Sweet Precision: CT and Food Safety
This Halloween, we’ve challenged you to guess your favorite candy based on its CT scan. But behind the fun competition lies a powerful tool that manufacturers in the food industry are increasingly turning to: industrial CT scanning. Just as we’ve X-rayed these treats for fun, Lumafield’s Neptune scanner and Voyager software are built to offer a much more serious value—ensuring product quality and safety at the highest level.
Let’s take a deeper dive into how industrial CT is transforming quality assurance and control in the food industry and beyond.
Detecting the Unseen: Foreign Material Identification
When consumers reach for their favorite candy, they trust that what’s inside is exactly what it should be. But production environments aren’t perfect, and foreign materials—like small pieces of plastic, metal, or other debris—can inadvertently end up in the final product. Magnets, metal detectors, and even traditional 2D X-ray methods often fall short when it comes to identifying these contaminants, especially if they’re embedded within complex textures or shapes. For example, a fiberglass staple that ended up in a bag of chocolate candies might evade all of these tools, blending in with its surroundings because of how similar its density is to the surrounding candy.
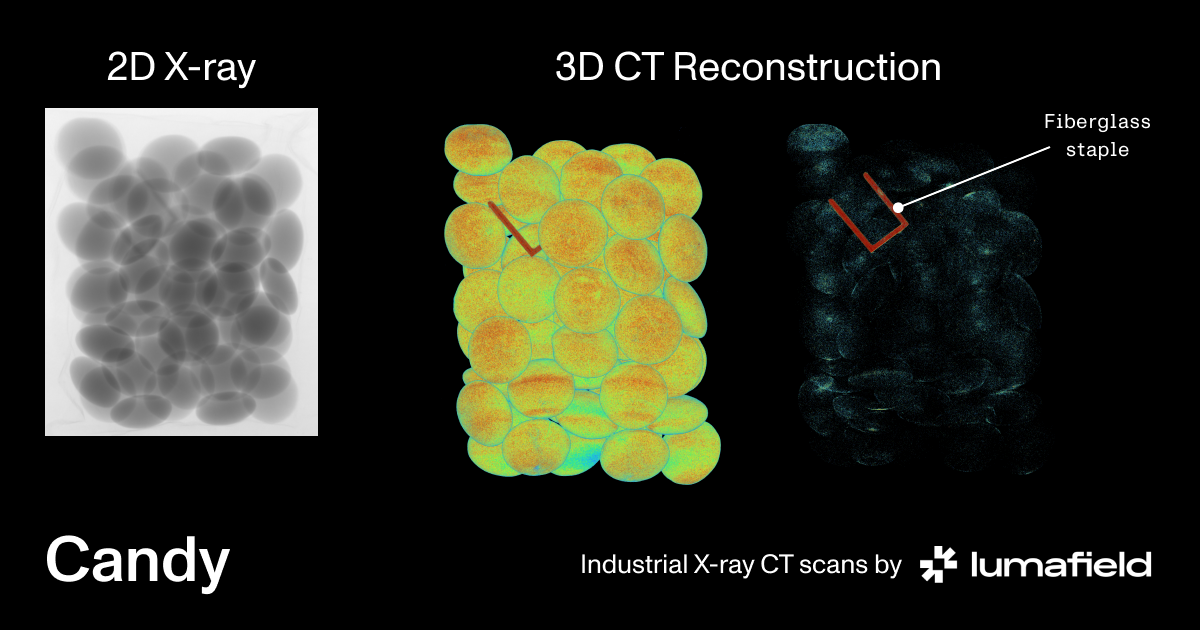
Lumafield’s Neptune CT scanner, however, provides a three-dimensional perspective with much-richer density information, allowing manufacturers to pinpoint and isolate foreign objects quickly and reliably. For high-volume production environments, Lumafield’s Triton scanner automates this process with ease. Designed for 100% inspection at unprecedented speed, Triton can detect foreign materials in every single item on the line, catching contaminants in real time. Once Triton identifies a foreign object, it can trigger automated systems to remove the contaminated product from the line, ensuring that only perfect candy makes it to packaging.
Porosity Analysis: Ensuring Product Integrity
Ever wondered why your Snickers bar is so satisfyingly smooth? One reason is the control of porosity during the manufacturing process. In food production, voids or air pockets can compromise the texture, quality, and shelf life of products. With Lumafield’s Porosity Analysis feature, manufacturers can not only visualize but also quantify these voids in a single scan.
By analyzing cross-sections of a Snickers bar, we can detect small pockets of air that may have formed during production. These voids, while harmless in a candy bar, could cause significant issues in other types of products, such as baked goods, where air bubbles might lead to structural collapse. Porosity analysis helps food manufacturers maintain consistency, ensuring every product delivers the quality their customers expect.
Food Industry Applications
Industrial CT scanning goes beyond just identifying contaminants or ensuring product consistency. Here are some other ways Lumafield’s technology is making a difference in food and packaging manufacturing:
- Seal Integrity Testing: CT scans provide a detailed view of packaging seals, identifying gaps, misalignments, or weaknesses that can lead to air leaks, contamination, or spoilage.
- Packaging Inspection: CT scans detect structural inconsistencies, such as delamination or defects in multi-layered materials, ensuring that packaging performs as designed.
- Leak Detection: CT technology non-destructively visualizes potential leaks by analyzing internal structures, offering a more precise method than traditional inspection.
- Shelf Life Optimization: By simulating real-world conditions, CT scans help manufacturers test packaging durability, optimize material choices, and reduce waste.
- Weight Distribution & Fill-Level Verification: CT scans ensure consistent fill levels and weight distribution, providing a non-invasive method for verifying packaging uniformity.
Reducing Recalls and Protecting Your Brand
In an industry where consumer trust is everything, even a small recall can have permanent consequences for a brand. CT scanning offers an advanced, non-destructive method for proactively identifying defects and contaminants that could lead to recalls. By integrating this technology into your quality control process, you can catch issues before they become costly problems, helping you safeguard your brand reputation and reduce waste.
With Neptune, Triton, and Voyager, Lumafield is proud to bring the future of food quality assurance to the present. And as you guess the candy from its CT scan this Halloween, remember that the same technology keeping your treats safe can ensure quality in every corner of the food industry.
Want to learn more about how Lumafield’s technology can help you improve quality assurance in your production process? Get in touch to schedule a demo or discuss how Neptune and Voyager can be integrated into your workflow.