Introduction to Industrial CT
Industrial Computed Tomography (CT) has long been a critical tool in solving engineering challenges across industries. However, the technology has traditionally been out of reach for many companies due to high costs and complexity. At Lumafield, we’re changing that with our cutting-edge CT solutions, making this powerful technology accessible to more manufacturers than ever before.
What is industrial CT?
Industrial CT operates similarly to medical CT, but it’s tailored for the unique demands of product design and manufacturing. Our Neptune CT scanner consists of a turntable that holds the scan subject, an X-ray source, and an X-ray detector. During a scan, X-rays are projected through the subject and captured by the detector, producing two-dimensional X-ray images known as radiographs. These radiographs, which vary in density and thickness, form the foundation of our CT data.
To transform these 2D images into a comprehensive 3D model, the scanner captures multiple radiographs as the object rotates. This process, managed by our Voyager cloud software, compiles anywhere from several dozen to over a thousand radiographs into a detailed 3D representation. The resulting model not only shows the object’s spatial configuration but also highlights density variations, providing invaluable insights into the internal and external features of the scanned item.
Voyager offers multiple ways to visualize and analyze CT data. Users can view the original radiographs, explore the 3D model, and employ tools like histograms to isolate materials of different densities. This functionality is especially useful for inspecting complex assemblies and identifying potential issues. Moreover, Voyager includes automated analysis features that detect and measure defects such as pores, voids, and cracks, streamlining the quality control process.
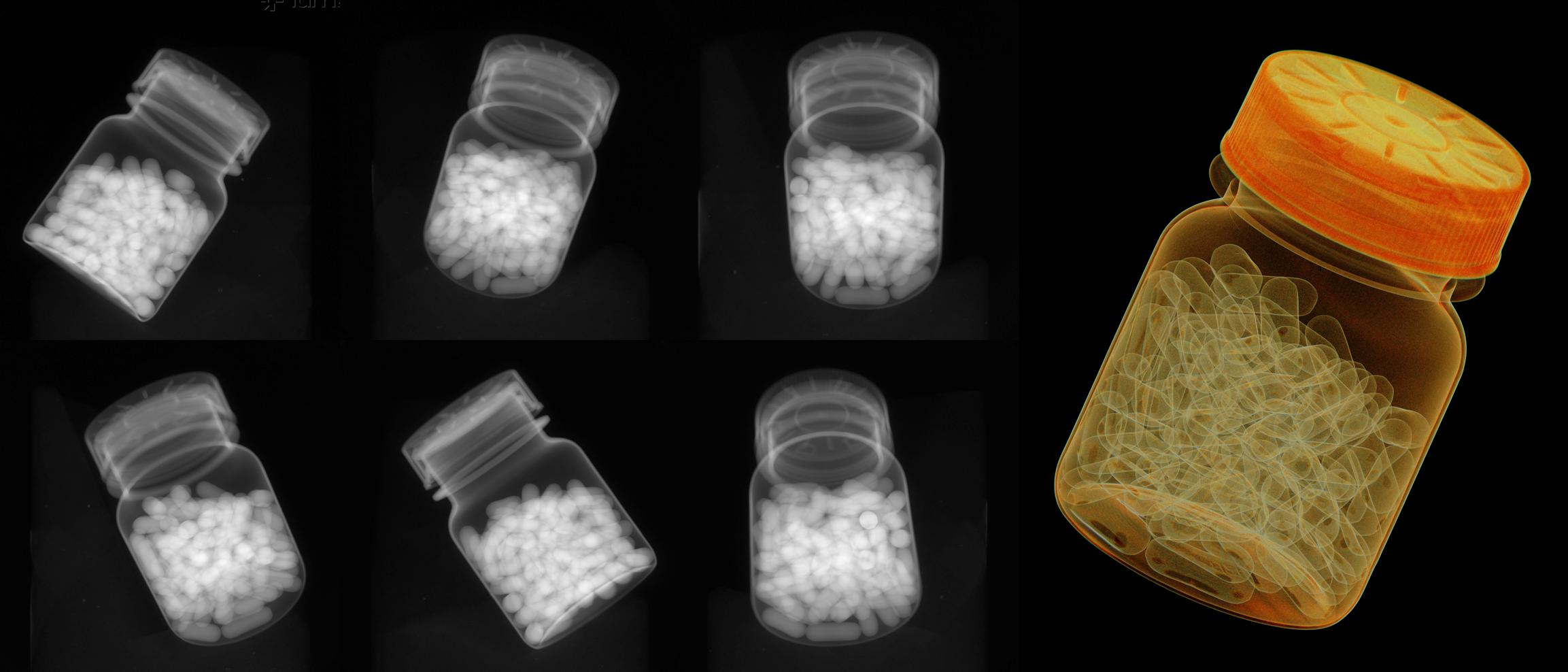
Industrial CT applications
The versatility of industrial CT extends beyond inspection. Engineers can export the 3D model to create mesh versions for 3D printing or integrate it into CAD software for further design work. This capability is crucial for identifying manufacturing deviations and ensuring product integrity. The CT 101 video series, part of our educational resources, delves deeper into these features and demonstrates their practical applications.
Industrial CT has evolved to support a wide range of applications, from office and lab environments to high-volume production lines. Our Triton CT scanner, for instance, is designed for in-line inspection, enabling manufacturers to detect hidden flaws before products reach the market. This is particularly beneficial in industries such as plastic packaging, medical devices, athletic equipment, and automotive manufacturing. Industrial CT provides a non-destructive, efficient, and precise method for inspecting complex assemblies, validating material integrity, and optimizing manufacturing processes.
For companies adopting new technologies like 3D printing, industrial CT is an invaluable tool. It allows for the inspection of intricate geometries and internal structures, facilitating the validation and refinement of innovative designs. By integrating CT scans into the product development lifecycle—from initial research and design to manufacturing and quality assurance—companies can save time, reduce costs, and improve overall product quality.
Learn more
At Lumafield, we are committed to making industrial CT accessible and practical for a wide range of industries. Our CT 101 series is designed to help you understand how our Neptune CT scanner and Voyager analysis software can revolutionize your product development and manufacturing processes.
To explore how industrial CT can solve your toughest engineering challenges, reach out to our team.
Get in touch.
Are you a current customer? Head over to our Support site for detailed documentation and tutorials.