Manufacturing Process: Metal Welding
Welding and joining are fundamental to modern metal manufacturing, with around 40 distinct processes available to securely fuse metal components. These techniques are essential for creating everything from aircraft structures to high-performance automotive parts. This guide focuses on three of the most widely used for metals: Spot Welding, Electron Beam Welding, and Laser Beam Welding.
These advanced welding methods allow manufacturers to create high-strength joints with speed, precision, and efficiency. In this guide, we’ll explore how each process works, what makes it uniquely suited to metal joining, and how it’s applied across various industries to meet modern manufacturing demands.
What is Spot Welding?
Spot welding, or Resistance Spot Welding (RSW), is a technique used to join metal sheets by applying electrical current and pressure to create a small, localized weld. It’s commonly used in automotive assembly, appliance manufacturing, and other industries requiring fast, strong, and efficient metal joining. Spot welding is particularly effective for materials like steel and aluminum and is ideal for high-speed production where strength is essential but appearance and airtight seals are less critical.
The Spot Welding Process
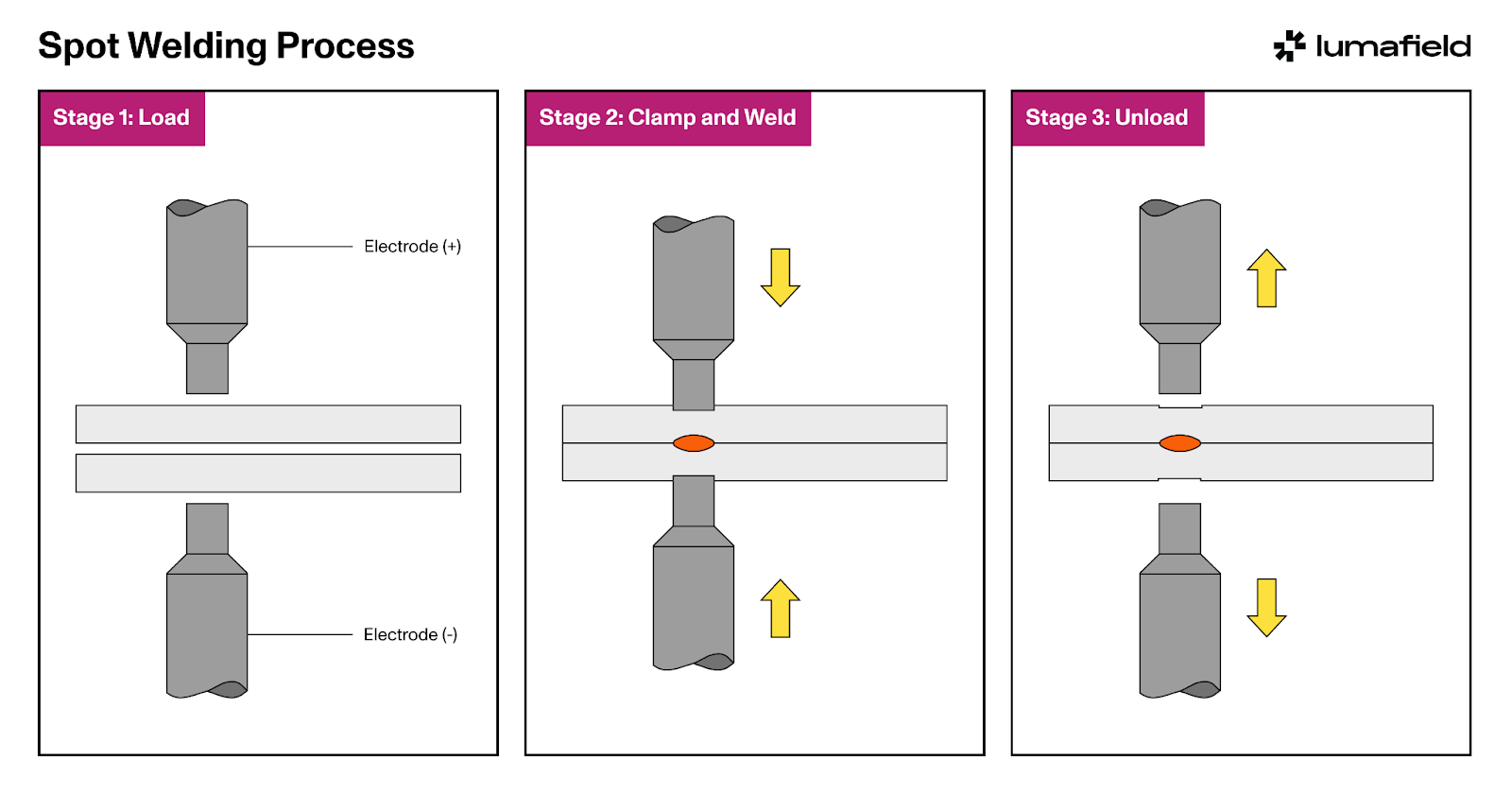
- Setup: Metal sheets are overlapped at the intended weld spot, with any contaminants removed for optimal bonding.
- Electrode Placement: Copper alloy electrodes are positioned on both sides of the sheets to focus the current precisely at the weld point.
- Current and Pressure Application: A high electrical current passes through the electrodes, generating heat from resistance at the contact point. Simultaneously, the electrodes apply pressure to compress the metals together.
- Weld Formation: The heat melts the metal at the contact point, creating a solid weld spot as it cools and solidifies under pressure. Each weld typically takes only a fraction of a second.
- Completion: The welded sheets are released, with automated quality checks often confirming that each spot weld is strong and consistent.
Spot welding’s speed and efficiency make it indispensable in mass production, especially for products like car bodies and appliances where strong, repeatable joints are crucial.
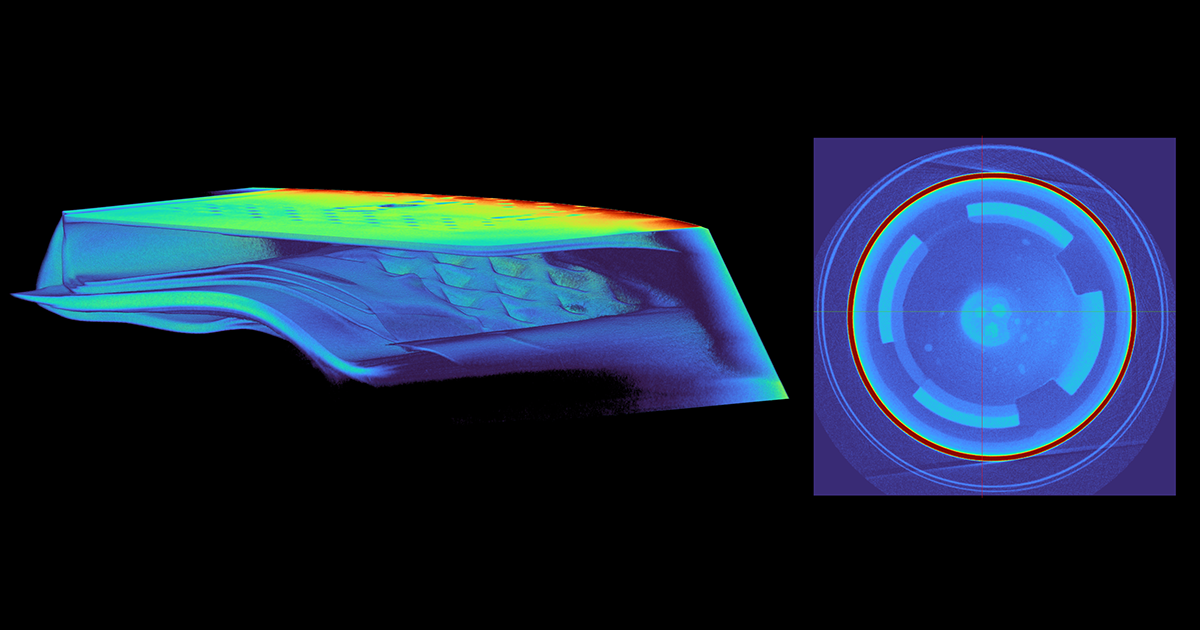
What is Electron Beam Welding?
Electron Beam Welding (EBW) is a highly precise welding process that uses a focused stream of high-velocity electrons to fuse metals. This process occurs in a vacuum, preventing contamination and allowing for deep, high-integrity welds. EBW is critical for industries requiring minimal heat distortion, such as aerospace and nuclear sectors.
The Electron Beam Welding Process
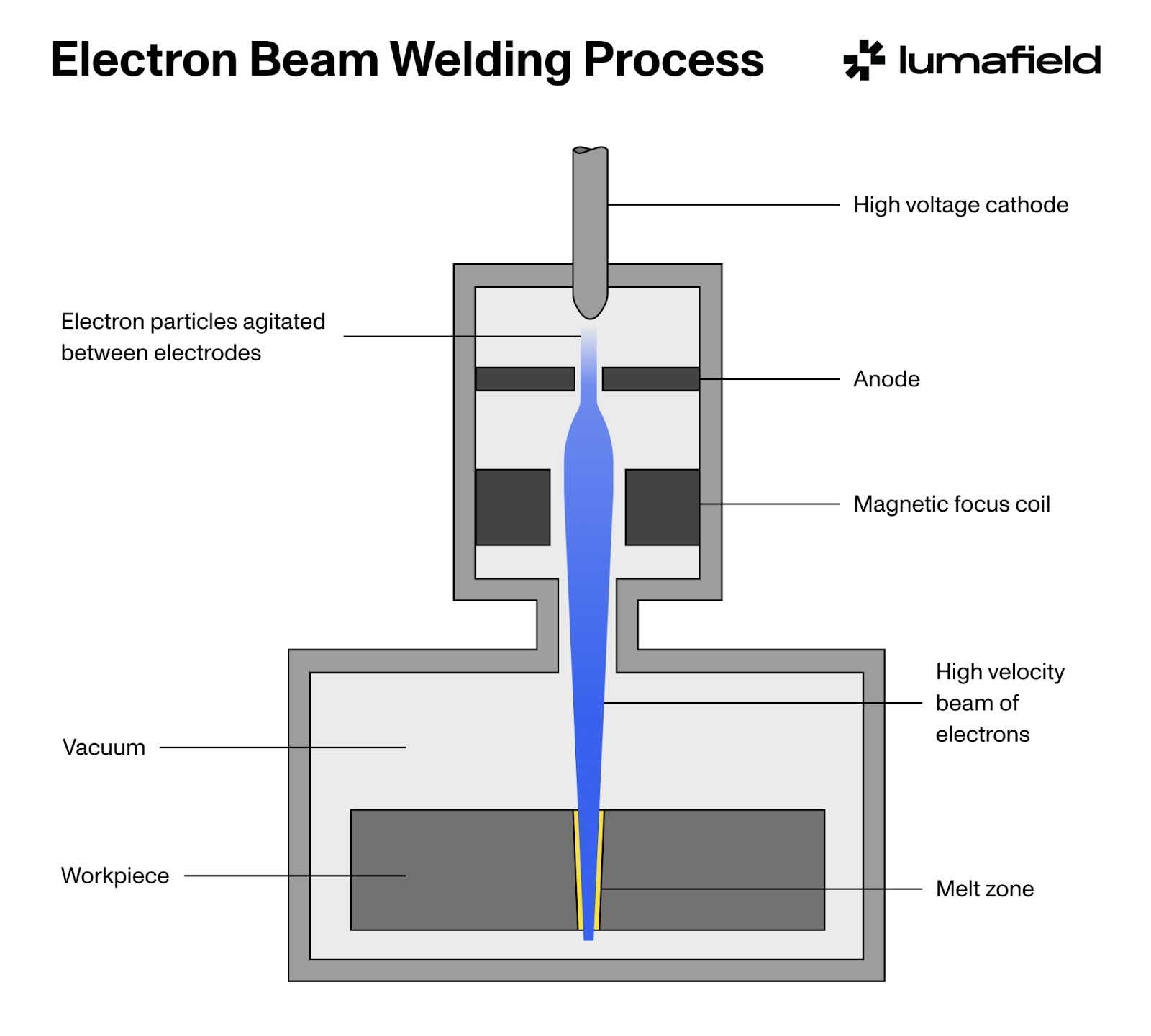
- Vacuum Chamber Setup: The parts to be welded, usually metal, are placed inside a vacuum chamber. This prevents the electron beam from scattering, ensuring a precise weld.
- Electron Beam Generation: A focused electron beam is generated and directed toward the materials, transferring kinetic energy into heat at the welding point.
- Welding: The intense heat from the electron beam melts the metals together at the joint, creating a deep, narrow weld. This precision allows for the joining of high-strength materials such as aerospace turbine blades, automotive racing parts, and nuclear reactor components, where distortion must be minimized.
- Cooling and Ejection: The part cools in the vacuum chamber, and the clean, high-integrity weld is complete.
EBW is especially useful for materials that must withstand extreme conditions, making it the go-to method for critical components in high-stress environments.
What is Laser Beam Welding?
Laser Beam Welding (LBW) uses a concentrated laser beam to melt materials at the weld joint, producing strong, precise welds with minimal heat-affected zones. LBW is widely used for both metals and thermoplastics, particularly in applications requiring fine control and high speeds, such as high-performance athletic equipment, electronics, and medical devices.
The Laser Beam Welding Process
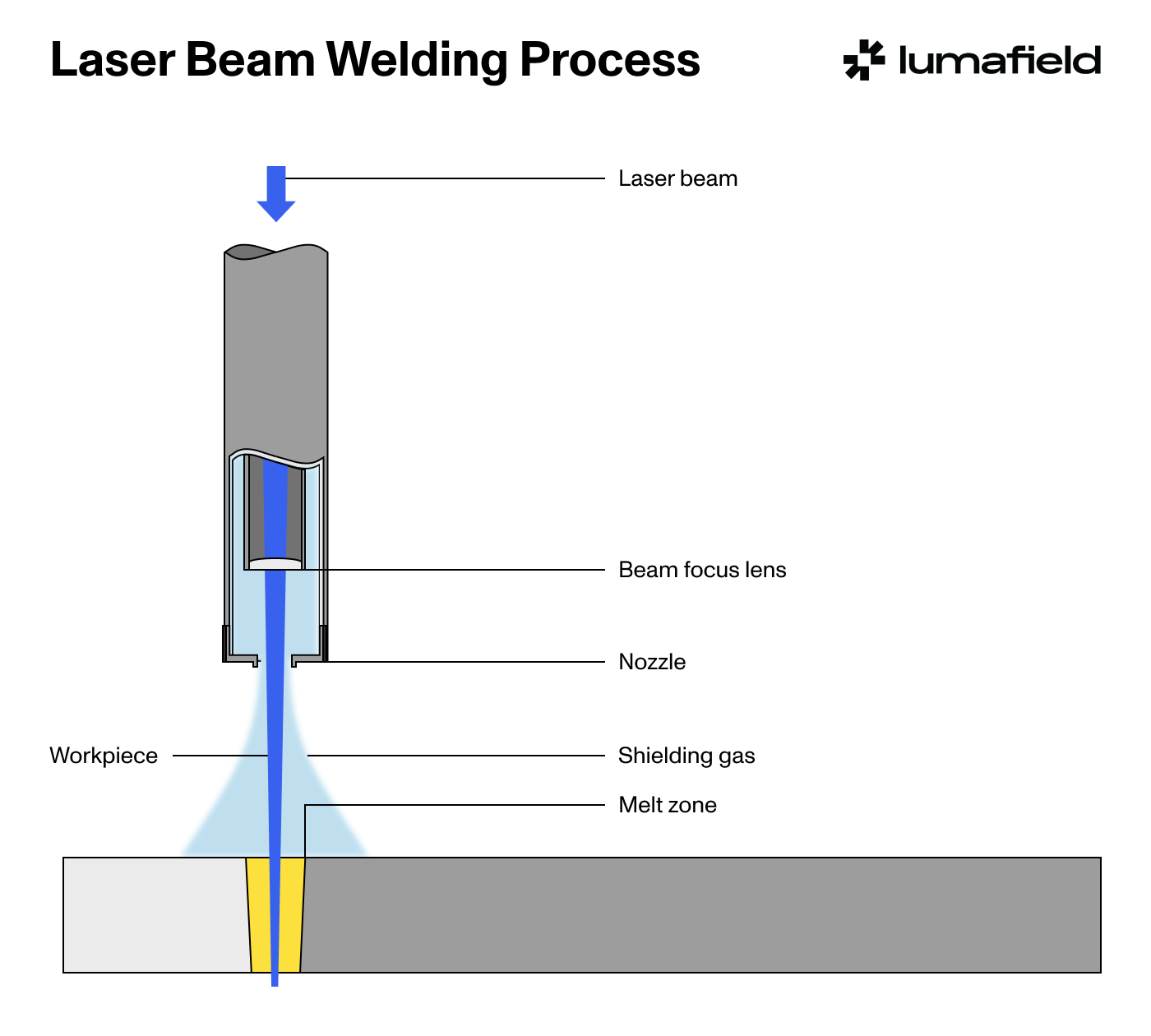
- Laser Generation: A laser beam, typically from a solid-state or CO2 laser, is directed toward the material with pinpoint accuracy.
- Welding: The focused laser rapidly heats the materials at the joint, causing them to melt and fuse. The intense, localized energy allows for precision welding with minimal heat distortion, ideal for assembling electric vehicle battery cells, medical implants, and fine jewelry where aesthetic and structural integrity are essential.
- Cooling: The rapid cooling that follows the laser weld results in a strong bond with minimal warping, ensuring that intricate or heat-sensitive components maintain their dimensional accuracy.
LBW’s speed, precision, and control make it indispensable for products that require high-quality welds with minimal post-processing, especially in the electronics and automotive industries.
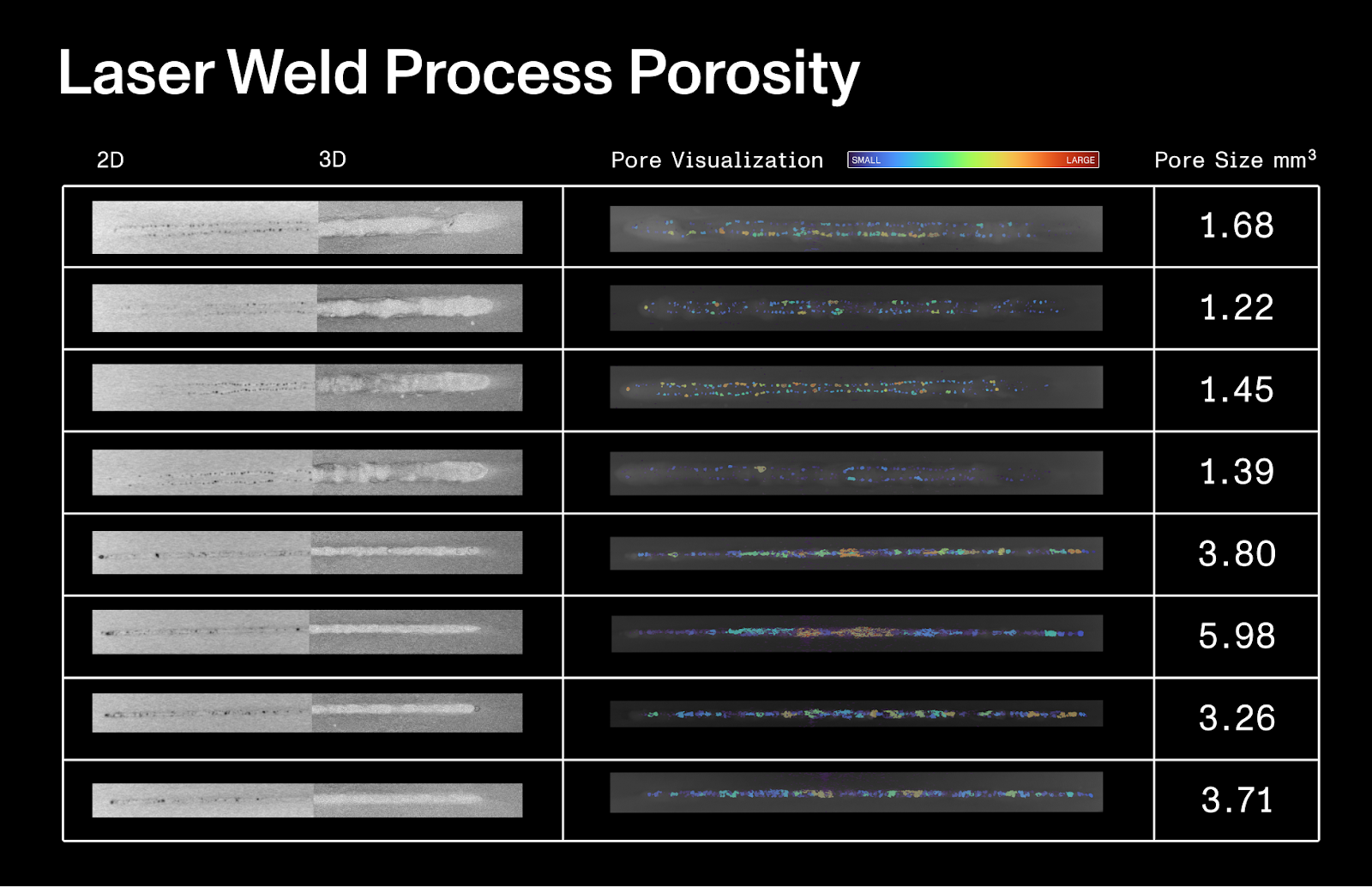
Design Considerations for Metal Welding
When designing for metal welding processes like Spot Welding, Electron Beam Welding (EBW), and Laser Beam Welding (LBW), several key factors ensure the strength, durability, and efficiency of the weld:
- Material Compatibility: Choosing the right welding method for the material is essential. Spot welding works best with steel and certain aluminum alloys, while EBW and LBW are suited for metals requiring high-precision and deep penetration, like titanium and stainless steel.
- Joint Design: For EBW and LBW, tight tolerances and precise joint design are critical to creating strong, reliable welds. The joint edges should be clean and well-prepared to ensure uniform fusion and structural integrity. Spot welding, on the other hand, requires sufficient overlap at each spot to maintain strength across the weld line.
- Heat Management: EBW and LBW generate significant localized heat, which can cause warping or distortion, especially in thin or delicate components. Designs should account for heat dissipation to minimize damage to surrounding areas, ensuring that components retain their intended dimensions and structural integrity.
- Part Size and Complexity: Spot welding is highly efficient for joining thin sheets and simple assemblies, such as automotive body panels. EBW and LBW, however, accommodate larger or more complex parts that require precise welds, making them ideal for aerospace and high-performance applications where intricate geometry and high strength are essential.
How Industrial CT Can Improve Metal Welding
Industrial CT scanning is an invaluable tool for evaluating and enhancing the quality of metal welds, providing non-destructive insights into the internal structure of welded joints across Spot Welding, Electron Beam Welding, and Laser Beam Welding processes.
- Detecting Internal Defects: CT scanning reveals hidden issues such as porosity, voids, and incomplete fusions that may compromise weld strength. This is especially crucial in EBW and LBW, where even minor defects can impact the durability of parts in high-stress applications like aerospace and automotive.
- Verifying Weld Penetration and Dimensional Accuracy: CT scans allow manufacturers to measure weld penetration depth and ensure the joint dimensions meet precise tolerances. This is essential for EBW and LBW applications where accurate depth control and consistent weld geometry are critical for performance and safety.
- Analyzing Heat-Affected Zones: In EBW and LBW, CT scans help identify the extent of heat-affected zones (HAZ) to ensure that thermal effects haven’t weakened surrounding material. This level of analysis helps maintain the strength and reliability of parts exposed to extreme conditions.
- Optimizing Process Parameters: CT data provides feedback on welding parameters like beam power, speed, and pressure, enabling manufacturers to fine-tune their settings to reduce defects and improve consistency, especially in high-volume production environments.
- Failure Analysis and Troubleshooting: When welds fail during testing or use, CT scanning can pinpoint the root cause, such as misalignment, internal cracks, or inadequate bonding. This information helps manufacturers make targeted adjustments to prevent similar issues in future production runs.
Conclusion
Spot Welding, Electron Beam Welding, and Laser Beam Welding each offer unique benefits in metal manufacturing, allowing manufacturers to produce strong, precise, and durable components. These methods are essential for joining metal parts with high integrity and performance. With industrial CT, manufacturers can fine-tune these processes, ensuring welds are consistent, defect-free, and aligned with the highest standards of quality.