Inspecting an MJF 3D printed part with a CT scanner
Introduction to MJF
Multi-Jet Fusion (MJF) is a 3D printing process developed by HP that uses inkjet heads to selectively apply a fusing agent to plastic powder. MJF parts resemble SLS prints, and the process has become popular because it produces strong, functional parts at high volume with cost-effective operation.
Like all 3D printing processes, MJF requires specialized design knowledge and careful post-processing to achieve optimal results. An industrial CT scanner can quickly pinpoint invisible problems that can lead to part failure.
Explore this scan in Voyager by creating a free account.
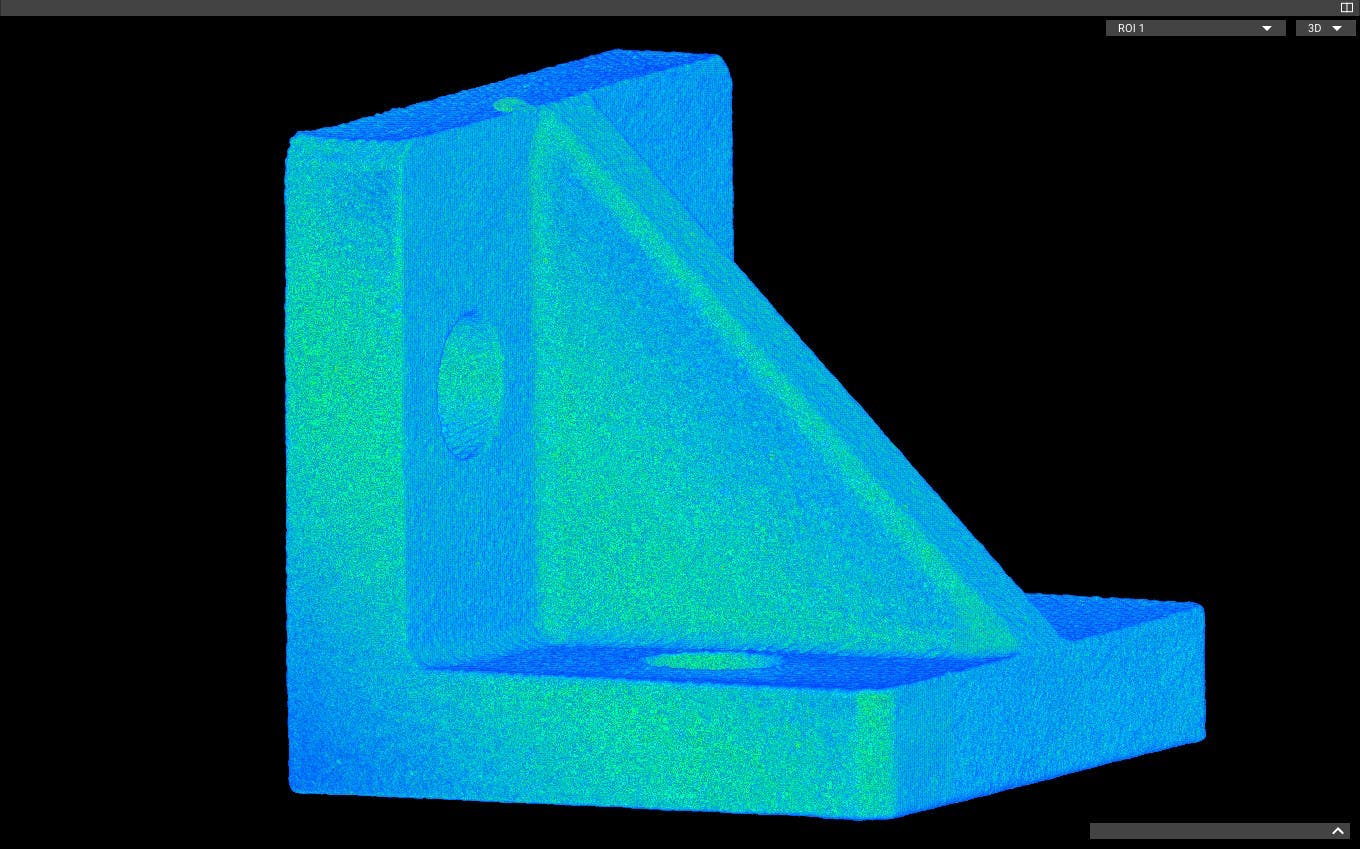
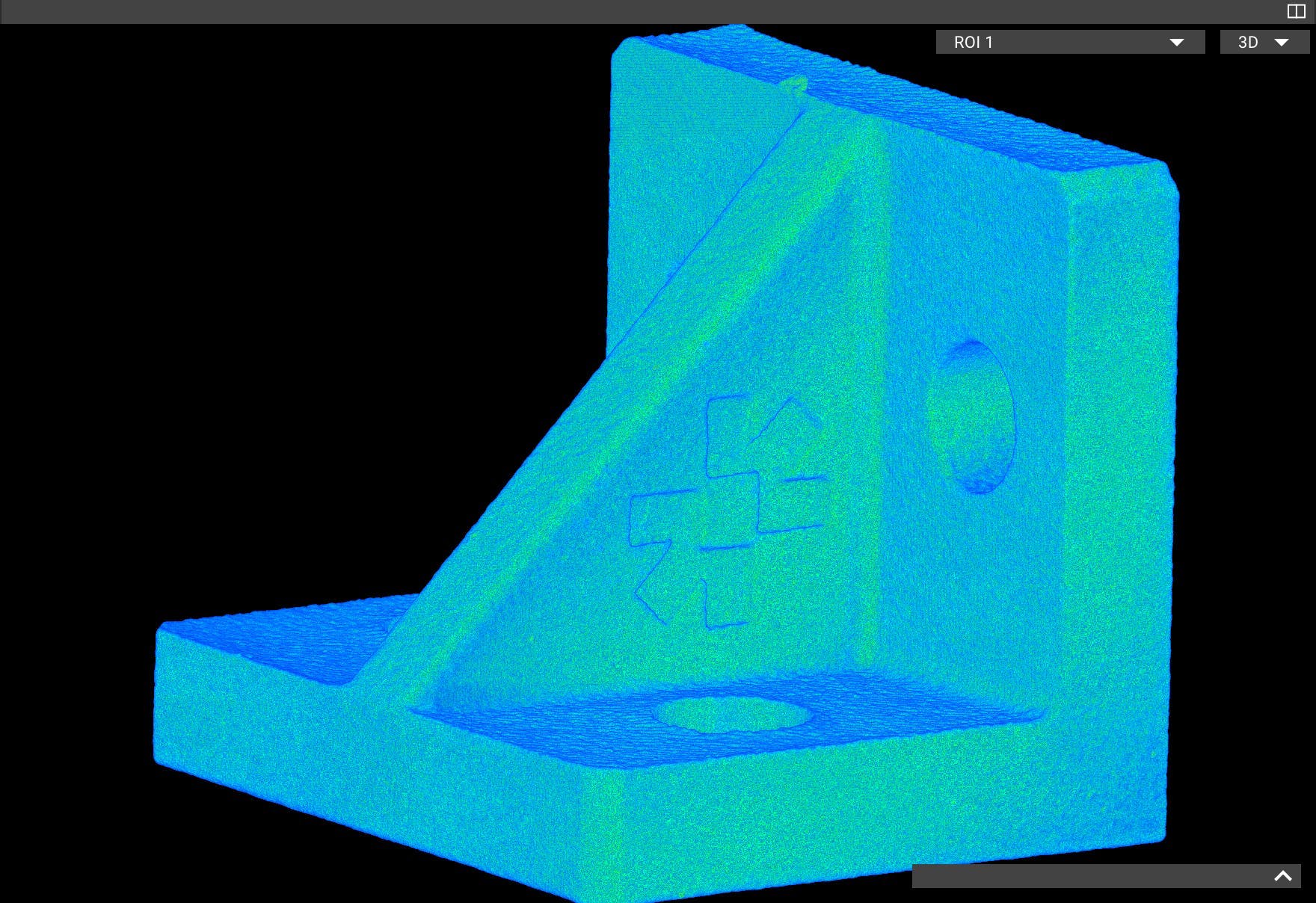
Trapped powder
Internal features can trap unfused powder, requiring design revisions or painstaking manual post-processing. This trapped powder is outwardly invisible, but easy to find with a CT scanner.
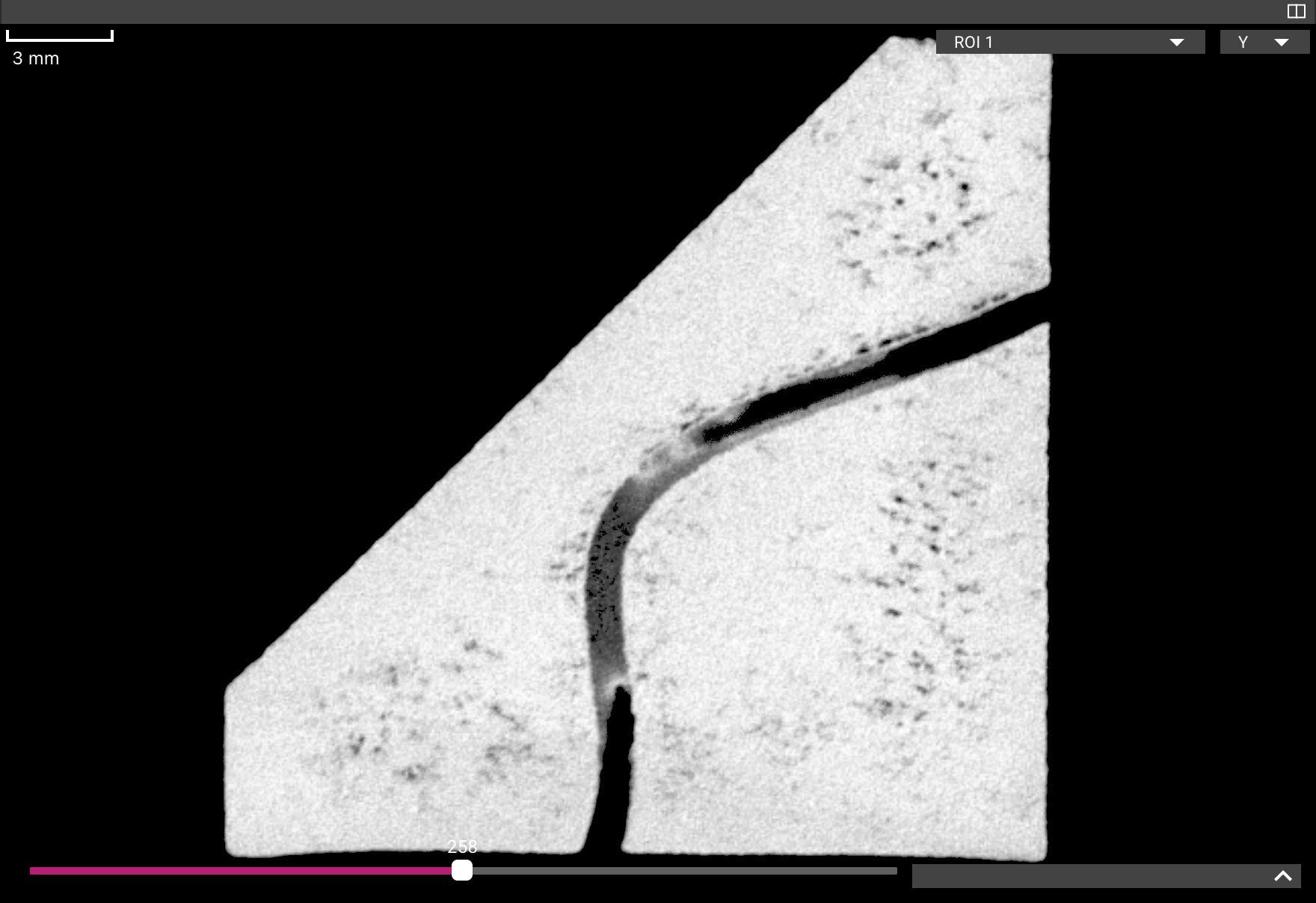
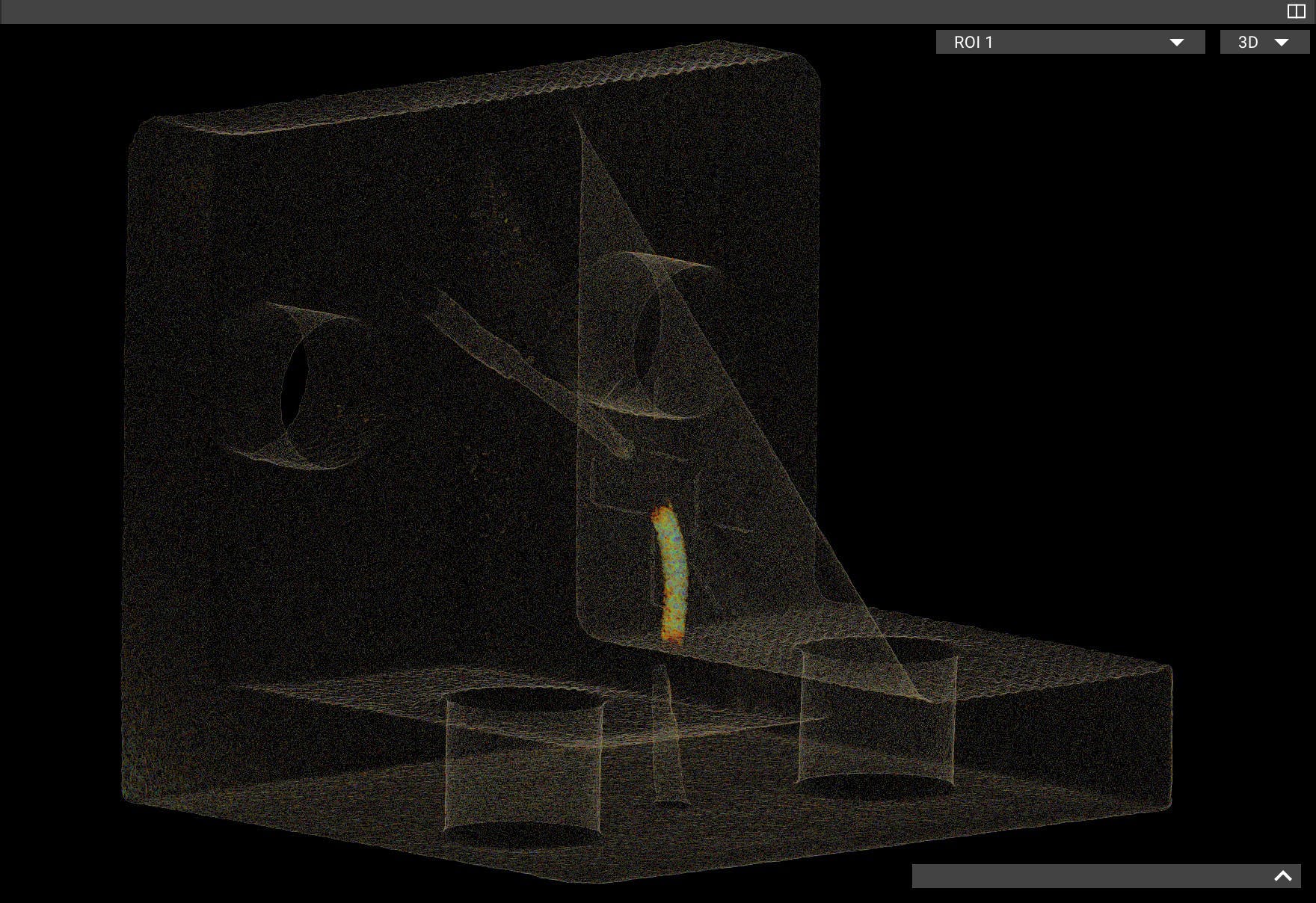
Surface quality
The MJF process offers excellent thermal control during printing, resulting in parts with low porosity and good surface finish. Here our CT scan shows a generally high-quality surface finish with a slight uniform roughness.
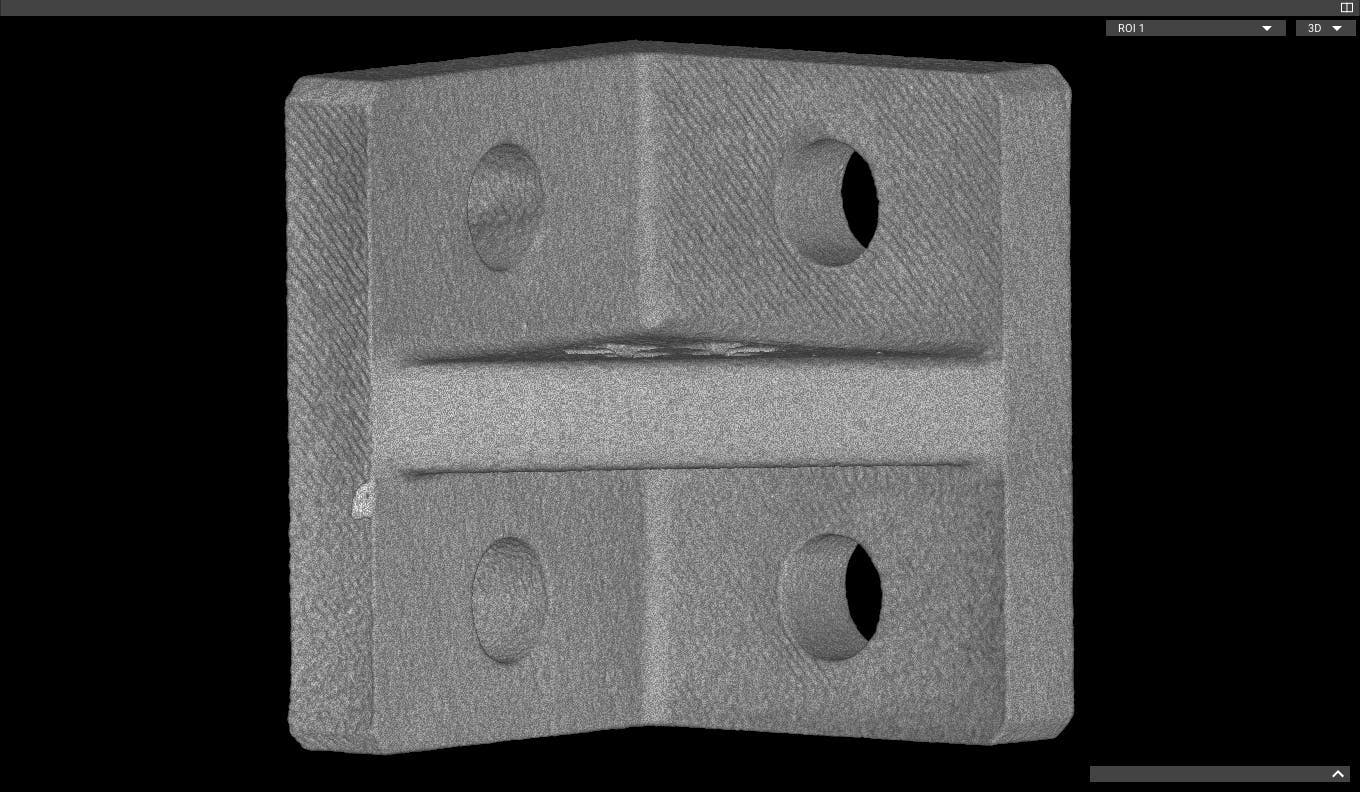
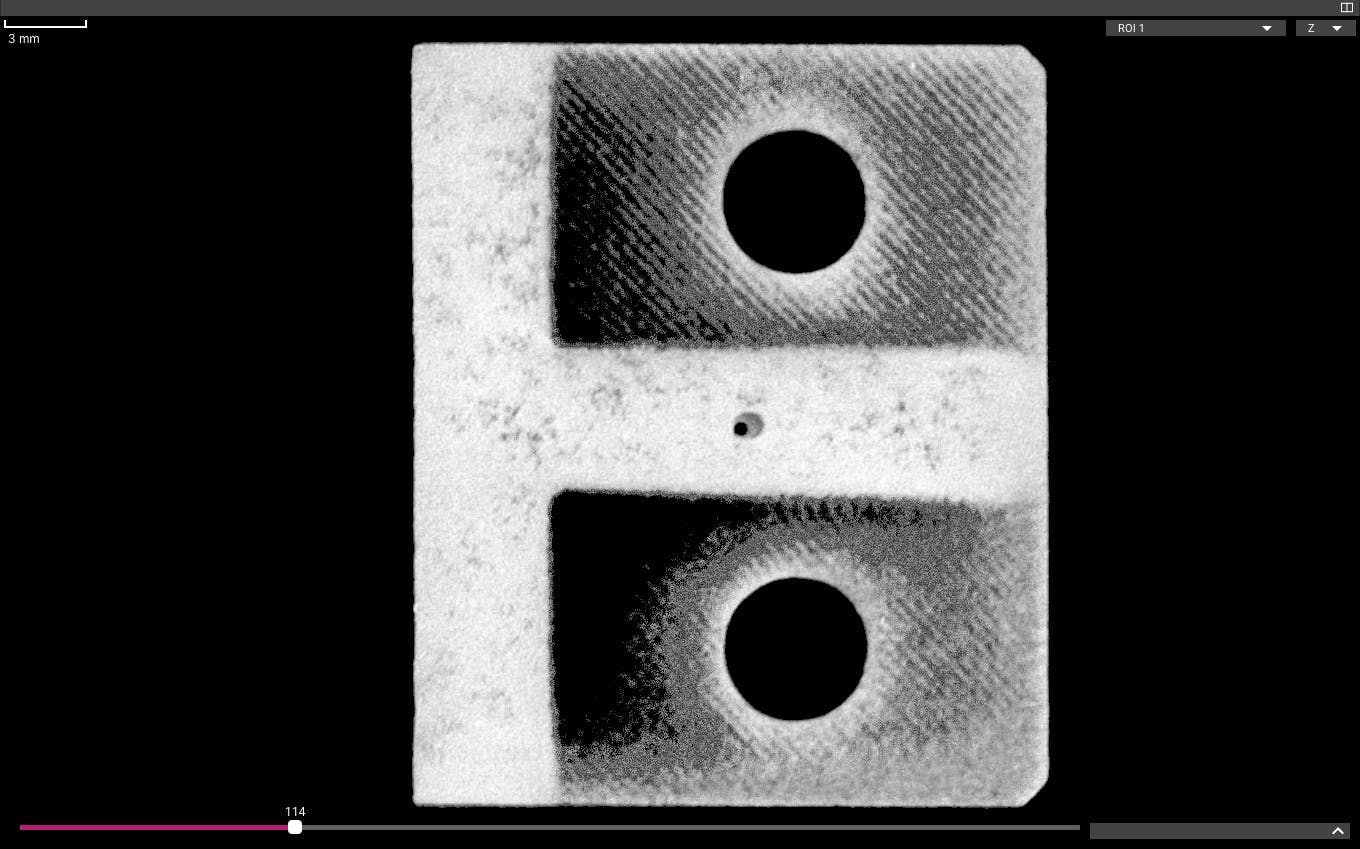
Accuracy
Thermal printing processes can introduce warping and other dimensional problems. This part turned out well, however; the Lumafield logo is sharp, and even the fine internal channel stays close to its 1 mm nominal diameter throughout its length.
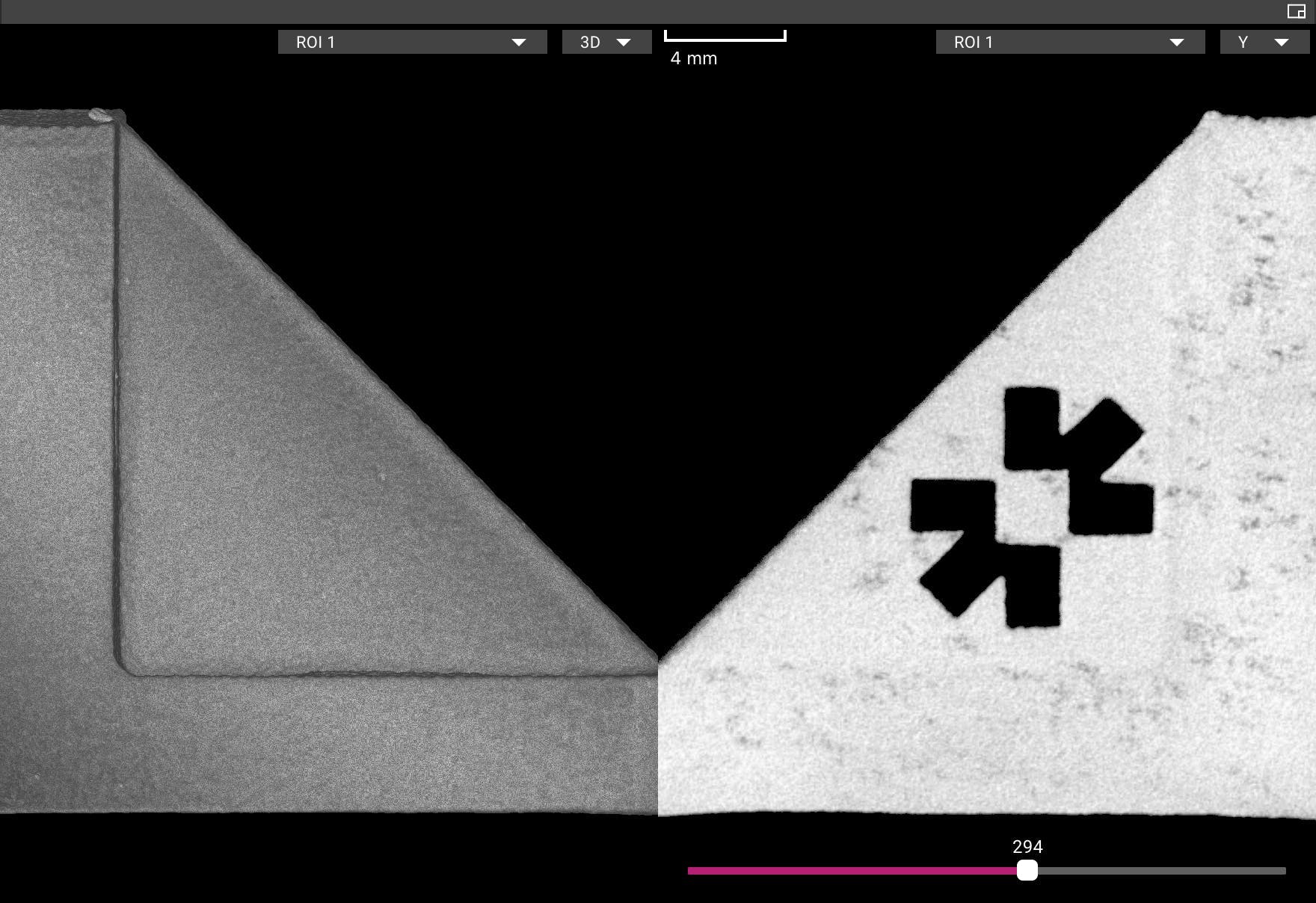
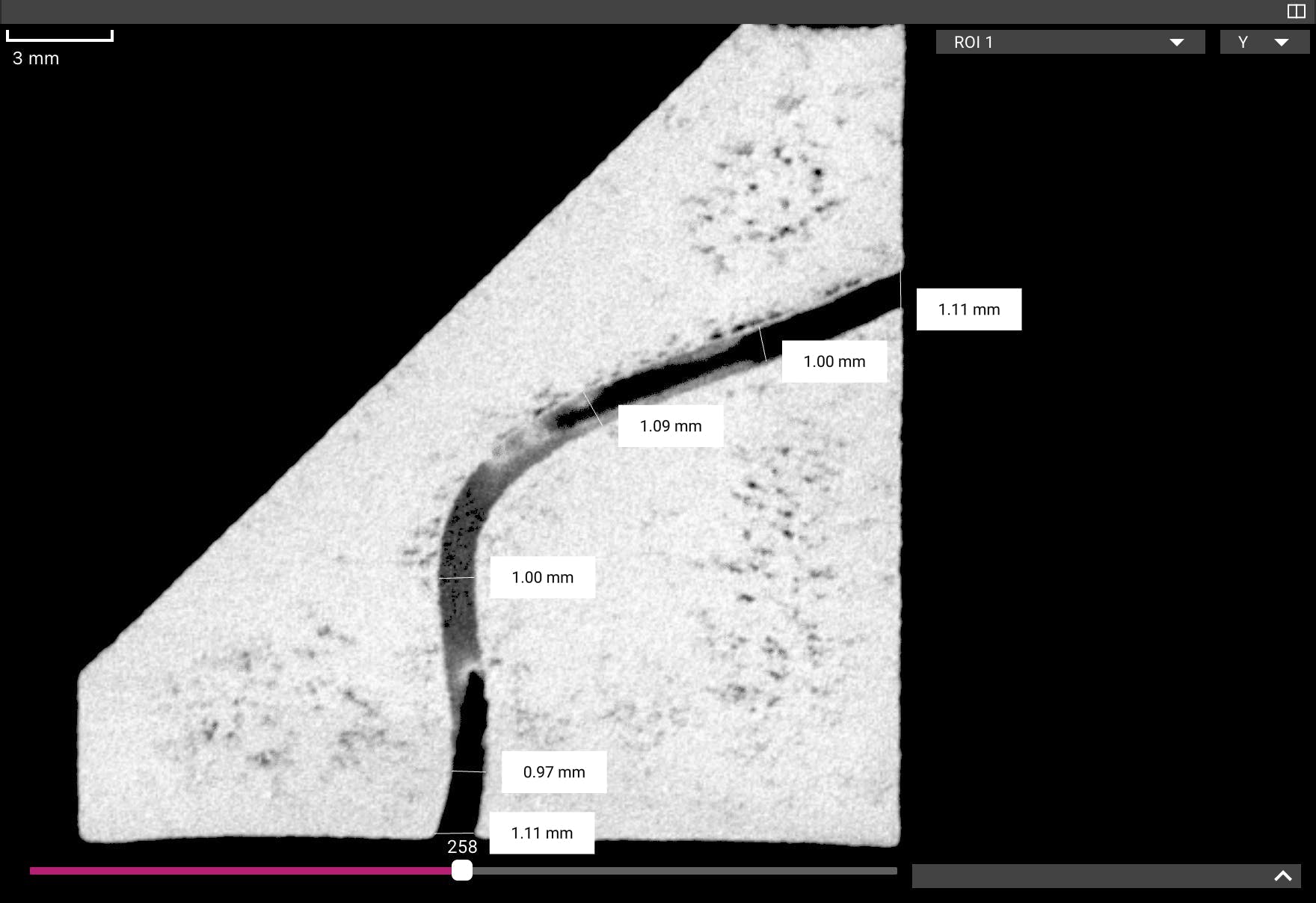
Other Articles in the Series
- Main page: Inspect 3D printed parts with industrial CT
- Fused Deposition Modeling (FDM)
- Selective Laser Sintering (SLS)
- Stereolithography (SLA)
- Direct Metal Laser Sintering (DMLS)