Manufacturing Process: Casting
Casting is one of the most versatile manufacturing techniques, with a history dating back to antiquity. The process of pouring molten material into a mold makes it possible to create an astonishing range of metal parts with a high degree of complexity. From lightweight automotive components to intricate aerospace parts, casting delivers precision and efficiency at scale. This guide explores four key casting processes—both High- and Low-Pressure Die Casting, Investment Casting, and Sand Casting—focusing on how each meets unique needs across industries.
What is High-Pressure Die Casting?
High-Pressure Die Casting (HPDC) is a process where molten metal, such as aluminum or magnesium, is injected into a steel mold at high pressure. This method is ideal for producing lightweight, high-strength components with tight tolerances. HPDC is widely used for making automotive parts like engine blocks and transmission housings, as well as consumer electronics casings where precision and volume are key.
The HPDC Process
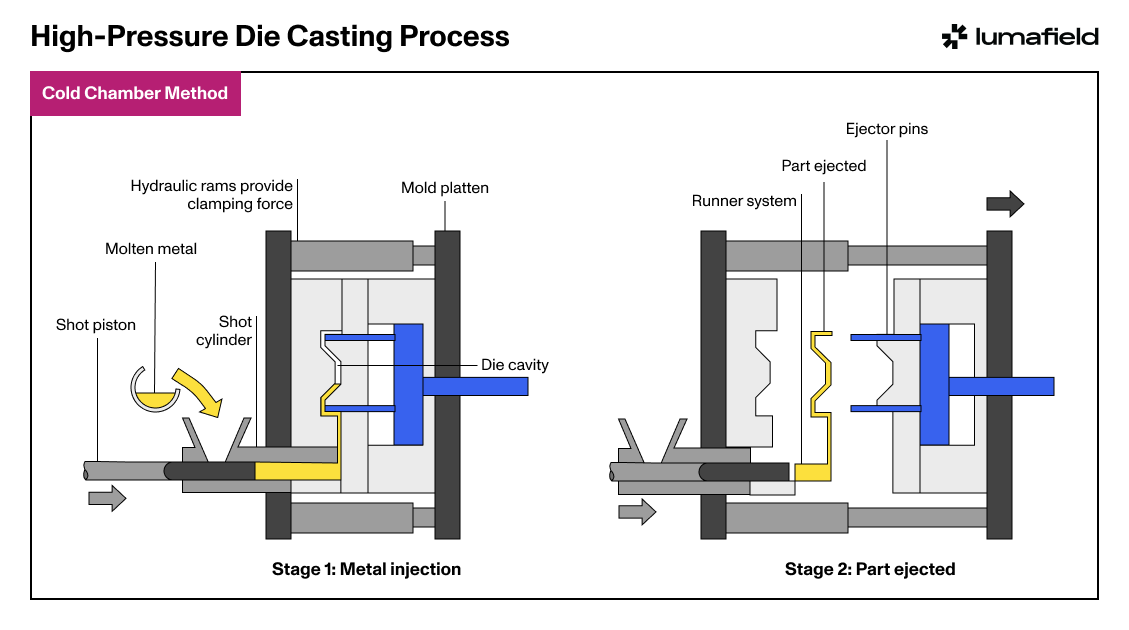
- Injection: Molten metal is forced into the mold cavity at extreme pressure.
- Solidification: The metal quickly cools and solidifies, retaining the mold’s intricate details.
- Ejection: The part is ejected and undergoes minimal post-processing.
What is Low-Pressure Die Casting?
Low-Pressure Die Casting (LPDC) uses controlled, low-pressure air to push molten metal into a mold. This slower, more controlled process reduces turbulence, creating parts with superior mechanical properties. LPDC is ideal for automotive wheels, structural components, and parts requiring enhanced strength and surface quality.The LPDC Process
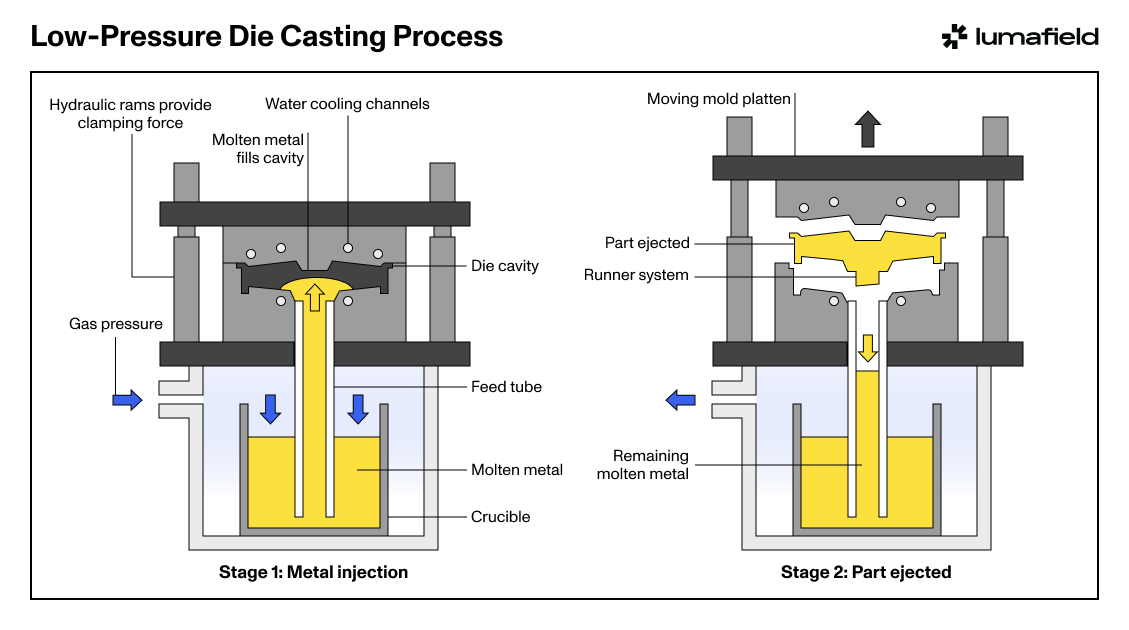
- Filling: Molten metal is gently pushed into the mold, reducing air entrapment.
- Cooling: The metal solidifies evenly, resulting in dense, high-quality parts.
- Ejection: The finished part is removed for secondary operations.
What is Investment Casting?
Investment Casting, or lost-wax casting, is a precision process for creating highly detailed components. Wax patterns are coated with ceramic to form molds, which are then filled with molten metal. Used in aerospace turbine blades, medical implants, and jewelry, investment casting produces intricate parts with excellent surface finish.
The Investment Casting Process
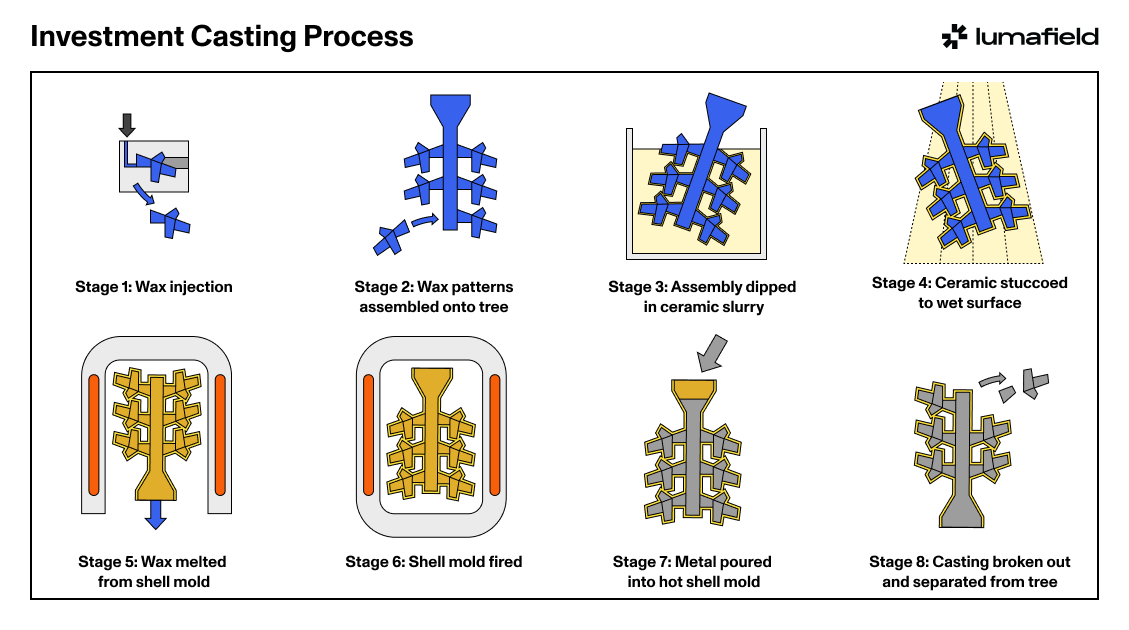
- Wax Injection: Wax is injected into a mold to create detailed replicas of the final part. These wax patterns form the basis for the mold structure.
- Wax Pattern Assembly: The individual wax patterns are attached to a central wax sprue, forming a tree-like structure. This assembly ensures multiple parts can be cast simultaneously.
- Dipping in Ceramic Slurry: The wax assembly is dipped into a liquid ceramic slurry to coat its surface, capturing every fine detail of the patterns.
- Ceramic Stucco Application: While the ceramic coating is still wet, the assembly is coated with fine ceramic particles (stucco) to build up the mold’s strength and heat resistance.
- Wax Removal: The ceramic-coated wax tree is placed in a heated environment, melting the wax and leaving behind a hollow ceramic mold.
- Firing the Mold: The ceramic mold is fired at high temperatures to harden it, ensuring it can withstand the molten metal during casting.
- Metal Pouring: Molten metal is poured into the preheated ceramic mold, filling the intricate cavities left by the wax patterns.
- Casting Removal: Once the metal cools and solidifies, the ceramic mold is broken away, and the individual castings are separated from the tree.
What is Sand Casting?
Sand Casting is the most flexible and economical casting method, using compacted sand to form molds. It’s ideal for large or simple parts that don’t require extreme precision. Sand casting is used for engine blocks, industrial pumps, and large machinery parts, offering affordability and scalability for heavy-duty components.
The Sand Casting Process
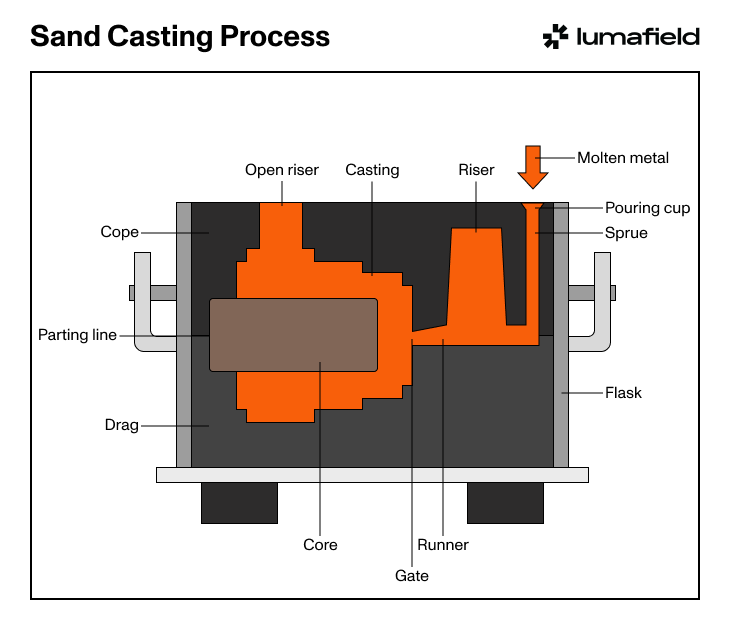
- Mold Preparation: A wooden or metal pattern is pressed into sand to create a cavity.
- Pouring: Molten metal is poured into the sand mold.
- Cooling and Breaking: Once cooled, the mold is broken to retrieve the part.
Design Considerations for Casting
When designing parts for casting, it’s important to consider the specific process being used and keep the following in mind:
- Material Selection: Aluminum and magnesium are commonly used for HPDC and LPDC, while investment casting works well with exotic alloys. Sand casting handles a broader range of materials, including cast iron.
- Complexity: Investment casting excels at fine details, HPDC offers tight tolerances, and sand casting is suited for simpler shapes.
- Surface Finish: HPDC and investment casting produce smooth finishes, while sand casting typically requires additional machining for finer details.
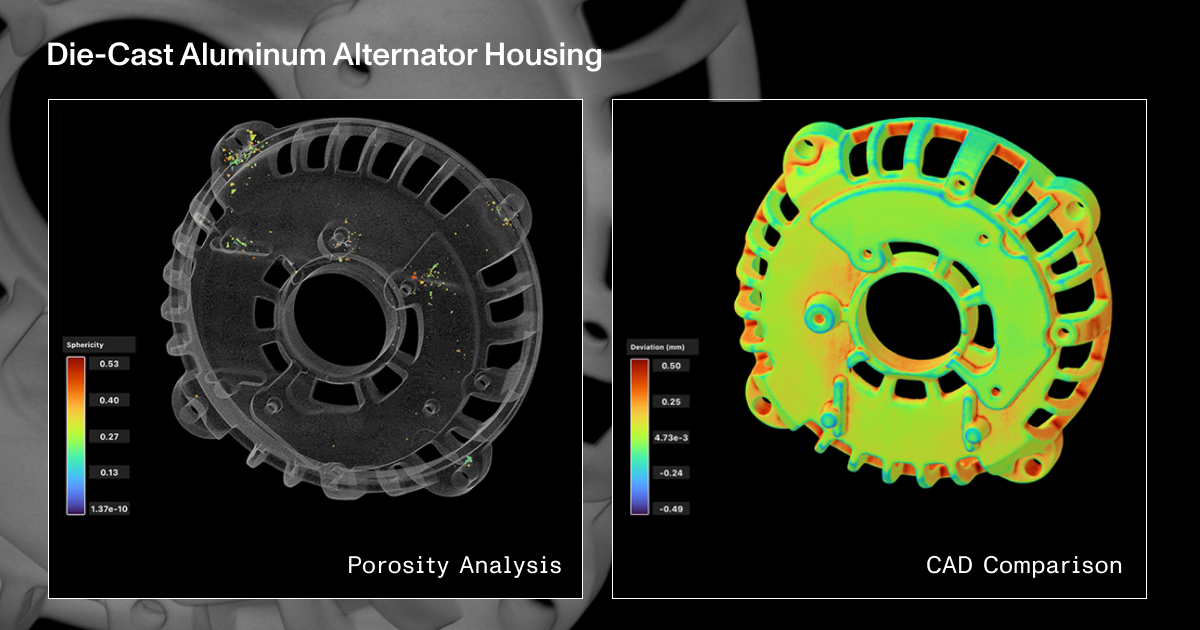
How to Ensure Casting Quality
Inspection is essential to identify casting defects like porosity, cracks, and dimensional inconsistencies. Traditional methods like dye penetrant testing or sectioning damage the part in question, while techniques like X-ray provide limited internal insights. Industrial CT scanning offers a non-destructive solution, delivering a complete 3D view of both internal and external structures. This allows manufacturers to detect hidden flaws, verify dimensional accuracy, and improve quality across all casting processes without damaging the part.
Industrial CT scanning is well-suited to addressing specific challenges unique to each casting method:
- High-Pressure Die Casting (HPDC): CT scans detect porosity and gas entrapment, common in high-speed injection processes, ensuring parts like engine housings meet strength and durability requirements. Scanning can also identify areas where the mold design causes uneven cooling or incomplete fills.
- Low-Pressure Die Casting (LPDC): CT helps evaluate defects like shrinkage cavities and air pockets that occur due to slower metal flow. It ensures uniform material density, especially in critical structural components like automotive wheels or suspension parts.
- Investment Casting: CT provides detailed analysis of thin-walled or intricate features, detecting potential defects like shell cracking or incomplete fills. It is particularly useful for verifying the integrity of aerospace turbine blades or medical implants, where fine detail and structural precision are essential.
- Sand Casting: CT scans reveal voids, cracks, or material inconsistencies often caused by mold shifting or insufficient compaction. Scanning also confirms dimensional accuracy for large, heavy-duty parts like engine blocks or industrial machinery.
By catching defects early, double-checking dimensional accuracy, and identifying root causes of failures, CT scanning ensures higher-quality cast products while reducing scrap and rework across all casting methods.
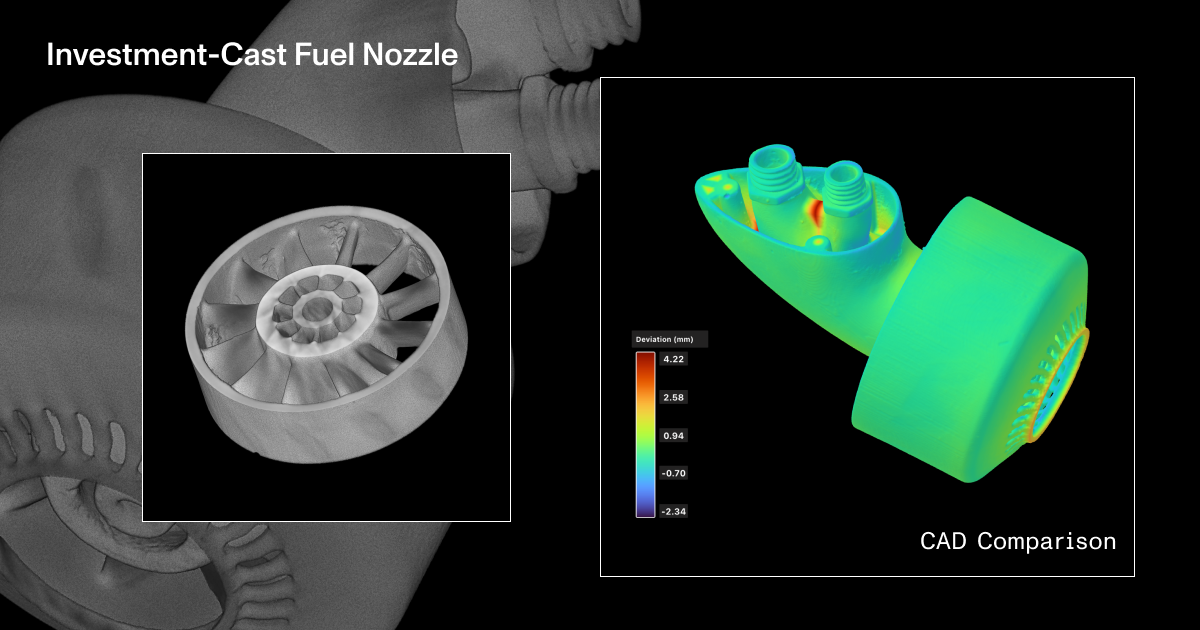
Conclusion
High-Pressure Die Casting, Low-Pressure Die Casting, Investment Casting, and Sand Casting each offer solutions tailored to specific needs—for everything from high-strength automotive parts to intricate aerospace components.
Industrial CT offers an accessible and affordable way to guarantee product integrity, as manufacturers optimize casting processes, reduce defects, and deliver reliable products that meet uncompromising standards. With cutting-edge inspection, even the most tried and true fabrication techniques can raise the bar on quality.