Reverse Engineering with Industrial CT
Regain control of your manufacturing
In the competitive landscape of modern manufacturing, the ability to quickly and accurately replicate existing parts is crucial. Whether you’re reshoring manufacturing to regain control over production, recovering lost design files, or optimizing product development, reverse engineering plays a vital role. Lumafield’s Neptune industrial Computed Tomography (CT) scanner and Voyager analysis software provide a new foundation for this crucial process, providing detailed, high-resolution data that minimizes labor and simplifies workflows.
Seamless mesh workflow
Traditional reverse engineering workflows utilizing surface scanners require extensive data stitching and mesh healing, consuming valuable time and resources. Industrial CT eliminates these steps by delivering a comprehensive view in a single scan, ensuring that every detail is captured accurately. Once you’ve identified your geometry of interest, Voyager makes it easy to export a mesh representation of your part. This model can be 3D printed directly, or imported into any CAD platform for use as reference geometry.
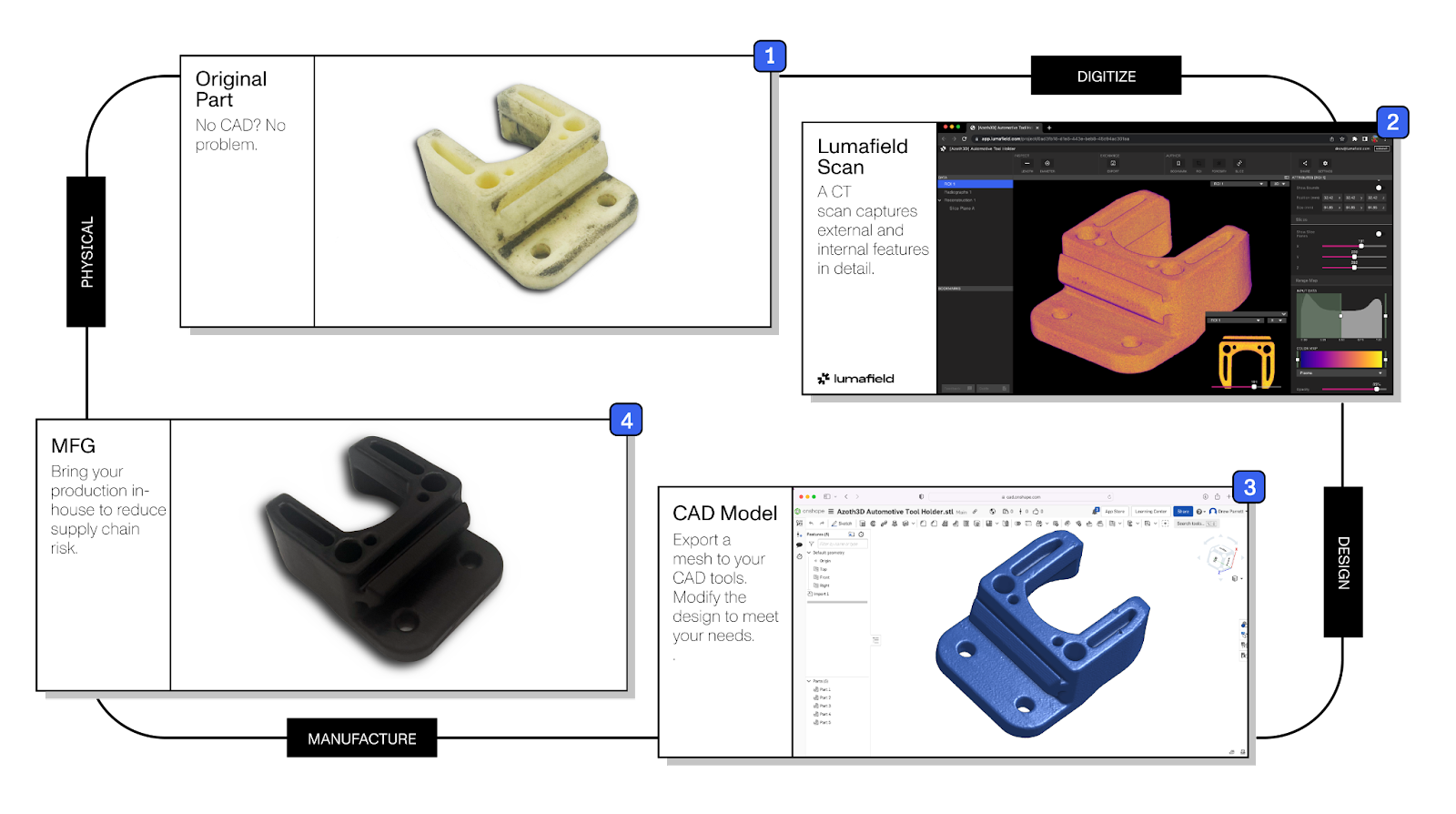
For more complex geometries, Lumafield’s workflow enables quick generation of STEP files, even for parts with intricate details. This is particularly useful for incorporating manufacturing defects into Finite Element Analysis (FEA) or rapidly moving placeholders into CAD. The high-resolution meshes provided by Lumafield ensure no details are missed, enhancing the accuracy and efficiency of your reverse engineering projects. These capabilities in Voyager also power CAD Comparison and Scan-to-Scan Comparison, allowing you to overlay meshes and calculate deviation.
Stay one step ahead
The implications of these advancements are significant. For instance, reshoring manufacturing efforts benefit from the ability to reproduce parts locally without relying on overseas suppliers. This not only reduces lead times but also enhances quality control and intellectual property security. Similarly, recovering lost design files becomes a seamless task, as detailed scans provide all the necessary data to recreate original specifications.
Pursuing your reverse engineering workflows with the support of Lumafield’s industrial CT scanning and analysis platform not only streamlines workflows but also enables manufacturers to stay ahead in a rapidly evolving market. By leveraging these tools, companies can enhance their product development cycles, improve quality control, and drive innovation efficiently.
For more detailed guidance on how Lumafield can enhance your reverse engineering workflows, visit our support article.