Inspecting SLS 3D printed parts with industrial CT
Introduction to SLS
Selective laser sintering (SLS) is a 3D printing process that builds strong, functional parts out of plastic powder. SLS printers distribute a thin layer of powder (usually Nylon) across the build volume, melt specific areas with a laser, spread another layer above, and repeat the process until the model is complete.
SLS is ideal for production-scale additive manufacturing. Parts are supported by unfused powder during printing, so they don't require support structures and many parts can be stacked into a single build volume. And because Nylon is a familiar, high-performance thermoplastic, engineers are able to substitute SLS prints for conventional parts with a relatively high degree of confidence.
However, SLS can introduce flaws that make parts unsuitable. Industrial X-ray CT scanners can quickly find these issues.
Explore this scan in Voyager by creating a free account.
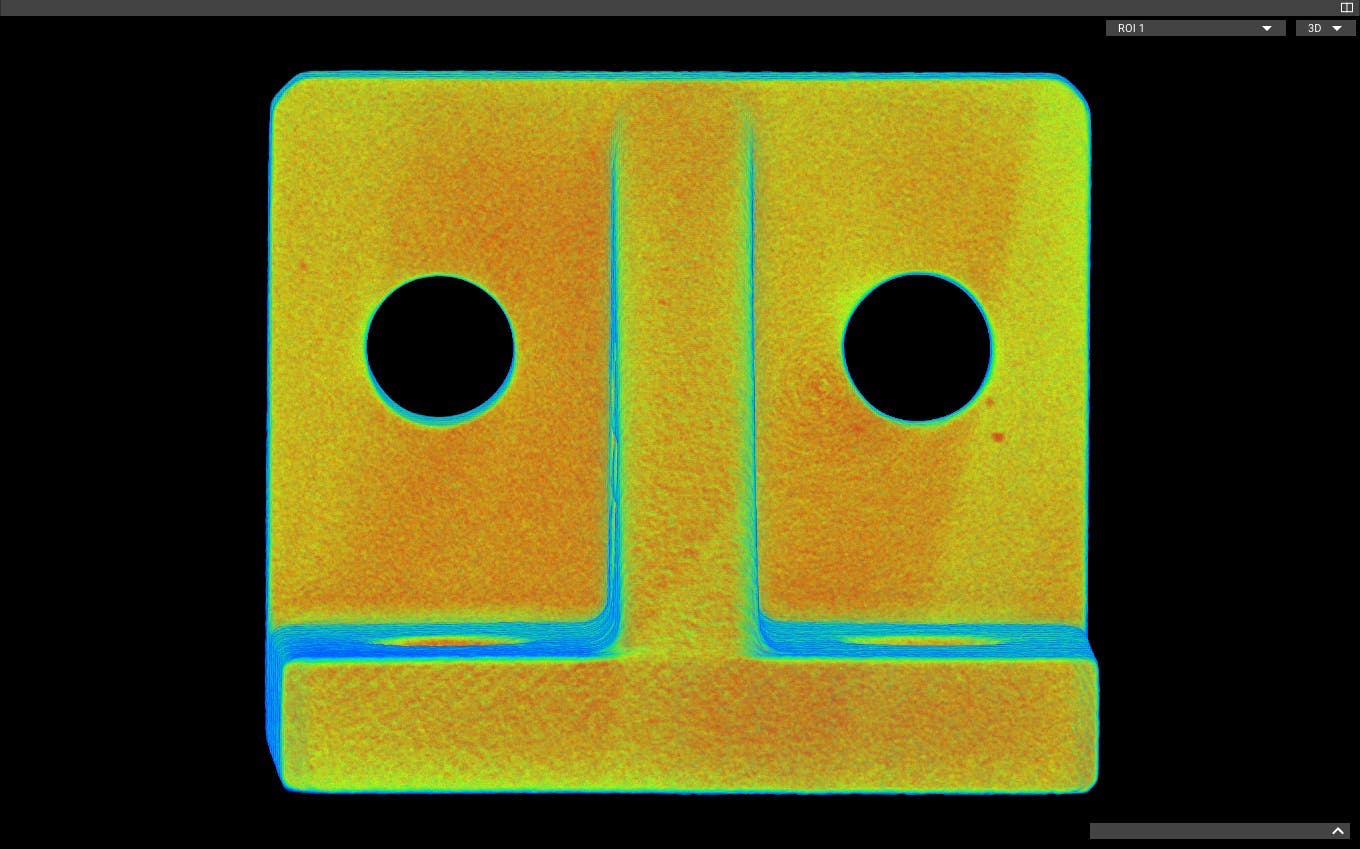
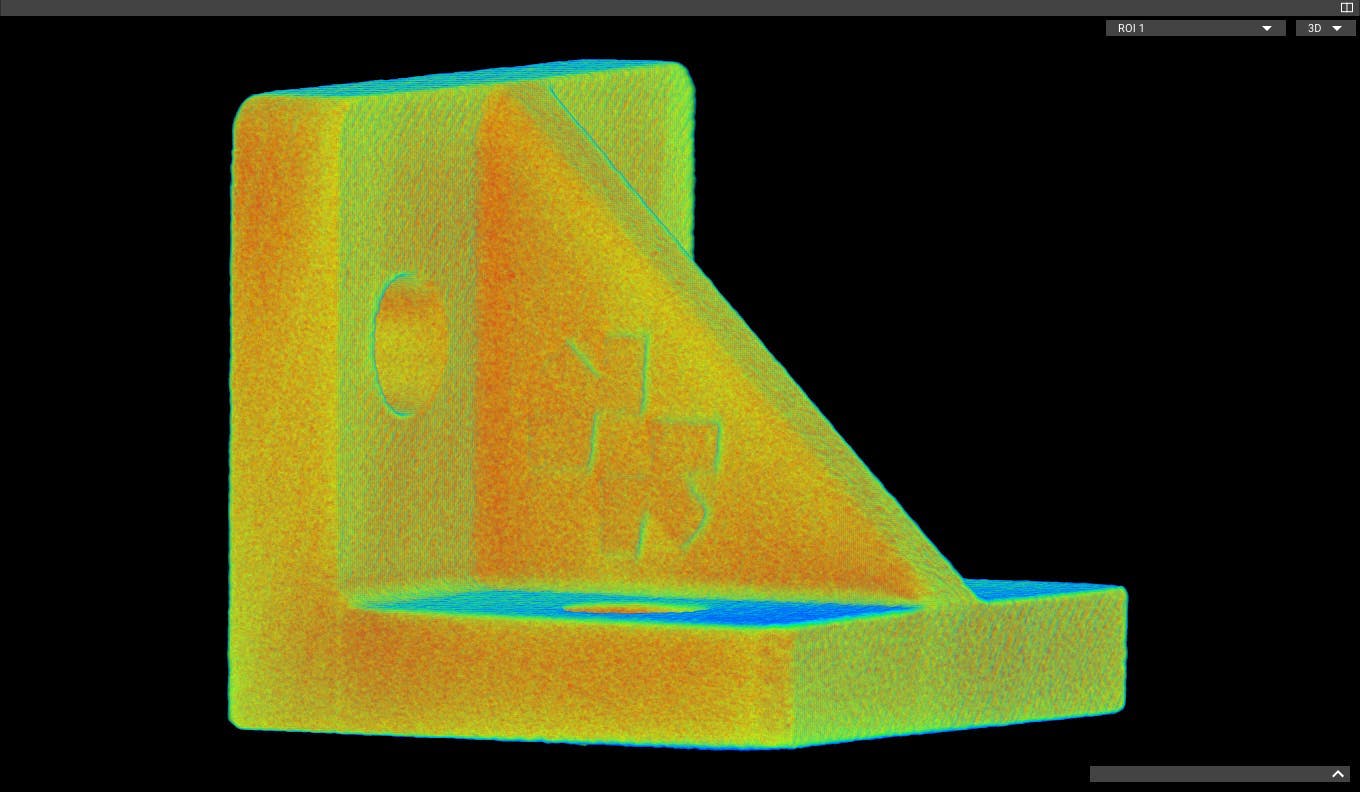
Uneven sintering
SLS printers build parts by sintering Nylon powder layer-by-layer. Errors in this process can result in unsolidified areas of the part that may be invisible, leading to unexpected part failure.
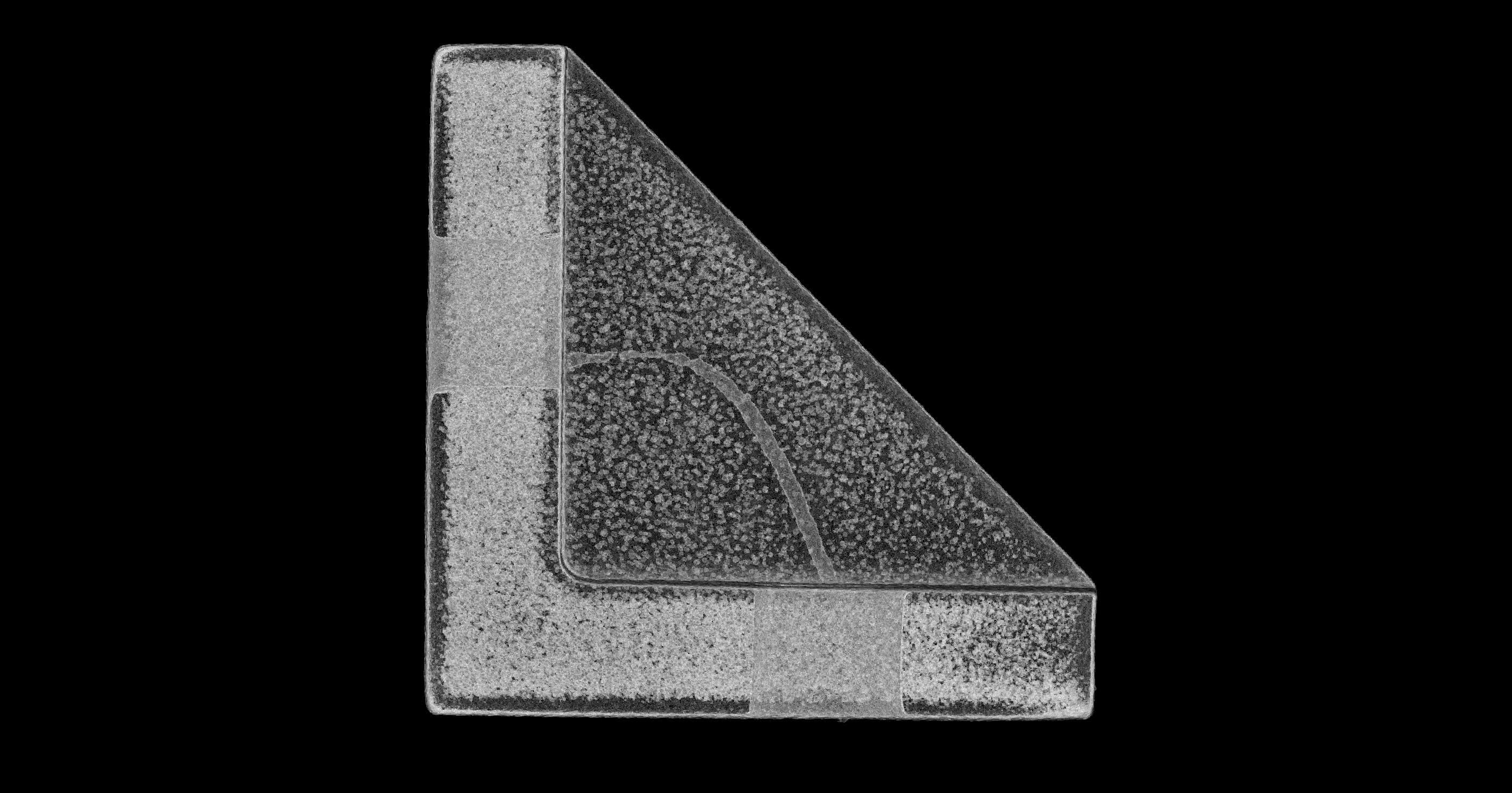
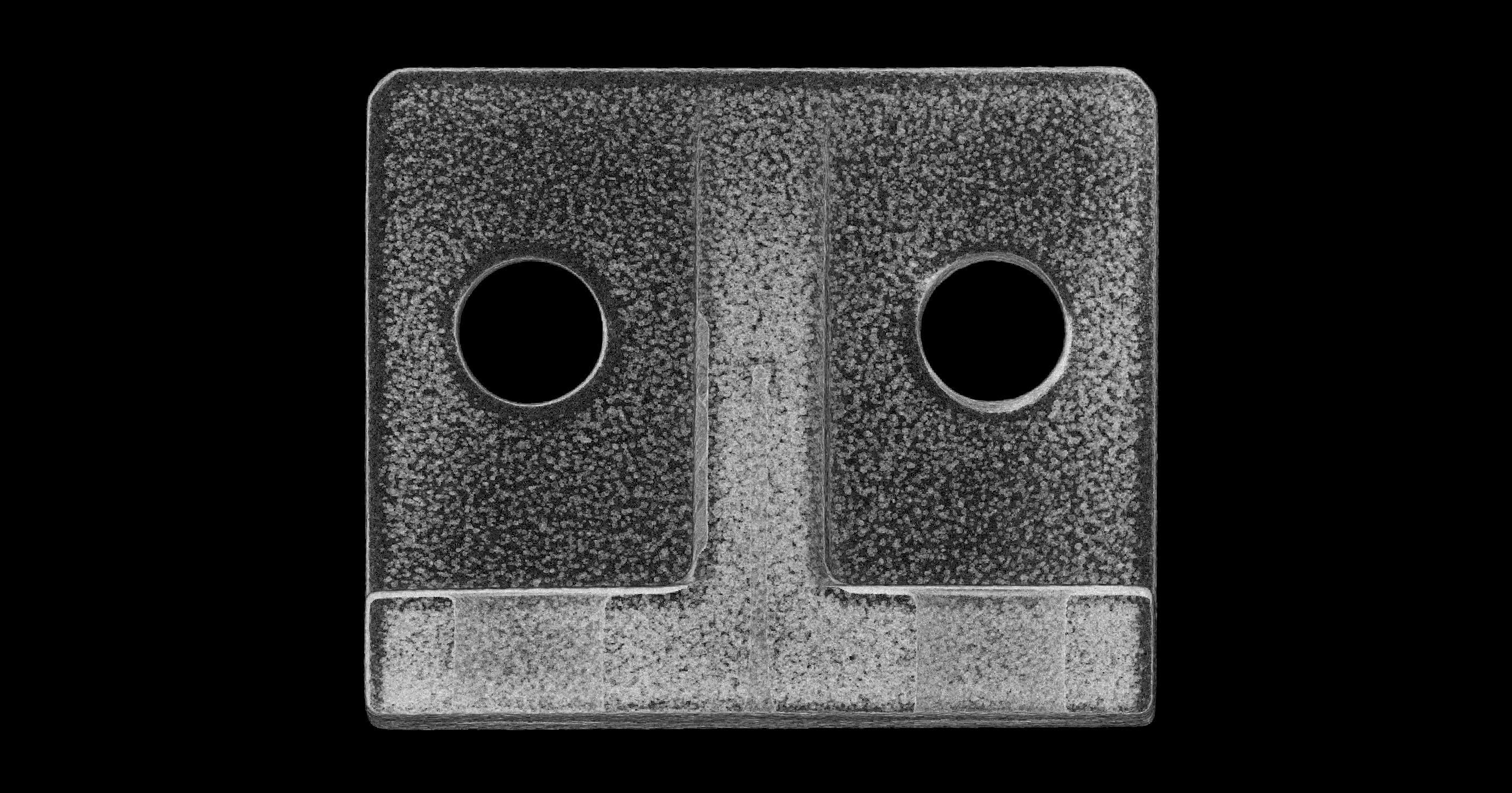
Dimensional accuracy
Accuracy and resolution are key considerations in additive manufacturing, and fine interior features are especially difficult to print accurately. In this part, a 1 mm channel starts close to nominal at the surface, but inside the part it narrows to 0.25 mm. Internal problems like this are indetectable with visual inspections, making industrial CT an important companion technology to 3D printing.
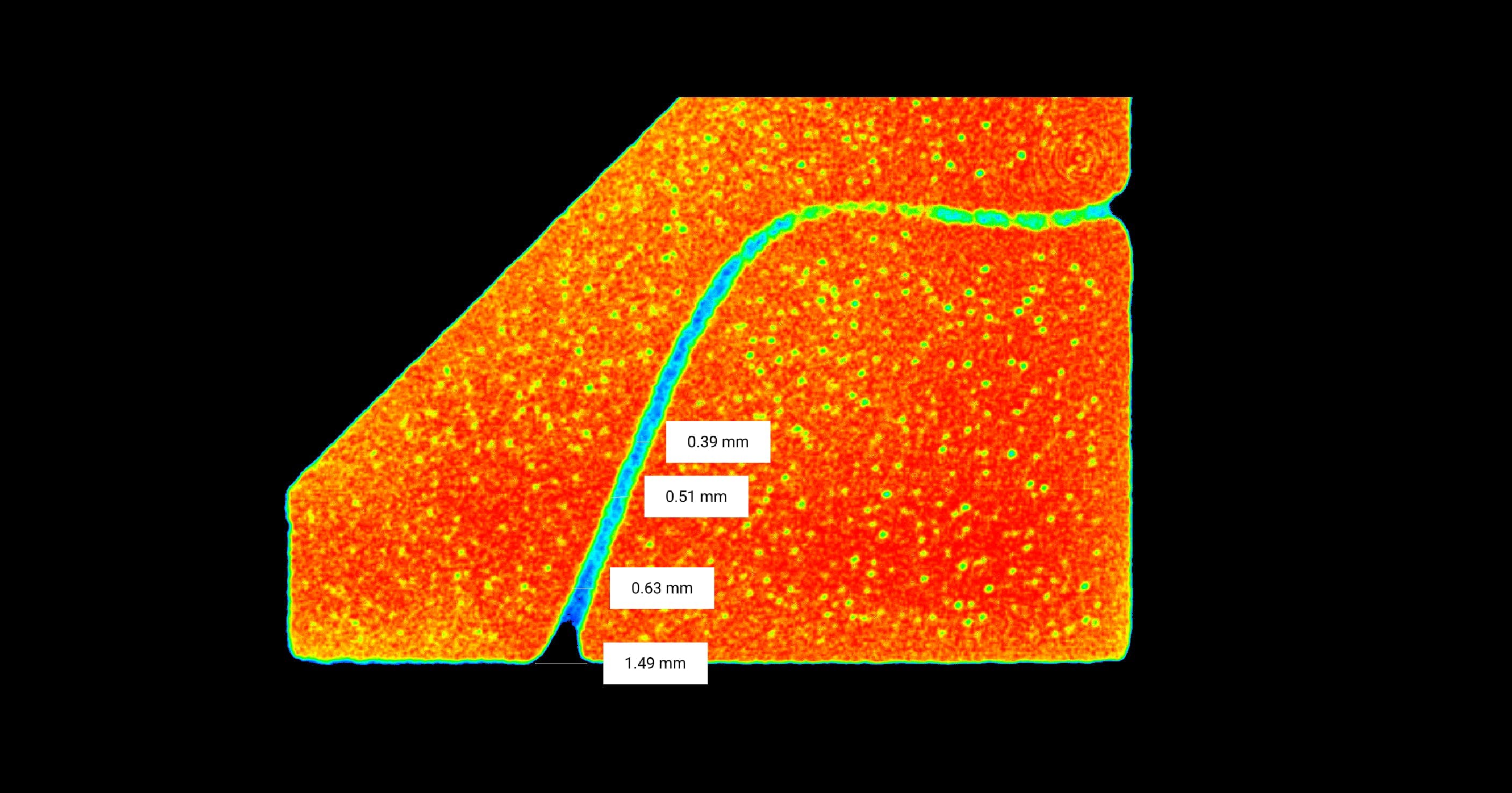
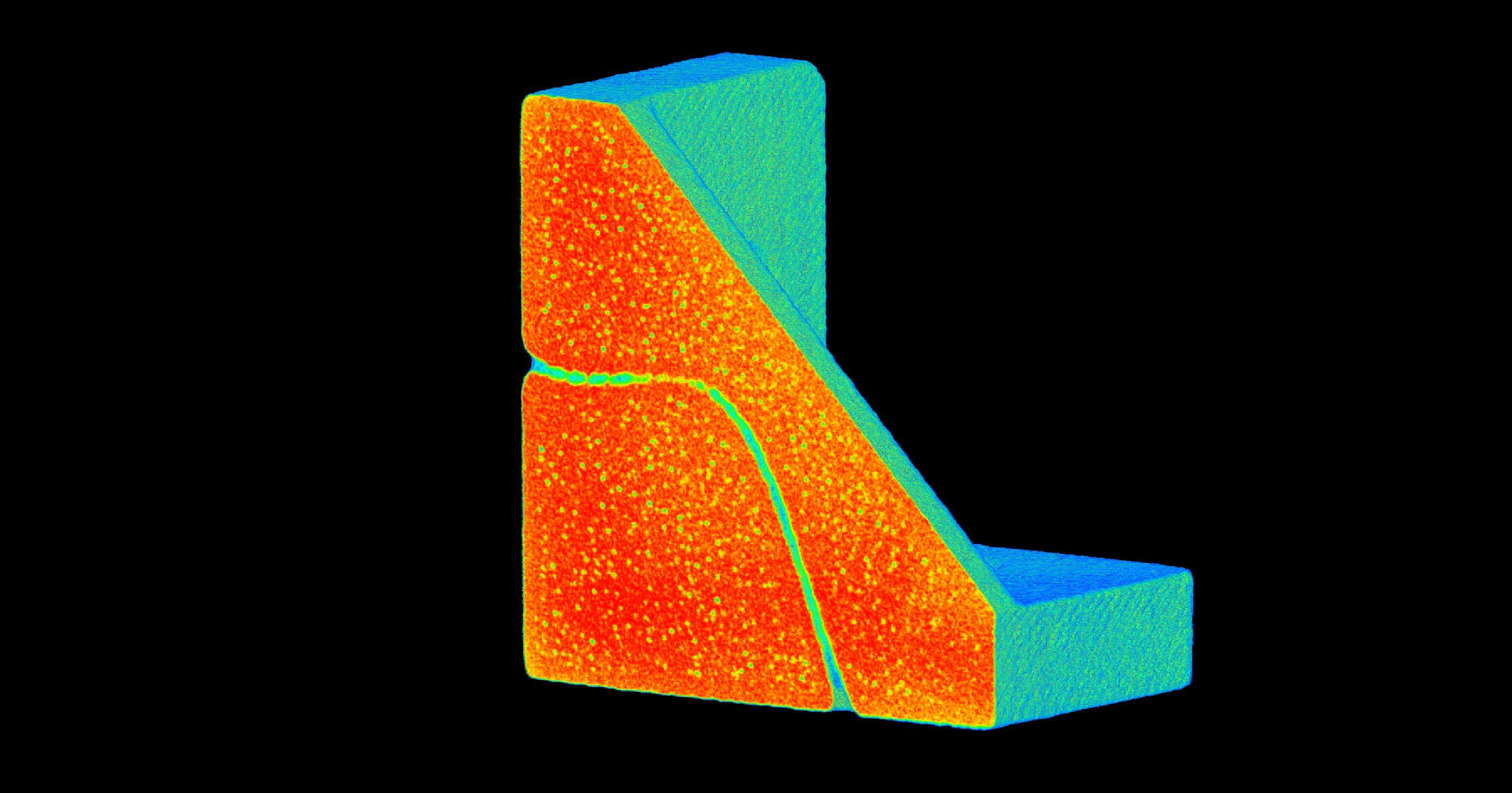
Trapped powder
An important advantage of 3D printing is the ability to form complex internal features that can't be molded or machined, like microfluidic channels. However, these internal features require careful post-processing, often including significant manual work, to clear trapped powder. Incomplete post-processing may lead to functional failure.
Here, a CT scan reveals unfused powder blocking an internal channel. In a production environment, this print would need to be returned for additional post-processing or scrapped altogether.
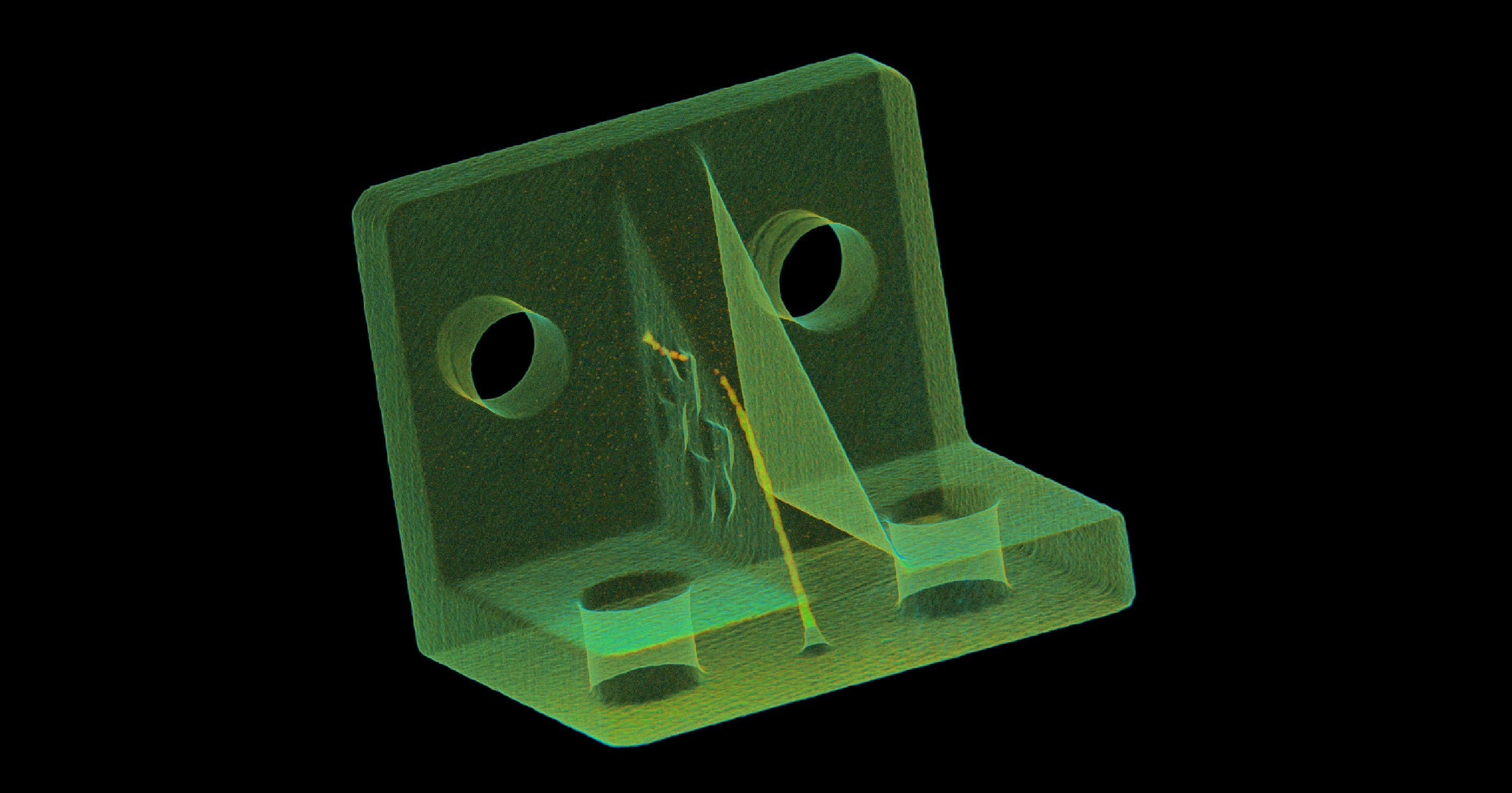
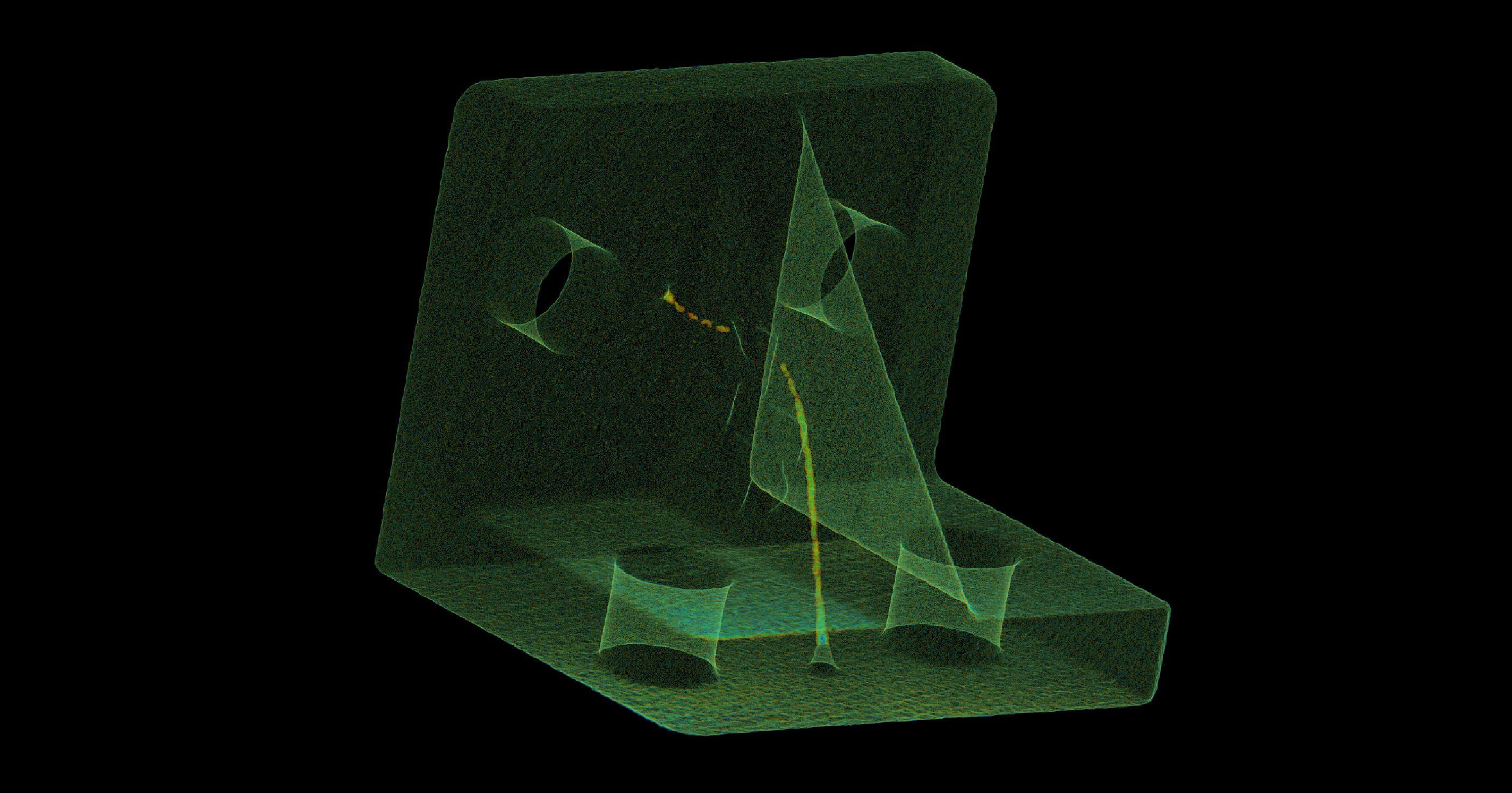