Introducing Triton: production-ready CT inspection
Industrial CT offers the best insight into your parts, and with Triton, CT is now production-ready with rapid, automated, and high-volume scanning that’s at home in your factory. Quickly inspect and validate manufacturing parameters, find porosity, inspect dimensions, and analyze every part on your line in real time, without human labor.
Engineers and product designers use Neptunes in the lab and next to the line to identify problems and build production solutions. With Triton, you can now scale solutions developed on Neptunes in the lab directly into production using Lumafield’s Voyager platform. This means more scans faster than ever, with automated decision-making that embeds quality assurance directly in your manufacturing process.
Triton operates autonomously, minimizing human involvement to give engineers more time to develop their next products. Triton’s lights-out operation eliminates labor costs and boosts throughput by 4x compared to a manually-operated Neptune. With scan times under one minute and real-time intelligent analysis, Triton uses AI and custom recipes to identify out-of-spec parts and make immediate go/no-go decisions. As it works, it also generates rich data that helps you spot trends and improve your processes.
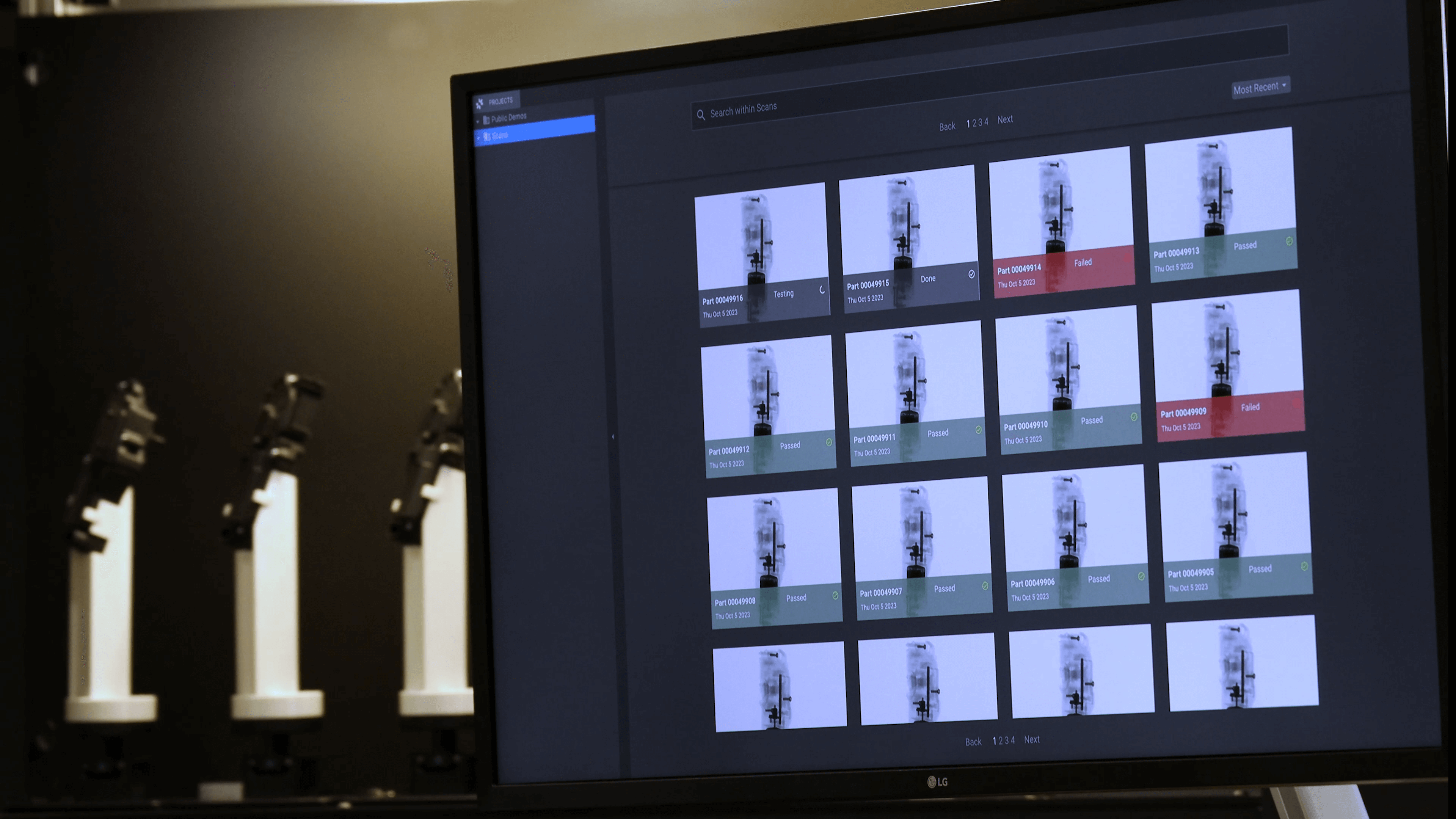
Triton’s automated part handling system is ready to integrate with factory automation systems in any industry. On packaging lines, Triton can conduct meticulous batch thickness and dimensional checks, ensuring every product meets quality criteria. For automotive assemblies, Triton validates component alignment and electrical connections in seconds. In battery production, Triton measures anode overhang distances to help ensure peak performance and reduce the risk of recalls. In consumer packaged goods (CPG), Triton conducts exhaustive 100% inspections, detecting internal porosity and cracks that evade human scrutiny.
Triton isn't just a tool; it's an ally in data-driven decision-making, enabling rapid responses at lightning speed. From the battery market to aerospace, Triton empowers manufacturers to seamlessly scale production while taking quality assurance to a new level.