Solving Problems for the 21st Century
"The solutions to the 21st century’s biggest problems depend on manufacturing."
Solving Real Problems
In the coming decades we will see changes to the way we power our cities, the way we deliver medical care, the way we communicate, how we move from place to place, and countless other aspects of our lives. Revolutions in energy production, transportation, housing, communications, medical devices, and other important sectors all need one thing to make the leap from idea to reality: manufacturing.
The engineers of the 1960s who designed and built Apollo capsules, Boeing 737s, Corvette Stingrays, and Telstar would be amazed by the tools that modern engineers have at their disposal today. Computed Aided Design (CAD), physics simulation software, advances in materials science, and manufacturing techniques have all taken gigantic leaps forward in the past several decades. We are able to make safer, less expensive, more efficient, and better performing products thanks to these advances. All of these breakthroughs are vitally important to solving our biggest problems.
As engineering tools became more complex and sophisticated, so did the products that engineers designed and manufactured with them. Assemblies have gotten smaller and more complex, manufacturing processes have grown more and more automated, and the requirements for product quality have grown more and more rigorous. Yet while the tools for developing new products took great strides over the past half-century, the tools for understanding them have not.
Yesterday’s engineers used a pair of calipers and a bandsaw to understand the parts that they were manufacturing. Today, engineers all over the world are still sawing products in half to discover, understand, and diagnose manufacturing problems.
"The founding team at Lumafield has struggled with this lack of manufacturing insight tools for our entire careers."
We’ve created medical devices, 3D printers, commercial LED lighting systems, batteries for electric vehicles, consumer devices and more. Every time we brought a new supplier online or tried a new material or tried a new design technology, we always had to ask ourselves: is this part good? We were surprised to find that there is no single way to answer that seemingly simple question. That’s when we started thinking that there has got to be a better way to give engineers confidence when developing, introducing, and manufacturing products.
Lumafield was started after a dinner where we talked about these shared frustrations. We asked ourselves: what would the world look like if we didn’t have to break things in order to understand them? What if you could understand changes in your manufacturing lines over time? What would happen if every designer and manufacturer had the ability to see inside of the things they made and diagnose problems without wasted time, material, and effort? What if, by giving you a deeper understanding of your parts, we could truly close the loop between design and manufacturing?
Reimagining something as complex as manufacturing quality control would be an intimidating undertaking for a clean-sheet design. We didn’t have to do that at Lumafield because there’s already an amazing technology that makes it possible to see inside of anything, diagnose problems, and avoid destructive testing. That technology is called Computed Tomography (CT) scanning and it’s as close to magic as any engineering tool we’ve ever used.
There’s just one problem with CT scanning. To use it today, you'd need about one million dollars to get a system in your lab or you'll be sending your precious parts to a specialized lab, waiting days to get a multi-gigabyte delivery of images selected by a technician unfamiliar with your design. Not exactly the kind of tool that every engineer can use each day.
We started Lumafield to shine a new light on manufacturing and bring the missing dimension to product design and manufacturing. Before Lumafield, we were working on the next generation of design and fabrication technologies at places like Formlabs, Desktop Metal, and Autodesk. We saw firsthand the amazing things that engineers are capable of when you give them access to powerful but intuitive tools to supercharge their design processes.
"We built exactly what we set out to make with Neptune and Voyager."
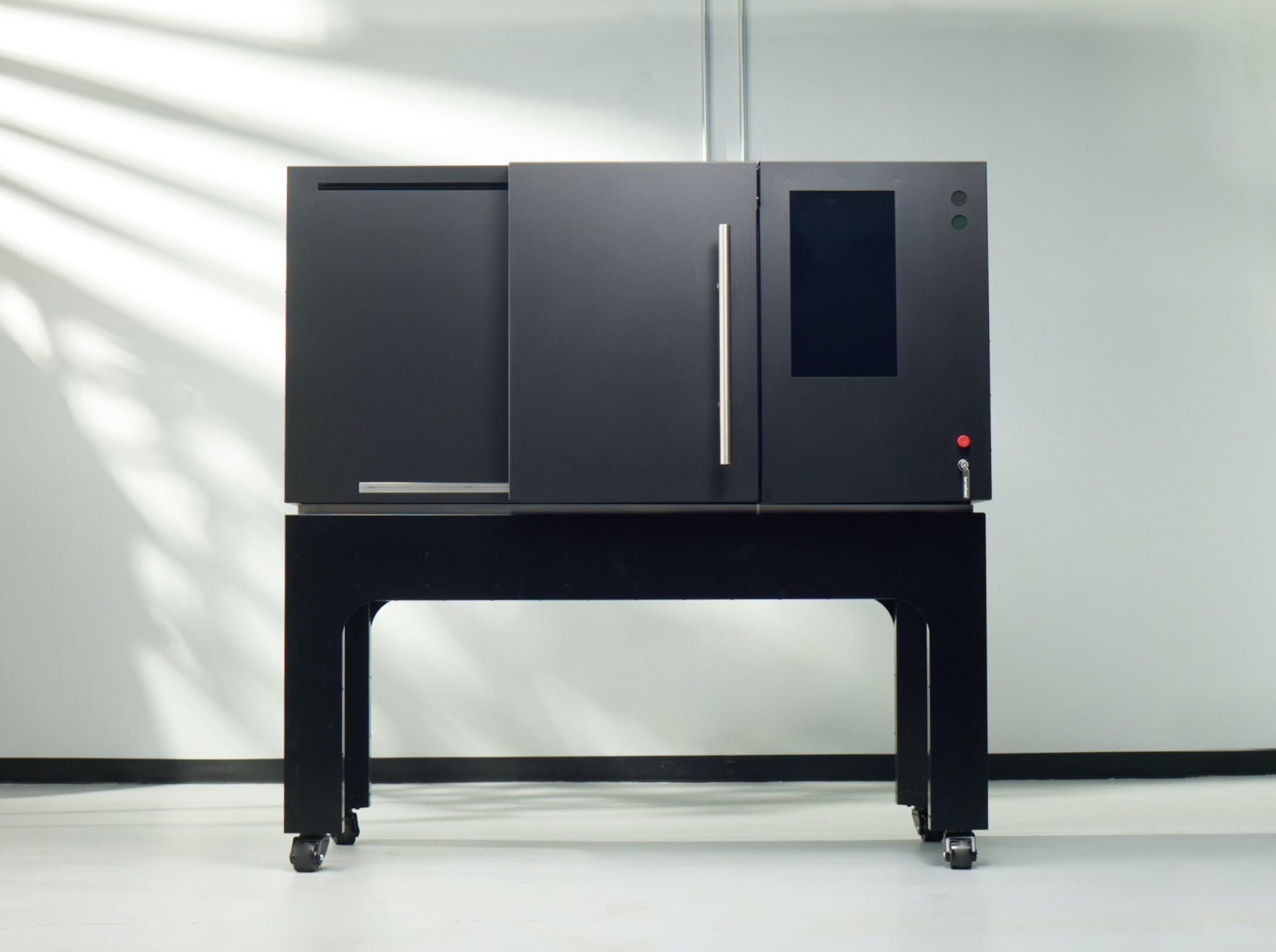
Neptune is the world’s first accessible CT scanner. We designed everything about Neptune to make it affordable, approachable, and intuitive so that every engineering team in the world can have one in their shop. Our team redesigned everything about CT scanning from first principles to achieve a combination of price and performance that has never existed with this technology before now. Neptune uses Artificial Intelligence to make it possible for anyone to run a CT scan without first becoming an expert in X-ray physics.
Neptune is powered by Voyager, our groundbreaking browser-based CT scan analysis software. Instead of requiring our customers to purchase expensive and difficult to use desktop software, we built Voyager to run in the browser so that it can be used on any computer, anywhere in the world. You can inspect, measure, slice, dice, and understand your parts however you want using Voyager’s intuitive and versatile interface. Share the discoveries you make with other people on your team, in your supply chain, or across your manufacturing ecosystem with real time comments directly on the scan.
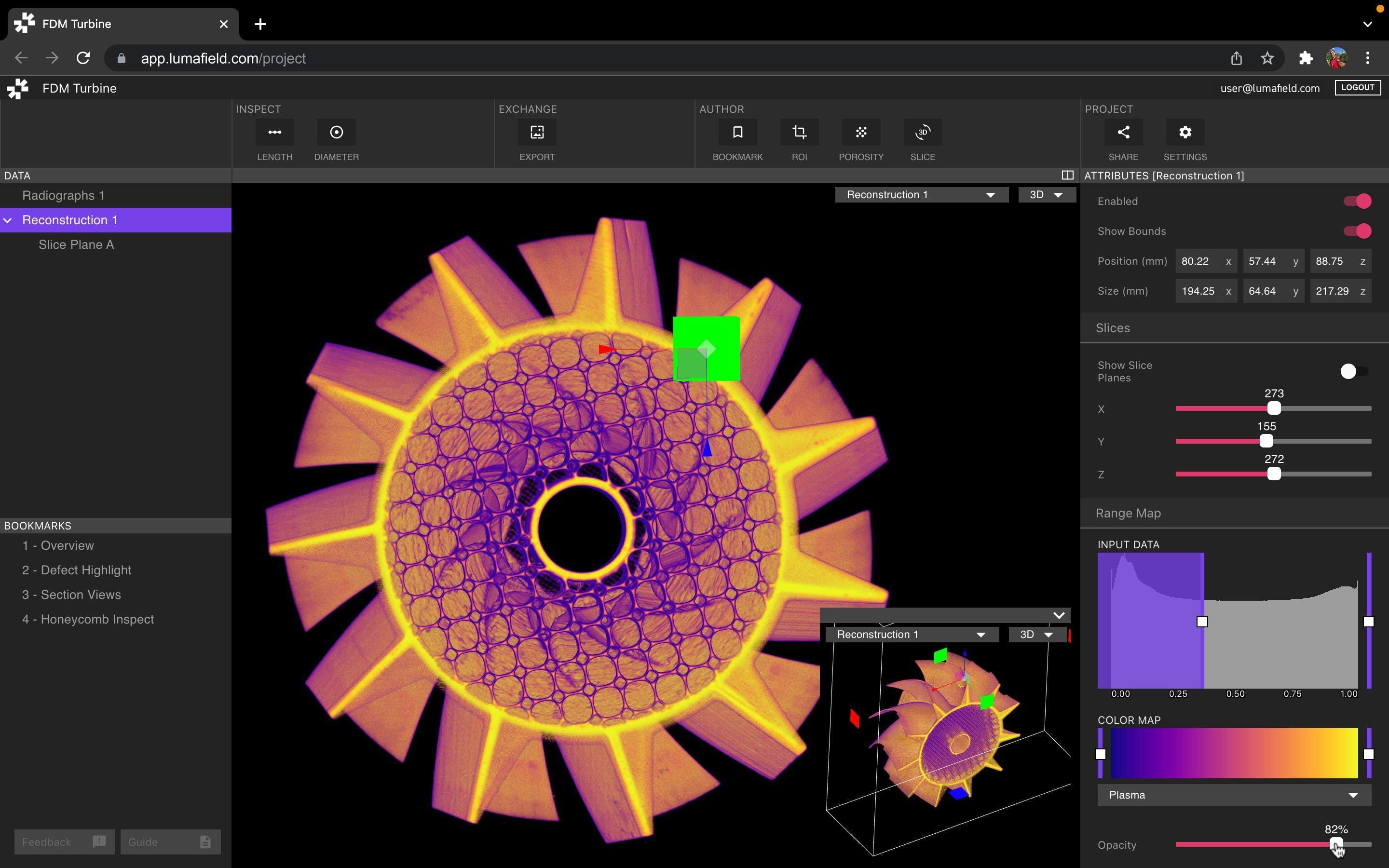
We’ve tried to stay under the radar as we’ve developed all of this amazing technology. We did so because we wanted to be able to focus on the hard parts of the challenge first. Our team has an allergic reaction to hype. We didn’t wait until we had built the first working scanner to announce our work—we waited until we had shipped multiple revisions of our products to dozens of paying customers. Our systems work and you can read more about how they are changing engineering for some of our customers over on our customer story page.
"Do you want to work at the intersection of humanity’s hardest problems, fundamental physics, hardware, and software?"
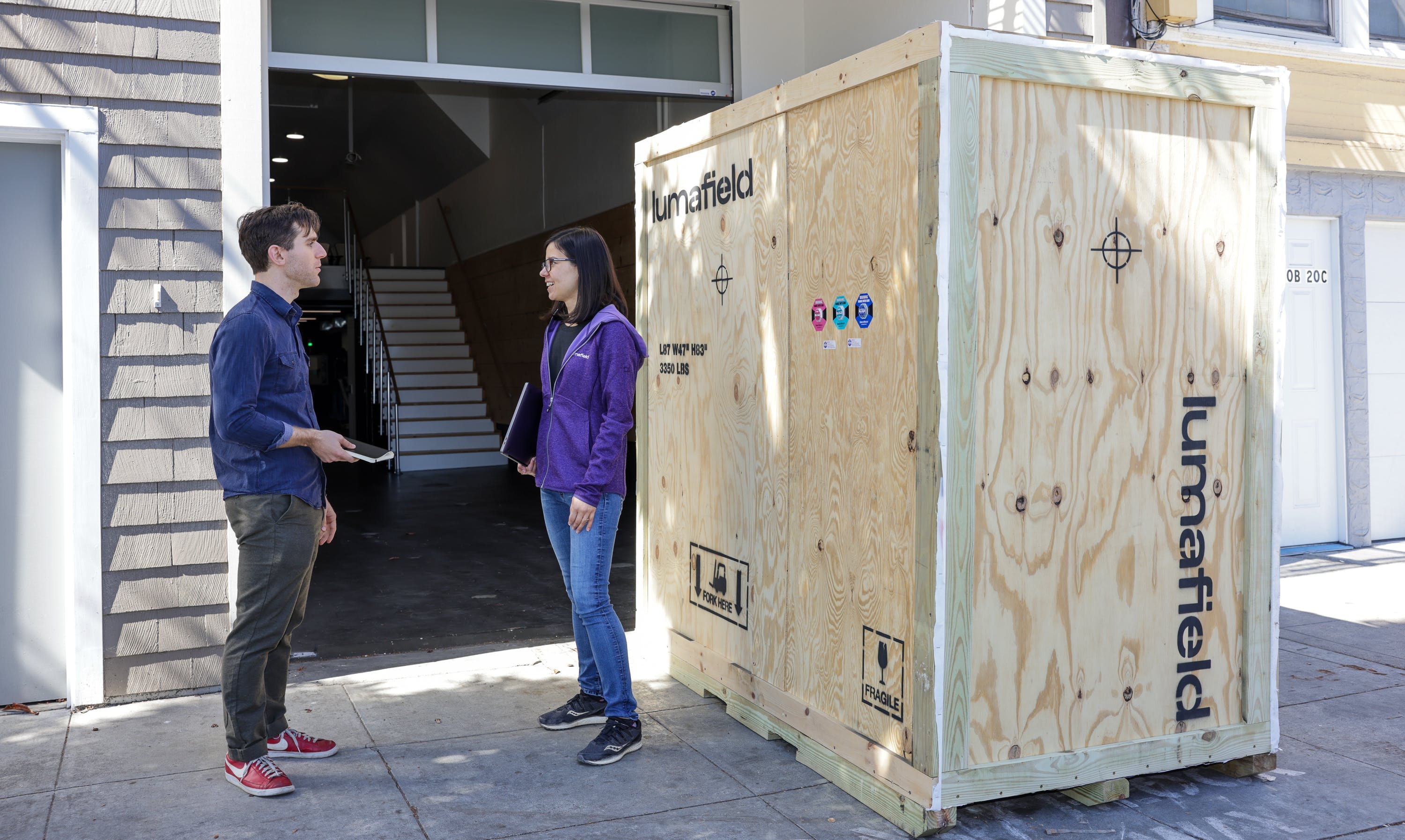
None of this would have been possible without the amazing team here at Lumafield. We are not ashamed to say that we have the best team in the world working on manufacturing insights. Our team includes PhDs from top universities, founders of successful hardware companies, alumni of some of the most valuable software companies in the world, and zero egos. Nothing is more exciting and rewarding than working hard on difficult and meaningful problems with incredible people.
Are you interested in what we're building? Get access to the technology by reserving a scanner now or join our team by visiting the careers page.
Even though we have covered a lot of ground already we are just getting started. We get out of bed each morning and fire up our computers because we want to transform the way that humanity solves manufacturing problems. Nothing excites us more than hearing about how our systems saved months of engineering time, helped a new process move through qualification with less waste, or empowered a company to bring a new technology to the world because of our work. The beautiful thing about building a tool is discovering all the ways it will be used in the hands of truly creative people.
The solutions to humanity’s hardest problems depend on manufacturing. Getting manufacturing right means solving those problems faster and more efficiently. Lumafield is here to make it possible for humanity to solve our hardest problems as quickly as possible.
More to come,
Andreas Bastian
Kevin Cedrone
Ric Fulop
Scott Johnston
Eduardo Torrealba