Manufacturing Process: Plastic Welding and Joining
Plastic welding and joining lie at the heart of many modern manufacturing processes, bringing together durable, high-performance components for industries ranging from medical devices to automotive and consumer electronics. Unlike traditional mechanical fasteners or adhesives, advanced methods like Ultrasonic Welding, Radiofrequency (RF) Welding, and Epoxy Bonding offer cleaner, more efficient, and precise ways to bring plastic materials together.
These techniques are not one-size-fits-all. Each method has unique strengths suited to specific materials, geometries, and applications. Ultrasonic Welding excels in precision and speed for rigid plastics, while RF Welding proves best when flexible plastics need airtight or watertight seals. Epoxy Bonding stands apart as a versatile solution for joining dissimilar materials or handling harsh environments. In this guide, we’ll explore how these processes work, their differences, and their roles in creating products we rely on every day.
What is Ultrasonic Welding?
Ultrasonic Welding uses high-frequency mechanical vibrations to bond thermoplastics. By generating localized frictional heat, it melts the plastic at the joint interface, creating a strong, clean bond without the need for adhesives or fasteners. This process is extremely fast and precise, making it ideal for assembling components like medical devices (syringes and IV connectors), consumer electronics (smartphone casings and headphones), and automotive parts (dashboards and air filters).
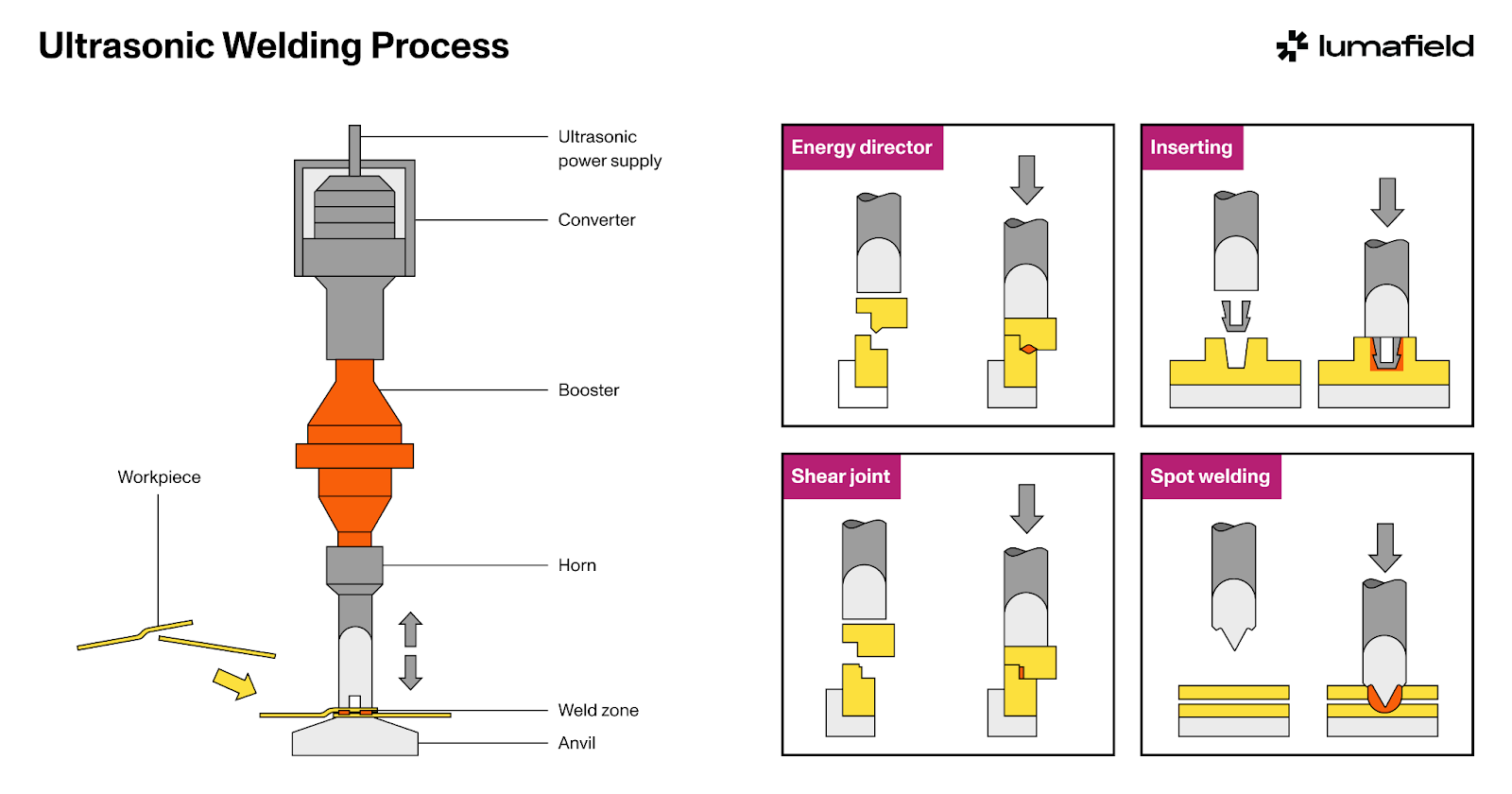
The Ultrasonic Welding Process
- Clamping: The plastic parts are placed in a fixture to ensure proper alignment. A vibrating “horn” (sonotrode) is positioned against the joint.
- Vibration: High-frequency vibrations (20–40 kHz) are applied through the horn, generating frictional heat at the contact surfaces.
- Melting and Bonding: The heat melts the plastic at the interface, and as the vibrations stop, the melted plastic fuses and solidifies into a durable joint.
- Ejection: The completed part is released, ready for use with no additional finishing steps needed.
Ultrasonic welding’s speed, precision, and cleanliness make it the perfect fit for industries relying on high-quality plastic assemblies.
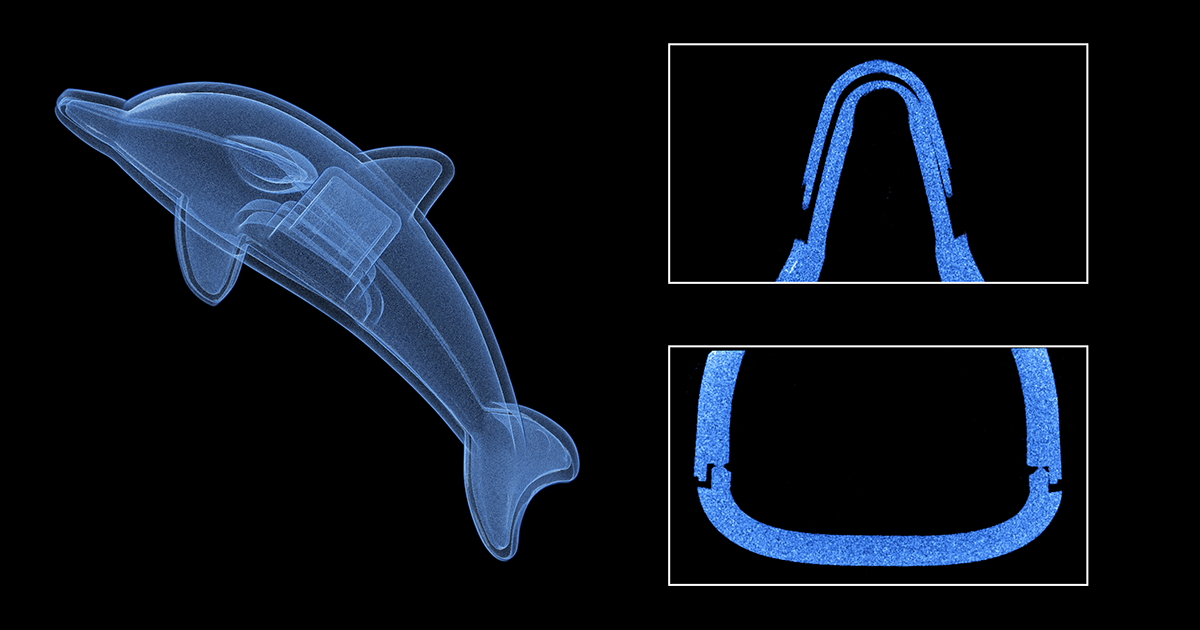
What is Radiofrequency (RF) Welding?
Radiofrequency (RF) Welding, also called High-Frequency Welding, uses electromagnetic energy to bond plastics with polar molecular structures, such as PVC and polyurethane. Unlike ultrasonic welding, which generates localized frictional heat, RF welding excites molecules within the material to produce internal heat, creating strong, uniform bonds. This method is ideal for producing airtight medical bags, inflatable products like air mattresses, and watertight industrial packaging.
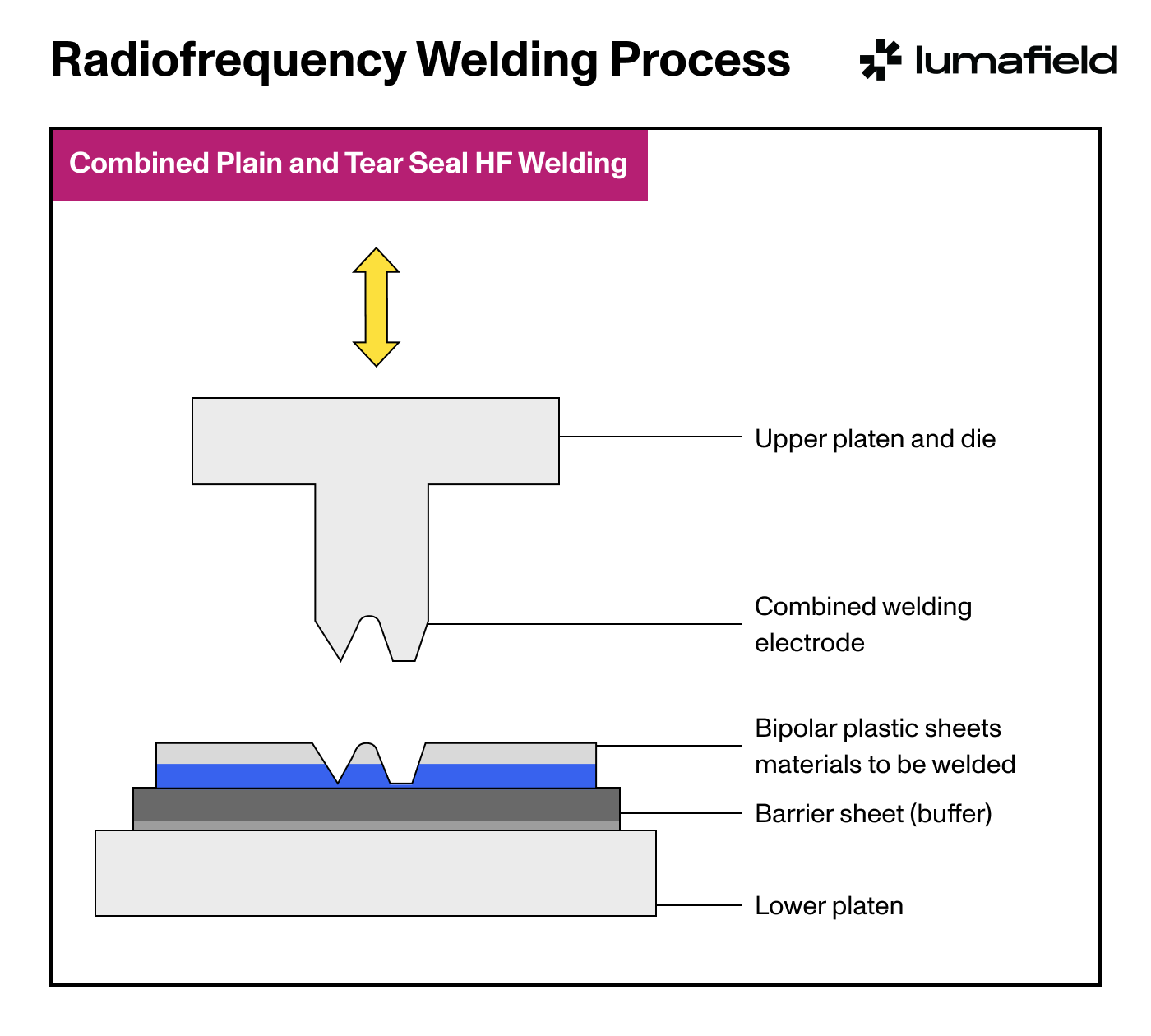
The Radiofrequency (RF) Welding Process
- Material Preparation: The plastic components or sheets are aligned in the welding fixture for consistent contact at the joint.
- Electromagnetic Energy Application: A high-frequency electromagnetic field (13.56 MHz) is applied between two electrodes. The polar molecules in the plastic generate heat as they react to the energy.
- Melting and Bonding: The internal heat softens the material, and with the electrodes applying pressure, the plastics fuse together seamlessly.
- Cooling and Ejection: The energy stops, and the bond solidifies as the material cools, creating a durable and consistent weld.
RF welding is the go-to method for flexible plastics, especially in applications requiring strong seals and uniform durability across large surface
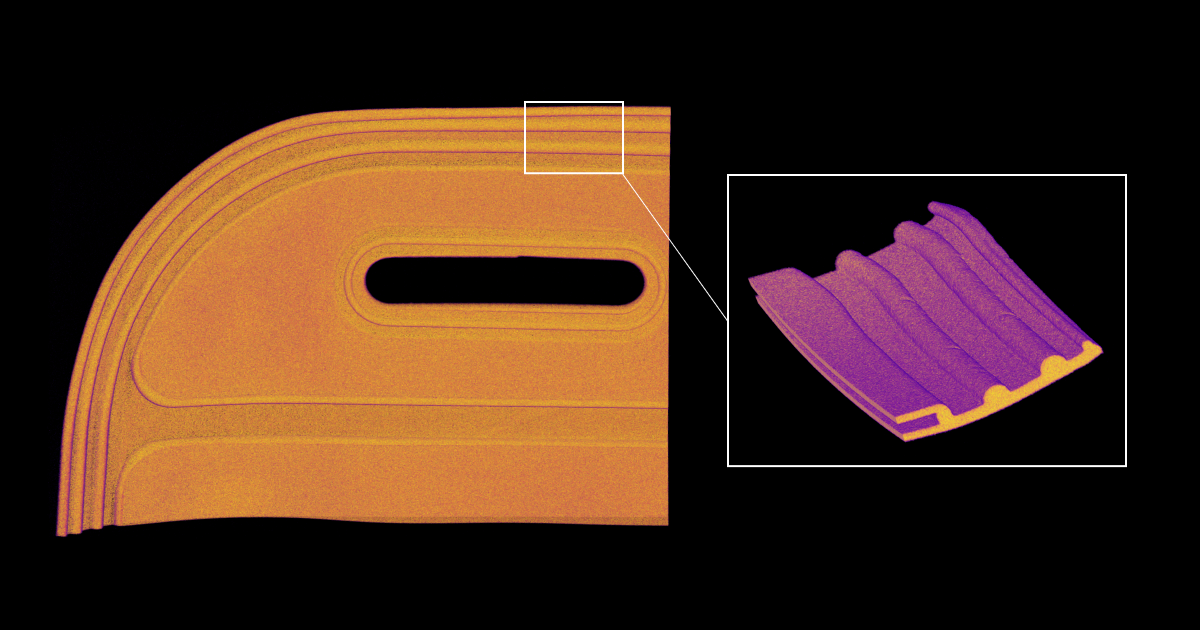
What is Epoxy Bonding?
Epoxy Bonding is a chemical joining method that uses an adhesive resin and hardener to create permanent bonds. Unlike Ultrasonic or RF Welding, Epoxy Bonding doesn’t rely on heat or electromagnetic energy, making it ideal for joining dissimilar materials or complex assemblies. It’s widely used to bond aerospace composites, industrial equipment exposed to harsh environments, and consumer products like outdoor furniture or plastic housings.
The Epoxy Bonding Process
- Surface Preparation: The surfaces to be bonded are cleaned and sometimes roughened to improve adhesion. Any contaminants, oils, or dirt are removed.
- Epoxy Application: The resin and hardener are mixed and applied to one or both surfaces, either manually or through automated equipment.
- Joining and Clamping: The parts are aligned and clamped to ensure consistent contact while the adhesive cures.
- Curing: The epoxy undergoes a chemical reaction over time (minutes to hours), forming a strong, durable bond that often exceeds the strength of the original materials.
Epoxy Bonding is the most versatile of the three methods, capable of joining plastics to metals, ceramics, or other dissimilar materials while providing excellent resistance to environmental stresses.
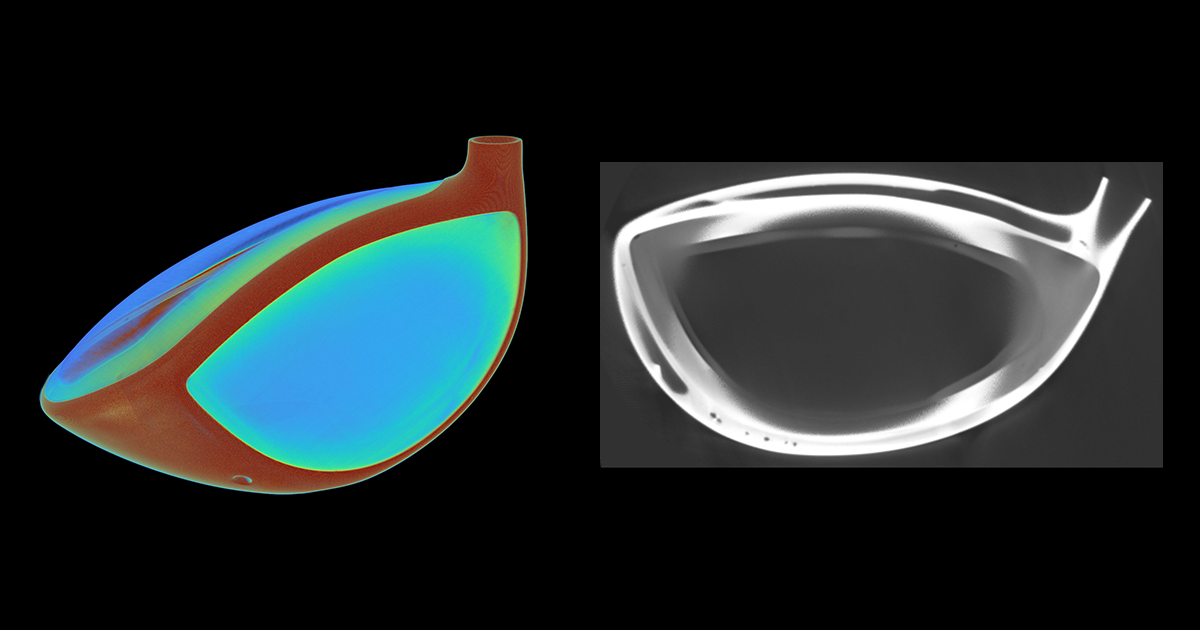
Design Considerations for Welding
When designing parts for Ultrasonic Welding, RF Welding, or Epoxy Bonding, it’s essential to consider the specific requirements of each process:
- Material Compatibility: Ultrasonic Welding is best for rigid thermoplastics, RF Welding works for flexible polar plastics like PVC, and Epoxy Bonding is ideal for joining dissimilar materials.
- Joint Design: Ultrasonic Welding benefits from energy directors (small ridges to focus vibrations), while RF Welding requires overlap for seals. For Epoxy Bonding, ensuring sufficient surface area and clean contact improves joint strength.
- Production Speed: Ultrasonic Welding is the fastest, completing welds in seconds. RF Welding takes longer but creates highly uniform seals, while Epoxy Bonding requires curing time, making it slower but more versatile.
- Environmental Resistance: Epoxy Bonding offers superior resistance to chemicals, heat, and moisture, while Ultrasonic and RF Welding bonds are less suitable for extreme conditions.
How Industrial CT Can Improve Plastic Welding and Joining
Industrial CT scanning is a critical tool for assessing the quality and integrity of welded joints, offering non-destructive, internal analysis of plastic welds.
- Detecting Bond Integrity: CT scans reveal voids, gaps, or incomplete bonds in ultrasonic and RF welds, ensuring consistent strength and durability.
- Verifying Alignment and Dimensions: CT scanning ensures welded or bonded parts are properly aligned and meet tight tolerances, critical for precision applications like medical devices or electronics.
- Failure Analysis: For epoxy-bonded parts, CT can identify air pockets, curing inconsistencies, or internal cracks that could weaken the bond and lead to premature failure.
- Optimizing Welding Parameters: CT data helps refine ultrasonic and RF welding parameters, such as energy levels and pressure, to reduce defects and improve bond consistency.
Conclusion
Ultrasonic Welding, Radiofrequency Welding, and Epoxy Bonding each provide tailored solutions for joining plastic components in industries like medical devices, automotive, and consumer electronics. From the speed and precision of ultrasonic welding to the versatility of epoxy bonding and the uniform seals of RF welding, these methods are essential for modern manufacturing. Combined with industrial CT scanning, manufacturers can ensure exceptional quality, reliability, and performance, meeting the rigorous demands of today’s plastic assembly applications.