What is High-Mix Low-Volume (HMLV) Manufacturing?
High-Mix Low-Volume (HMLV) manufacturing is an approach gaining traction in industries where customization, flexibility, and speed are critical. Unlike traditional mass production, which focuses on producing large quantities of identical products, HMLV manufacturing emphasizes the production of small batches of varied products. This strategy is particularly valuable in sectors like aerospace, automotive, medical devices, and consumer electronics, where the demand for personalized or specialized components is high and growing all the time.
What is High-Mix Low-Volume (HMLV) manufacturing?
Let’s break down the two components of HMLV manufacturing:
- High-Mix: A wide array of products or product variations are produced, often with different specifications, materials, or designs.
- Low-Volume: Each product type is produced in small quantities, which can range from a few units to a few thousand.
This manufacturing strategy allows companies to meet diverse customer needs, respond quickly to market changes, and innovate rapidly. However, it also introduces significant challenges, particularly in terms of quality control, efficiency, and cost management.
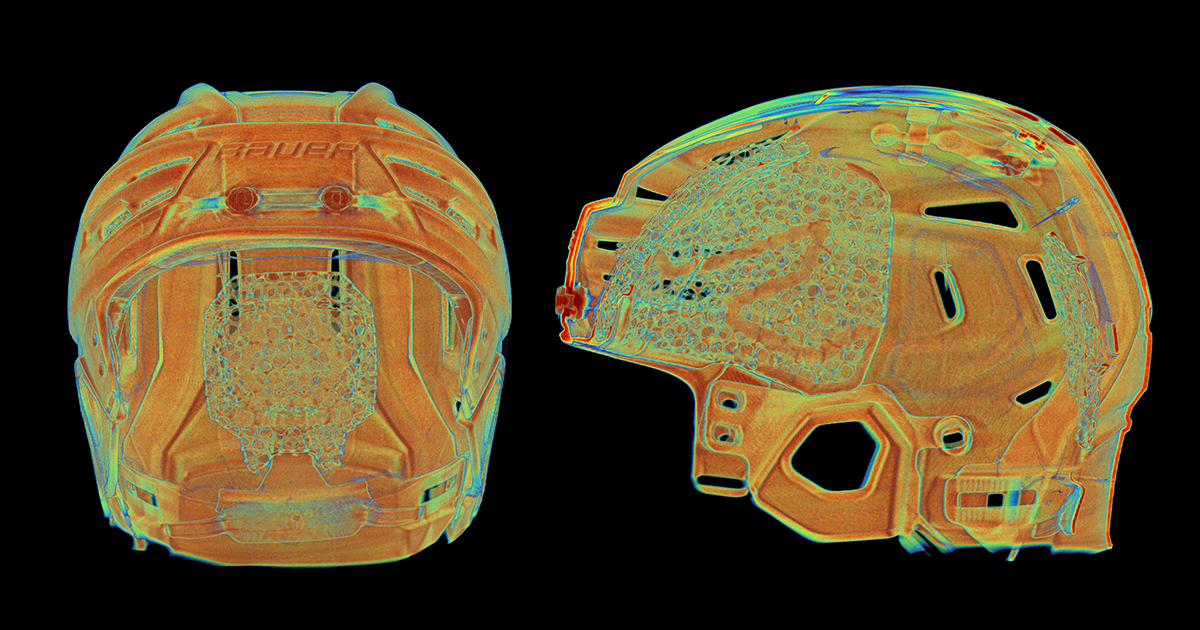
Examples of HMLV products
High-Mix Low-Volume (HMLV) manufacturing is particularly suited to industries where customization, precision, and rapid adaptability are essential. Below are a few examples of products that thrive in an HMLV environment:
- Luxury and high-performance automobiles: Luxury car manufacturers often offer a high degree of customization to meet the specific tastes and requirements of their customers. From custom interior finishes to specialized performance components, each vehicle may require a unique set of parts produced in low volumes. For example, custom exhaust systems, bespoke leather interiors, or limited-edition models are all produced using HMLV manufacturing techniques to ensure each vehicle meets the exact specifications desired by the buyer.
- Aerospace components: The aerospace industry frequently relies on HMLV manufacturing for producing specialized components like turbine blades, avionics enclosures, and custom fasteners. These parts often require materials and processes that can handle extreme conditions and precise tolerances. Due to the low production volumes and the need for various customizations depending on the aircraft model or mission, HMLV is the go-to manufacturing approach for aerospace components.
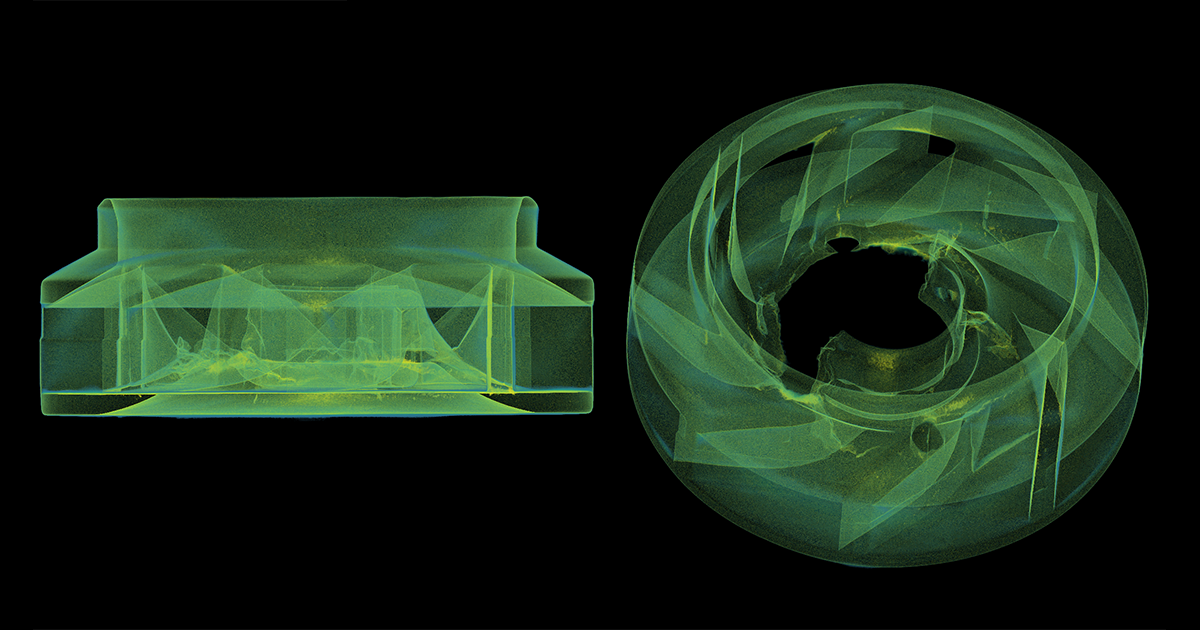
- Consumer electronics: High-end consumer electronics, such as specialized audio equipment or limited-run gadgets, also benefit from HMLV manufacturing. These products often feature custom designs, materials, and functionalities that are tailored to niche markets. For example, a company might produce a limited batch of high-fidelity headphones with custom tuning options or materials based on customer orders. The ability to quickly adapt production to these varied specifications while maintaining high quality is key in this sector.
- Sporting equipment: Athletic goods, such as custom-fit helmets, high-performance bicycles, or personalized golf clubs, exemplifies HMLV manufacturing. Companies like Bauer, for instance, create custom hockey helmets tailored to the unique measurements of each player’s head, ensuring optimal fit and safety. These products require a high degree of customization, with production processes that can adapt to varying specifications without compromising quality or efficiency.
- Medical devices: Medical devices such as customized implants, surgical instruments, and prosthetics are prime examples of HMLV products. Each device often needs to be tailored to individual patient anatomy or specific medical requirements. For instance, dental implants are custom-made to fit a patient’s mouth precisely, requiring small production runs of varied sizes and shapes. The high degree of customization and the critical nature of these devices make HMLV manufacturing essential for ensuring both quality and adaptability.
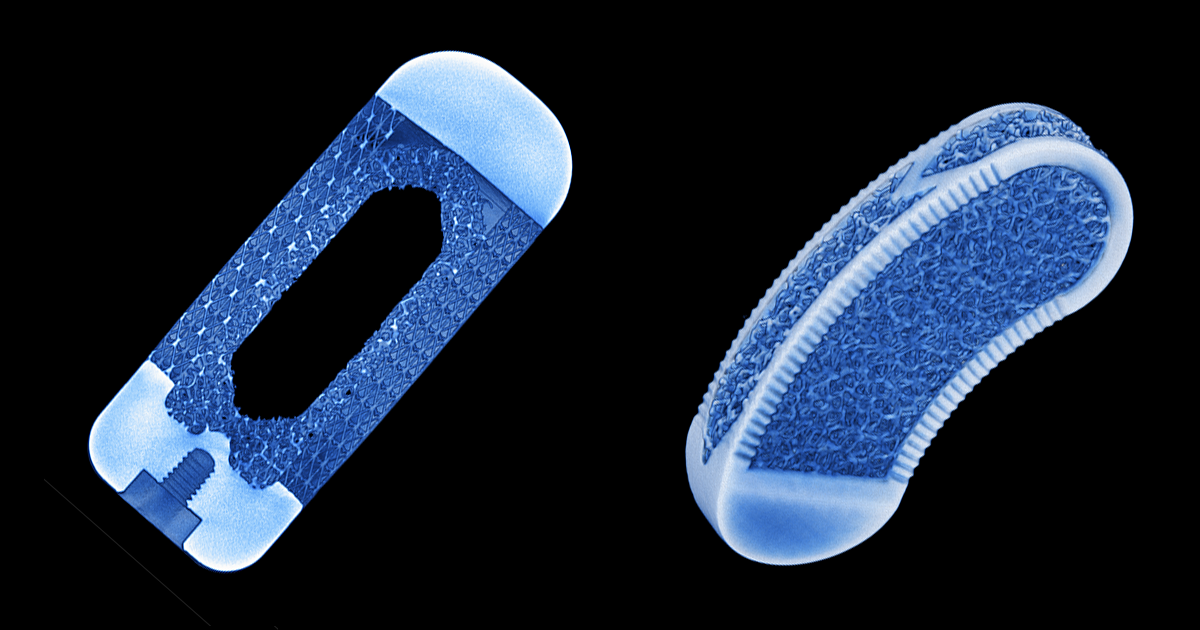
HMLV manufacturing challenges
- Production complexity: High-Mix Low-Volume manufacturing involves frequent changeovers between different product setups. This creates significant complexity in managing the diverse range of products, each with unique specifications and requirements. The constant need for reconfiguration can lead to inefficiencies and delays, making it difficult to maintain a streamlined production process.
- Quality assurance: In HMLV environments, ensuring consistent quality across varied, small-batch productions is challenging. Traditional inspection methods often lack the precision and adaptability required to detect defects in products with complex geometries or diverse material compositions. This variability increases the risk of undetected flaws, potentially leading to higher rates of rework or product failure.
- Inventory management: Balancing inventory in HMLV manufacturing is particularly difficult due to the need for a wide array of components, each required in small quantities. Overstocking leads to higher costs and wasted resources, while understocking can cause production delays. Managing this delicate balance without compromising efficiency is a persistent challenge.
- Cost constraints: Economies of scale are less accessible in low-volume production, leading to higher per-unit costs. Manufacturers must find ways to optimize their processes to maintain cost efficiency without compromising quality or speed. This is especially challenging when producing highly customized products in small batches.
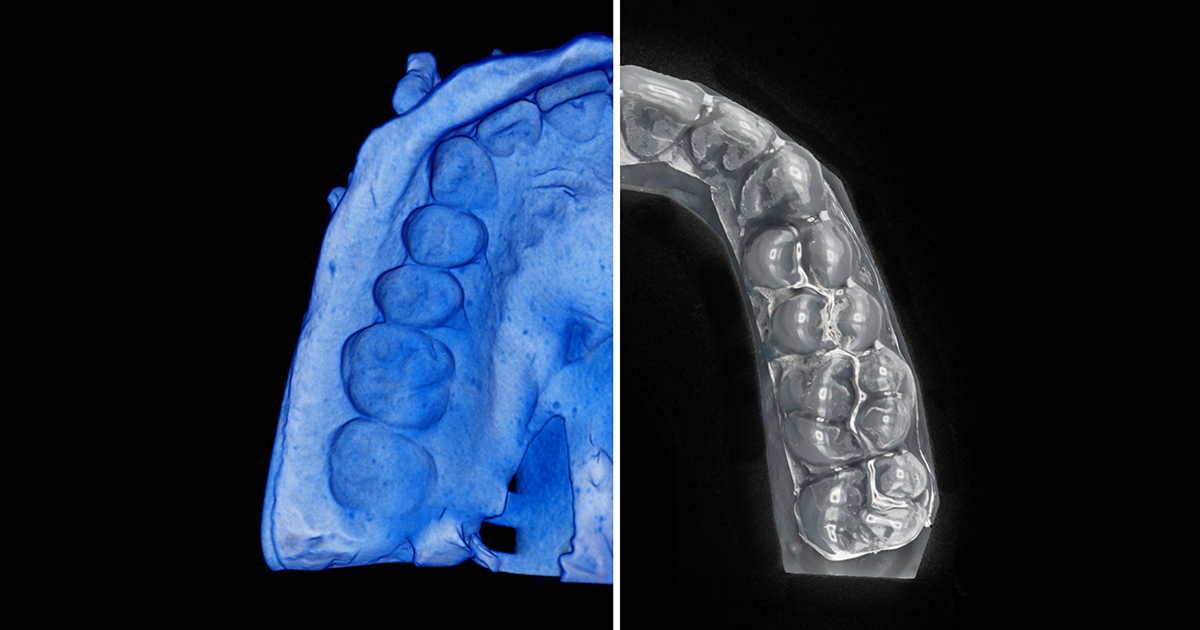
Overcoming the challenges of HMLV
- Streamlined process adaptability: To handle the complexity of HMLV production, manufacturers need tools that facilitate quick and efficient changeovers. These tools should allow for seamless transitions between different product setups, reducing downtime and maintaining the flow of production. Flexibility in manufacturing equipment and software is crucial to managing the diverse product mix without sacrificing efficiency.
- Precision inspection capabilities: Given the challenge of maintaining quality in a variable production environment, manufacturers must employ inspection methods that offer high precision and can accommodate a wide range of product types. These tools should be capable of detecting internal and external defects in even the most complex geometries, ensuring that every product meets rigorous quality standards, regardless of batch size.
- Inventory optimization solutions: Effective inventory management in HMLV manufacturing requires systems that can accurately predict component needs and streamline supply chain operations. Advanced software tools that integrate demand forecasting with real-time inventory tracking can help balance stock levels, minimizing both overstock and shortages while keeping production on schedule.
- Scalable cost management: To address the higher costs associated with low-volume production, manufacturers should leverage technologies that provide high value without the high price tag. These solutions need to offer the ability to perform detailed inspections and process optimizations at a fraction of the traditional cost, enabling manufacturers to maintain profitability even in small-scale operations.
- Comprehensive data utilization: Incorporating data-driven approaches into manufacturing processes allows for continuous monitoring and improvement. The ability to collect and analyze detailed production data enables manufacturers to optimize their processes, reduce waste, and enhance product quality over time. This proactive approach to data utilization helps in making informed decisions that drive long-term success.
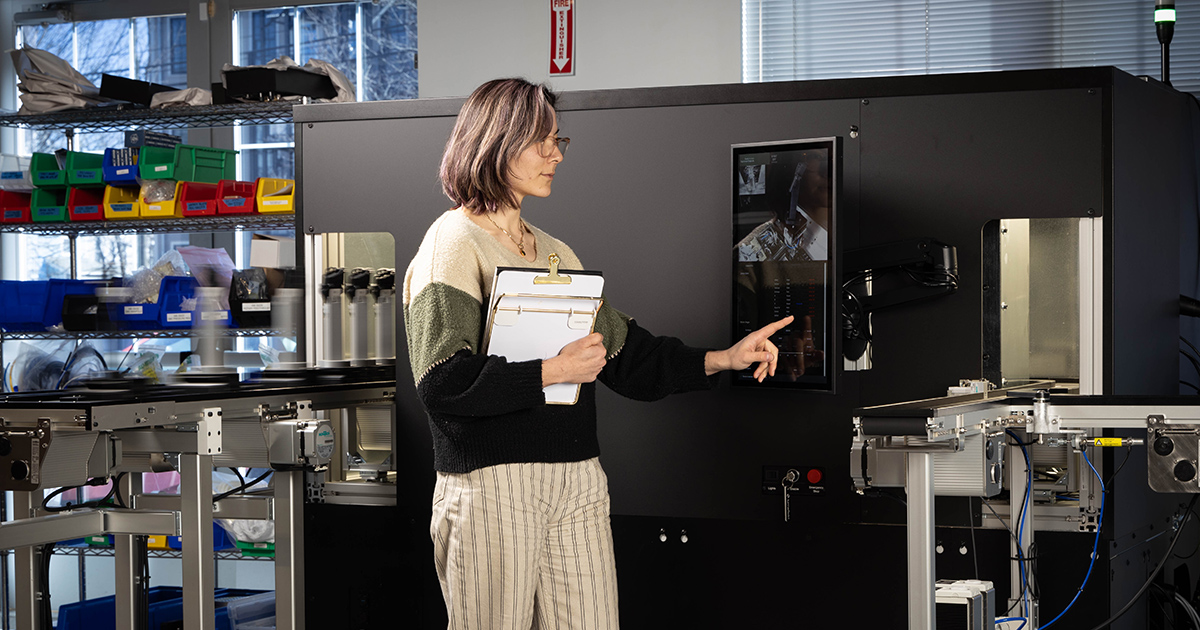
How industrial CT enables HMLV manufacturing
The demands of High-Mix Low-Volume manufacturing require a solution that meets all of these criteria—rigorous quality control, versatility, speed, cost-effectiveness, and data-driven insights. Industrial CT scanning emerges as the ideal technology to address these needs.
Industrial CT provides the precision required for thorough inspections, capable of revealing even the smallest internal and external defects. Versatile systems like the Neptune scanner can handle a wide range of materials and product types without extensive reconfiguration. The speed at which CT scans can be performed on high-throughput platforms like Triton ensures that quality control keeps pace with production demands, while the relatively lower cost of modern CT solutions makes this advanced technology accessible to manufacturers of all sizes.
Comprehensive 3D CT data can be viewed, analyzed, and shared in the browser-based Voyager software. Analysis workflows offer invaluable insights for process optimization, product development, and quality assurance, making industrial CT an essential tool in the HMLV manufacturing landscape. By integrating industrial CT scanning into their processes, manufacturers can overcome the challenges of HMLV production, ensuring high quality, efficiency, and profitability in even the most complex manufacturing environments.