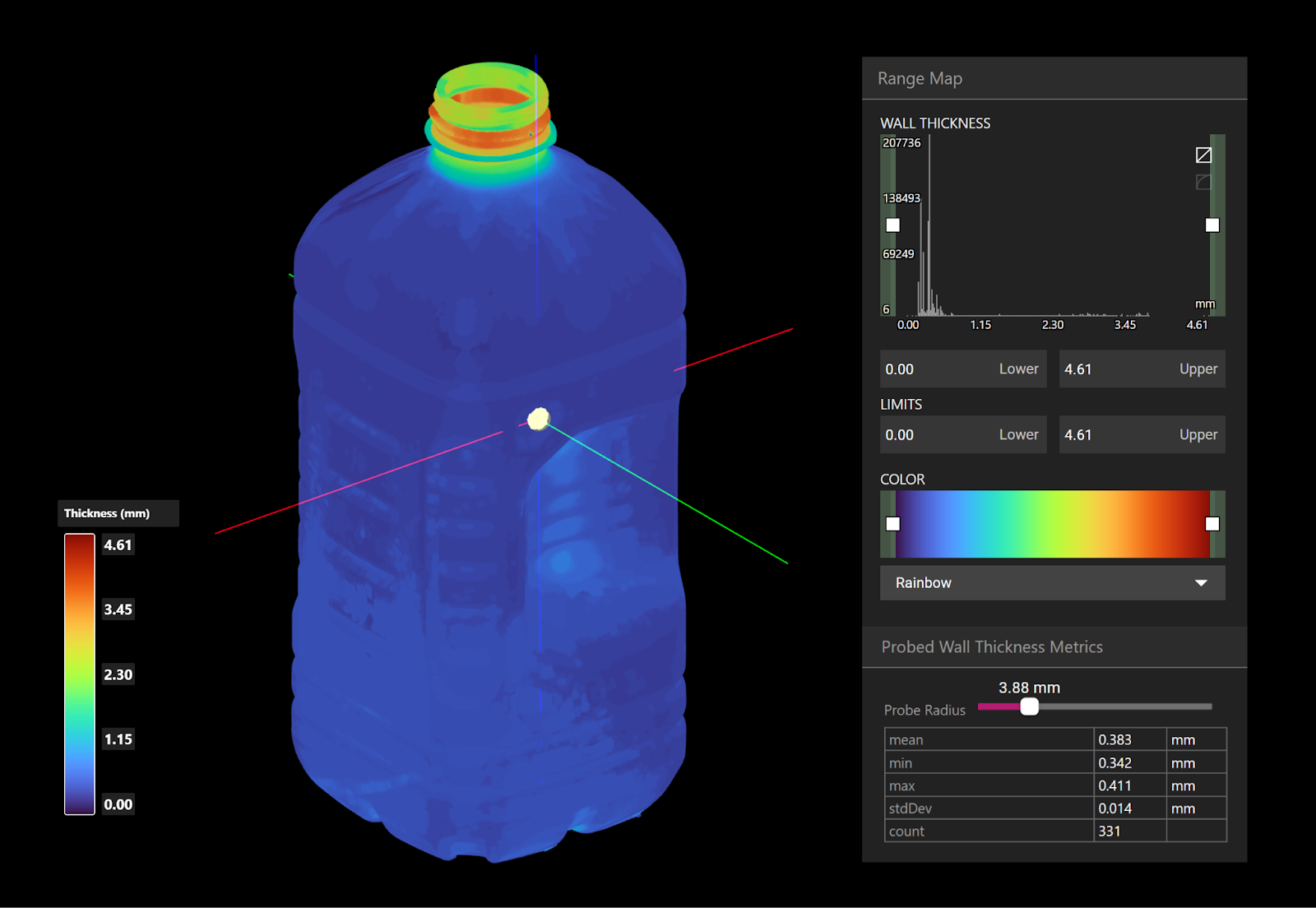
What is Injection Blow Molding (IBM)?
Injection Blow Molding (IBM) is used for producing small, precise, high-quality bottles, such as pharmaceutical vials, cosmetic containers, and lab bottles. It differs from EBM in that it starts with an injection-molded preform, leading to better dimensional accuracy and a polished surface.
IBM bottles have a smooth, seamless appearance, often with a precise, pre-formed neck and threads. Unlike EBM products, they lack visible side seams because the material is formed inside a closed mold rather than being pinched together.
The IBM Process
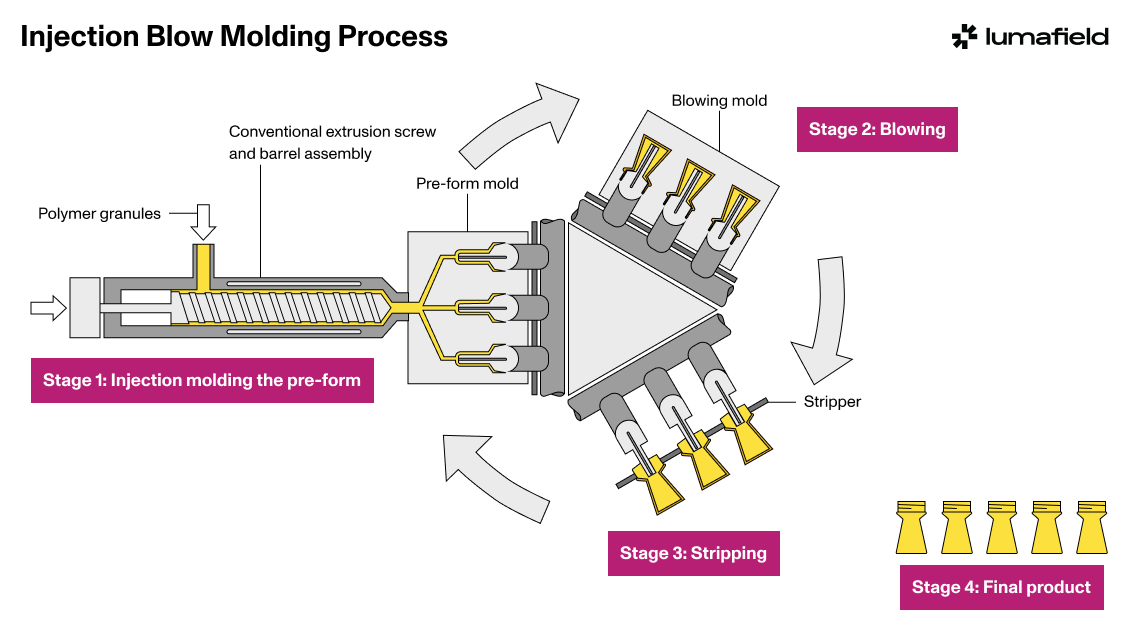
- Injection Molding the Preform: Plastic is melted and injected into a mold to create a preform, a small tube with a finished neck and threads.
- Blowing and Expansion: The preform is transferred to a blow mold, where compressed air expands it to the final shape. Because the preform is already solidified, the material distribution is highly controlled.
- Stripping and Ejection: Once the part cools, it is removed from the mold. No trimming is required, as IBM does not produce flash or excess plastic.
- Final Product: The finished bottle is immediately ready for filling or secondary processing, requiring minimal post-molding adjustments.
IBM produces consistent, high-precision bottles with excellent clarity, making it ideal for medical and cosmetic applications.
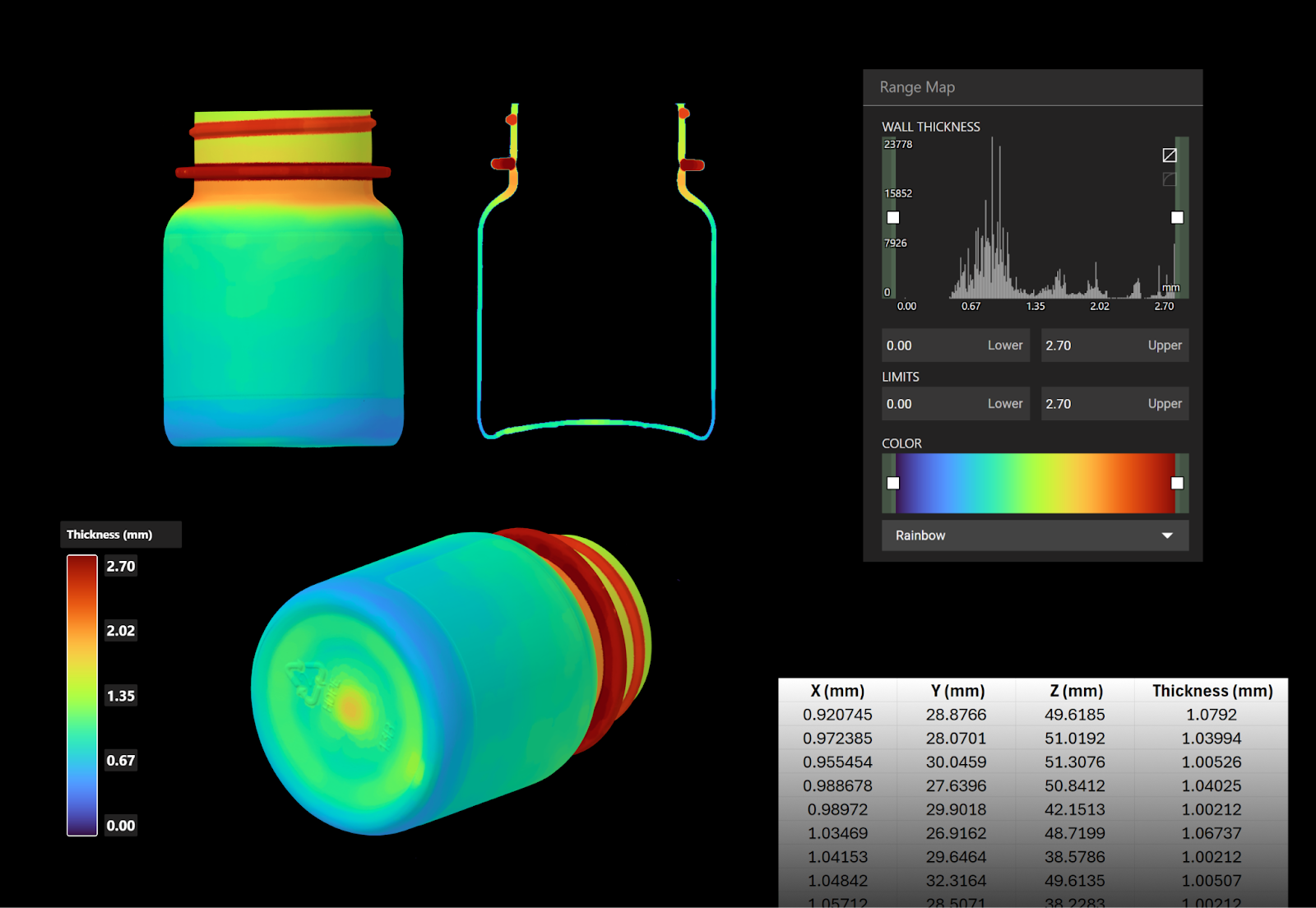
Design Considerations for Blow Molding
- Material Selection: HDPE and PP are common for EBM, while PET dominates ISBM for clarity and strength.
- Wall Thickness Control: IBM and ISBM ensure uniform thickness, whereas EBM may require trimming.
- Neck and Thread Precision: IBM and ISBM create high-accuracy necks, crucial for sealing with caps. This also allows companies to source bottles and caps from different sources, and be certain the threads will match up
- Production Speed and Volume: All three processes enable high-speed, cost-effective production, but EBM excels in large-scale manufacturing of industrial and household containers, while IBM and ISBM provide tighter dimensional control, making them ideal for applications where precision and safety—such as medical vials and beverage bottles—are critical.
How Industrial CT Can Improve Blow Molding
Industrial CT scanning is an essential tool for non-destructive quality inspection in blow molding.
- Wall Thickness Analysis: CT scanning provides highly accurate measurements of wall thickness across all blow-molded products, ensuring uniformity, structural integrity, and optimized material usage. This data helps identify weak points that could lead to buckling or failure under load, supports engineering design improvements, and enables material reduction strategies for cost savings and sustainability.
- Void and Defect Detection: Identifies air pockets, cracks, leaks, or inclusions in containers.
- Neck and Thread Accuracy: Ensures proper cap fit and sealing integrity for bottles.
- Preform and Stretch Ratio Evaluation: In ISBM, CT scanning assesses preform symmetry and material distribution, ensuring consistent material orientation for improved durability, stretch ratios, and weight reduction. This helps manufacturers refine heating, stretching, and blowing parameters to enhance bottle performance while minimizing material waste.
By detecting defects early and ensuring precision, CT scanning improves quality, reduces scrap, and enhances manufacturing efficiency.
Better Bottles, Faster
Blow molding has transformed how industries produce lightweight, durable plastic parts at scale. Whether it’s the high-speed efficiency of Extrusion Blow Molding, the precision of Injection Blow Molding, or the strength and versatility of Injection Stretch Blow Molding, each process plays a vital role in shaping the products we use every day—from detergent bottles to medical vials to beverage containers.
But even the most refined processes have room for improvement. Industrial CT scanning gives manufacturers a deeper level of insight, uncovering hidden defects, optimizing material distribution, and ensuring every part meets exacting standards. By embracing advanced inspection technologies, manufacturers can push the limits of performance, sustainability, and quality in blow-molded products, staying ahead in an ever-evolving market.