Heinz’s Sustainable Ketchup Cap
Heinz has taken a major step forward for sustainable packaging with the introduction of its first fully recyclable ketchup cap, made possible through a pioneering collaboration with Berry Global. Combining complex engineering with simple materials, Heinz’s achievement offers a model for manufacturers in consumer packaged goods (CPG) as well as food and agriculture at large to strive for waste reduction by designing more environmentally-friendly products.
Industrial CT is the perfect tool for exploring the intricacies of Heinz's new cap design without damaging it, even while it’s fully assembled and closed. Let’s take a look.
Mono-material construction
The old cap featured a silicone valve, which posed recycling challenges. The new cap's uniform composition of polypropylene (PP) simplifies recycling and can be accepted by any facility that processes plastic #5. Currently only about 3% of PP products are being recycled in the United States, but it is becoming more widely accepted. The new cap appears as a uniform color in Voyager’s range map, indicating that it’s entirely made of the same material. Compare it to the old cap, whose silicone valve is denser than the surrounding plastic.
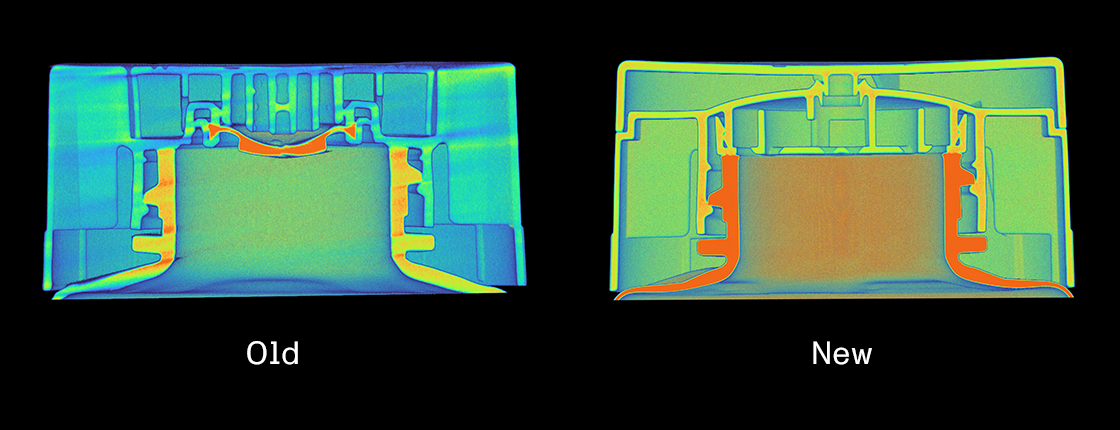
Innovative valve design
The new design leverages ketchup's shear-thinning property to dispense the perfect amount. Ketchup requires a specific amount of pressure to flow. When the bottle is squeezed, it moves through the outer channels where the wall separating them from the inner channels plays a crucial role. The wall prevents the ketchup from flowing back and directs it toward the antechamber, building the necessary pressure for the ketchup to pass through the nozzle efficiently.
Once the squeezing stops, the ketchup's viscosity increases, preventing drips and mess. This design ensures a clean and controlled dispense of the product.
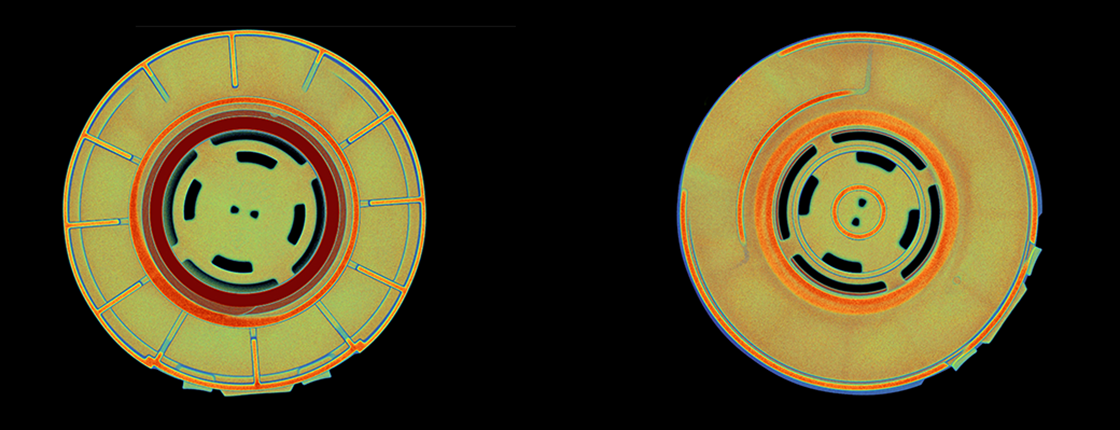
Industrial CT and sustainability
Developing sustainable packaging can present a significant engineering challenge. Recyclable plastics often don’t perform as well as their non-recyclable counterparts, and reducing material usage can mean that safety factors are reduced as well. Effective, sustainable packaging requires careful design and lots of fine tuning.
Industrial CT plays a pivotal role in the development of sustainable packaging, offering a non-invasive method to analyze, refine, and perfect packaging solutions. By reducing the need for physical prototypes, CT scanning accelerates the development process, cuts down on waste, and helps avoid the costs associated with scrapped prototypes and recalled products. It embodies the convergence of innovation and sustainability, offering a blueprint for the packaging industry's next steps.
Advanced Surface Capture technology can help manufacturers tell the whole story of their sustainability efforts by visualizing areas that are otherwise impossible to capture—those hidden by overhangs as well as shiny and reflective surfaces.
Heinz's recyclable cap is more than just an innovation; it's a statement of intent, reflecting a broader commitment to environmental sustainability. The cap's successful redesign, fueled by a $1.2 million investment and extensive testing, demonstrates the potential for significant waste reduction—up to 300 million plastic caps annually—and a future where packaging is fully recyclable, reusable, or compostable.
Learn more
Download our free white paper Removing Obstacles to Sustainable Packaging and discover how industrial x-ray CT can help packaging engineers create solutions that work.