Webinar: Advanced battery inspection with industrial X-ray CT
On-demand webinar
Industrial CT offers engineers a powerful tool to diagnose problems and discover hidden flaws in batteries. This webinar hosted by Battery Technology and Lumafield delves into applications in battery construction, manufacturing, and inspection to ease detection and inspection for many critical issues. These include internal short circuits; cell swelling and deformation; delamination; electrode damage; contamination and inclusions; and electrolyte leakage.
Join Lumafield's Andreas Bastian and learn:
- How to quickly spot lithium-ion layer issues that can cause catastrophic failures
- How to measure internal battery features without cutting batteries open
- How industrial CT scanners work
- How companies can inexpensively adopt industrial CT in product development and manufacturing workflows
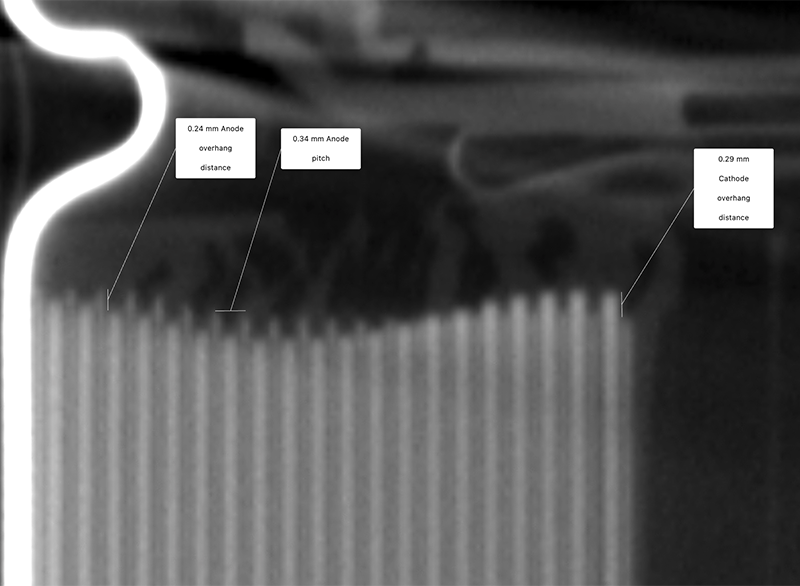
Industrial X-ray CT, akin to medical CT technology, captures a series of 2D X-ray images from various angles to reconstruct intricate 3D objects. X-ray CT reconstruction, a puzzle-like process, assembles these images into comprehensive 3D representations, opening up new avenues for analysis.
In battery engineering, CT has emerged as an indispensable tool for inspection and analysis. Destructive testing on batteries is not only dangerous; it also destroys vital evidence needed to understand failure causes. This makes CT the ideal inspection method to ensure both battery safety and performance.

CT allows engineers to address a wide range of the most common and consequential battery defects, including those that elude all other means of detection. It facilitates the identification of foreign debris within battery cells, a common culprit for reduced capacity and operational hazards. CT lets you assess the condition of electrode and current collector components, revealing any folds, tears, or wrinkles they may have. The ability to measure anode overhang distance and alignment also provides critical insights into battery quality and function.
The integrity of tab welds, which ensures optimal energy transfer, can be characterized with exceptional precision using CT scans. Deflected anodes prove to be a major problem for batteries, but with CT, engineers can pinpoint and correct misalignments that could potentially lead to uneven energy transfer or premature battery failure.

Delving deeper, CT scans offer comprehensive characterizations of anode and cathode materials, their dispersion, and structural integrity. With these insights, engineers can enhance the uniformity and effectiveness of battery components, ultimately boosting cell reliability and lifespan. As an all-encompassing inspection tool, CT empowers battery engineers to scrutinize and enhance battery quality, without compromising safety or performance.
For more, explore our earlier batteries webinarinspired by our Scan of the Month from October 2022.
About the presenter
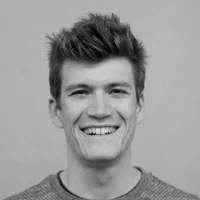
Andreas Bastian is co-founder and Head of Product at Lumafield. Prior to Lumafield, he led research in machine learning for engineering for aerospace and product design at Autodesk. In collaboration with NASA JPL, he developed generative design for space applications.